Industrial Robots: Redefining Manufacturing with Enhanced Efficiency and Precision
Industrial robots, the backbone of modern manufacturing, have revolutionized production processes, unlocking unprecedented levels of efficiency, precision, and flexibility. With their inherent capabilities and advanced features, these machines are transforming industries, creating a competitive landscape where automation takes center stage.
The Evolution of Industrial Robots: A Historical Perspective
The genesis of industrial robots can be traced back to the 1950s, when the first programmable manipulator was developed by George Devol in the United States. Initially designed for simple tasks like welding and material handling, these early robots laid the foundation for the sophisticated machines we use today.
Over the decades, advancements in technology, particularly in electronics, software, and sensors, have significantly enhanced the capabilities of industrial robots. The transition from traditional mechanical systems to modern computer-controlled robots has paved the way for greater precision, adaptability, and versatility.
Types of Industrial Robots: Applications Across Industries
The diversity of industrial robots is evident in their various configurations and applications. Depending on the tasks they are designed to perform, these robots can be categorized into different types:
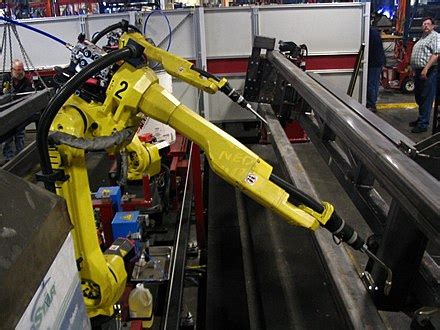
- Articulated Robots: With their versatile range of motion, these robots resemble the human arm, making them ideal for assembly, welding, and painting.
- Cartesian Robots: Also known as gantry robots, they move along three linear axes, providing precision and speed for repetitive tasks like pick-and-place operations.
- Delta Robots: Featuring a parallel-link structure, these robots excel in high-speed packaging and assembly applications.
- SCARA Robots: Designed specifically for assembly tasks, SCARA robots offer high speed and accuracy in compact spaces.
- Collaborative Robots (Cobots): These robots work safely alongside human operators, enabling increased productivity and reduced labor costs.
Benefits of Industrial Robot Implementation: Transforming Manufacturing
The integration of industrial robots into manufacturing processes offers a multitude of benefits, driving efficiency, quality, and innovation:

- Enhanced Productivity: Robots work tirelessly, increasing throughput and reducing cycle times. Their consistent performance minimizes downtime and improves overall productivity.
- Improved Quality: By eliminating human error and providing precise movements, robots ensure consistent product quality, meeting stringent standards.
- Reduced Labor Costs: Robots automate repetitive and labor-intensive tasks, allowing human workers to focus on higher-value activities. This optimization reduces labor costs and improves profitability.
- Enhanced Flexibility: Robots are easily reprogrammed to adapt to changes in production requirements, providing flexibility to handle product variations and market demands.
- Improved Safety: Robots perform hazardous tasks, reducing the risk of accidents and injuries for human operators. This creates a safer work environment, promoting employee well-being.
How Industrial Robots Are Used in Practice: Industry-Specific Applications
The versatility of industrial robots extends across a wide range of industries, each benefiting from their unique capabilities:
- Automotive Industry: Robots are extensively used in welding, assembly, and painting, improving efficiency and precision in vehicle production.
- Electronics Industry: Robots assemble delicate components with high speed and accuracy, ensuring quality and reducing defects.
- Food and Beverage Industry: Robots automate packaging, palletizing, and sorting processes, maintaining product integrity and hygiene.
- Medical Industry: Robots assist in precise surgical procedures, providing enhanced accuracy and minimizing patient recovery time.
- Logistics Industry: Robots automate warehouse operations, including order fulfillment, inventory management, and shipping.
Advanced Features of Industrial Robots: Pushing Boundaries
Modern industrial robots are equipped with advanced features that enhance their capabilities and versatility:
- Vision Systems: Integrated cameras allow robots to "see" their surroundings, enabling precise object recognition and manipulation.
- Sensors: Various sensors, such as force, torque, and proximity sensors, provide robots with detailed information about their environment, allowing for adaptive and intelligent behavior.
- Artificial Intelligence (AI): AI algorithms empower robots with learning and decision-making capabilities, enabling them to handle complex tasks and optimize performance.
- Cloud Connectivity: Robots can connect to cloud platforms, facilitating remote monitoring, predictive maintenance, and data analytics.
