Harness the Power of Industrial Welding Robots: A Game-Changer for Manufacturing
## Introduction: Empower Your Fabrication Operations
Industrial welding robots are revolutionizing the manufacturing landscape, enabling businesses to enhance productivity, reduce costs, and improve product quality. These advanced machines offer unparalleled accuracy, efficiency, and scalability, transforming the way companies approach welding tasks.
Feature |
Benefits |
Precision Welding |
Exceptional quality and repeatability |
High Speed and Accuracy |
Increased production rates |
Reduced Labor Costs |
Significant savings on labor expenses |
Flexible Automation |
Adaptable to diverse welding applications |
## Success Stories: Embracing the Power of Welding Robots
Case Study: A Leading Automotive Manufacturer
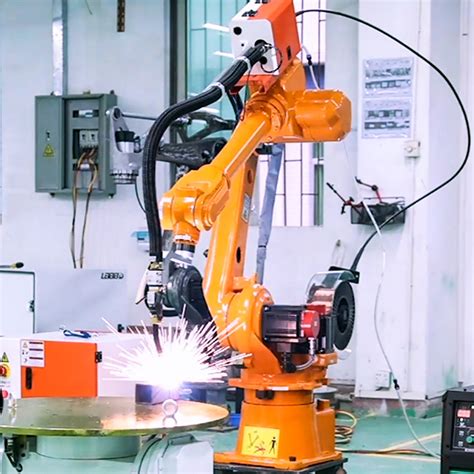
- Implemented industrial welding robots to automate the welding of automotive chassis components
- Results: 50% increase in production capacity, 25% reduction in welding defects
Case Study: A Heavy Equipment Manufacturer
- Deployed industrial welding robots for the fabrication of large-scale industrial equipment
- Results: 30% increase in weld consistency, 20% reduction in rework costs
Case Study: A Construction Company
- Utilized industrial welding robots to streamline the welding of structural steel components for high-rise buildings
- Results: 40% reduction in welding time, 15% improvement in weld quality
## Effective Strategies for Optimizing Welding Robot Operations
-
Invest in high-quality equipment: Choose industrial welding robots from reputable manufacturers to ensure precision and longevity.
-
Proper training and maintenance: Train operators thoroughly and implement regular maintenance schedules to keep robots operating at peak performance.
-
Analyze welding processes: Identify bottlenecks and areas for improvement to optimize robot utilization and efficiency.
-
Monitor and adjust parameters: Regularly review and adjust welding parameters to ensure optimal results and prevent defects.
-
Use simulation and testing: Leverage simulation software and testing procedures to validate weld quality and optimize robot parameters before production.
## Why Industrial Welding Robots Matter: Key Benefits
-
Enhanced Safety: Robots eliminate the risk of repetitive and hazardous welding tasks for human operators.
-
Increased Productivity: Continuous and tireless operation maximizes production capacity and reduces lead times.
-
Improved Quality: Precision welding and consistent parameters ensure high-quality welds with minimal defects.
-
Reduced Costs: Automation eliminates labor costs and minimizes rework expenses.
-
Increased Flexibility: Robots can be easily reprogrammed for different welding tasks, improving adaptability.
## Challenges and Limitations: Potential Drawbacks and Mitigating Risks

-
High initial investment: The acquisition of industrial welding robots can require significant capital investment.
-
Skills gap: Implementing welding robots requires skilled technicians and operators who are familiar with robotics and programming.
-
Maintenance and repair costs: Regular maintenance and potential repairs can add to operating expenses.
-
Downtime: Unplanned downtime due to technical issues or maintenance can disrupt production schedules.
-
Integration with existing processes: It is crucial to carefully integrate industrial welding robots with existing workflows to avoid disruptions.
## Industry Insights: Maximizing Efficiency
-
Industry 4.0 Integration: Integrate welding robots with automation, data analytics, and IoT solutions for increased efficiency.
-
Advanced Sensing and Inspection: Utilize vision systems and sensors for real-time monitoring and weld quality inspection.
-
Collaborative Robotics: Consider collaborative robots that work alongside human operators to enhance safety and productivity.
-
Remote Monitoring and Diagnostics: Implement remote monitoring systems to track robot performance and identify potential issues early on.
-
Predictive Maintenance: Leverage predictive maintenance technologies to anticipate and prevent robot downtime.