Common Mistakes to Avoid in Industrial Robot Implementation
To maximize the benefits of industrial robot implementation, it is crucial to avoid common pitfalls:

- Underestimating Planning: Thorough planning and analysis are essential to identify the right robot for the specific application and ensure successful integration.
- Neglecting Safety: Safety is paramount when deploying industrial robots. Proper risk assessments and safety measures must be implemented to protect both human operators and the equipment.
- Overestimating Capabilities: Robots have limitations, and it is important to set realistic expectations and avoid overloading them with tasks beyond their capabilities.
- Lack of Training: Operators must receive proper training to ensure safe and efficient operation of industrial robots. Comprehensive training programs are crucial for maximizing productivity and minimizing risks.
- Inadequate Maintenance: Regular maintenance is essential to keep industrial robots functioning optimally. A proactive maintenance schedule ensures reliability and extends the lifespan of the equipment.
How to Implement Industrial Robots Step-by-Step
Successful industrial robot implementation requires a methodical approach:
-
1. Assess Needs: Conduct a thorough analysis of production processes to identify areas where robots can add value and improve efficiency.
-
2. Research and Select: Explore different robot types, consider their capabilities, and select the most suitable robot for the specific application.
-
3. Design and Plan: Design the robot's layout, consider safety measures, and integrate it into the existing production environment.
-
4. Installation and Commissioning: Install the robot and all necessary peripherals, ensuring proper calibration and testing.
-
5. Programming and Training: Program the robot to perform the desired tasks and train operators on safe and efficient operation.
-
6. Monitoring and Evaluation: Continuously monitor robot performance, collect data, and make adjustments as needed to optimize productivity and efficiency.
Why Industrial Robots Matter: A Catalyst for Growth
Industrial robots are not merely machines; they are transformative tools that drive economic growth and innovation:
- Productivity Boost: Robots increase production output, reduce costs, and enhance overall productivity, contributing to business growth and profitability.
- Competitiveness Enhancement: By adopting industrial robots, businesses gain a competitive edge by improving efficiency and quality, meeting market demands effectively.
- Technological Advancement: Robots foster innovation and technological advancements, leading to the development of new products, processes, and services.
- Job Creation: While robots automate certain tasks, they also create new job opportunities in areas such as robot design, maintenance, and programming.
- Sustainable Manufacturing: Robots contribute to sustainable manufacturing by reducing waste, improving energy efficiency, and enabling environmentally friendly practices.
Case Studies: Industrial Robots in Real-World Applications
Numerous success stories highlight the transformative impact of industrial robots:
-
Automotive Industry: Ford Motor Company implemented robots in its Dearborn Truck Plant, achieving a 20% increase in production efficiency and a reduction in assembly time by 50%.
-
Electronics Industry: Foxconn, a major electronics manufacturer, deployed over 1 million robots in its Chinese factories, resulting in a significant increase in production capacity and a reduction in labor costs.
-
Healthcare Industry: Intuitive Surgical's da Vinci Surgical System, a robotic platform for minimally invasive surgery, has enabled surgeons to perform complex procedures with greater precision and reduced patient recovery time.
Tips for Selecting the Right Industrial Robot
When selecting an industrial robot, consider the following factors:
-
Payload Capacity: Determine the weight of the objects the robot will handle.
-
Reach: Consider the required workspace and the distance the robot needs to travel.
-
Speed and Accuracy: Assess the desired cycle time and accuracy requirements.
-
Application: Identify the specific tasks the robot will be performing.
-
Cost: Evaluate the budget and return on investment.
Stories from the Industrial Robot World
-
The Robot that Forgot its Place: A robot in a warehouse was programmed to move pallets from one location to another. However, due to a software glitch, it kept going back to the same location, creating a hilarious loop.
-
The Robot that Went on a Coffee Break: Another robot in a food processing plant was programmed to pick and place products. One day, it decided to pause its operation and went to the break room to get a cup of coffee, leaving the production line in disarray.
-
The Robot that Played Matchmaker: A robot in a dating app was programmed to match people based on their interests. However, it accidentally matched a cat lover with a dog lover, leading to an unexpected and humorous encounter.
Conclusion: Embracing the Future of Manufacturing
Industrial robots have become an integral part of modern manufacturing, unlocking new levels of efficiency, precision, and innovation. By embracing these advanced machines, businesses can gain a competitive edge, enhance productivity, and pave the way for a more sustainable future. With their transformative capabilities, industrial robots are not only shaping the future of manufacturing but also redefining the very nature of work and the possibilities for human ingenuity.
