The Welding Revolution: Unlocking Efficiency with Industrial Welding Robots
The welding industry is evolving at an unprecedented pace, driven by the relentless pursuit of efficiency, quality, and precision. Industrial welding robots have emerged as game-changers, transforming welding processes and unlocking a world of possibilities for businesses. Join us as we delve into the captivating world of industrial welding robots, exploring their multifaceted benefits, advanced features, and transformative impact on the manufacturing landscape.
Embracing Innovation: The Rise of Industrial Welding Robots
The advent of industrial welding robots has revolutionized the welding industry, offering a myriad of advantages over traditional manual welding methods. These automated marvels boast exceptional speed, accuracy, and consistency, ensuring impeccable weld quality with minimal human intervention. Their tireless operation enables 24/7 production, boosting productivity and minimizing downtime. With the ever-evolving advancements in technology, industrial welding robots are now equipped with sophisticated sensors and software, empowering them to adapt to complex weld geometries and handle intricate tasks with ease.
The Economic Impact: Quantifying the Benefits
According to the International Federation of Robotics, the global market for industrial robots is projected to reach a staggering $271 billion by 2030. This surge in adoption is attributed to the compelling economic benefits they deliver. Industrial welding robots can enhance output by up to 40%, significantly reducing labor costs and production timeframes. Moreover, their exceptional precision and accuracy minimize material wastage, leading to cost savings and increased profitability.
Unlocking the Capabilities of Industrial Welding Robots: A Comprehensive Guide
Industrial welding robots are true workhorses, capable of undertaking a wide range of welding tasks with remarkable proficiency. Their versatility extends from simple spot welding to complex arc welding, catering to diverse industry needs. These robots can effortlessly handle intricate welds, weld in confined spaces, and even perform underwater welding operations. With their ability to execute repetitive tasks with unmatched precision, industrial welding robots excel in industries such as automotive, shipbuilding, and heavy equipment manufacturing.
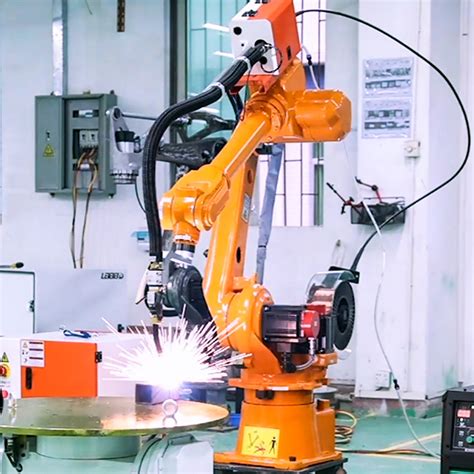
The Benefits That Drive Success
The advantages of incorporating industrial welding robots into your operations are undeniable. These robots:

-
Boost Productivity: Their tireless operation and rapid welding speeds translate into increased output and shorter production times.
-
Enhance Quality: Precision welding eliminates defects and inconsistencies, resulting in superior product quality and customer satisfaction.
-
Reduce Costs: Labor savings, minimized material wastage, and decreased rework expenses contribute to significant cost reductions.
-
Improve Safety: Robots eliminate the exposure of human welders to hazardous fumes, sparks, and heavy lifting, creating a safer work environment.
-
Increase Flexibility: Advanced robots can adapt to changing production demands, handle multiple tasks, and seamlessly integrate with other automation systems.
Common Mistakes to Avoid: A Path to Success
While industrial welding robots offer a wealth of benefits, it's crucial to avoid common pitfalls that can hinder their effectiveness. Thorough planning and diligent execution are essential to reap the full rewards of these technological marvels. Here are some常见的失误和避免方法:

-
Inadequate Training: Ensure that operators and maintenance personnel receive comprehensive training to maximize robot performance and safety.
-
Poor Programming: Optimize robot programming to prevent errors, ensure precision, and avoid costly rework.
-
Neglecting Maintenance: Regular maintenance and calibration are vital to maintain optimal robot performance and prevent costly breakdowns.
-
Overlooking Safety: Prioritize safety measures, including proper guarding, training, and adherence to established safety protocols.
-
Lack of Integration: Seamlessly integrate robots into existing production processes to avoid disruptions and maximize efficiency.
Advanced Features: The Cutting Edge of Welding Technology
The latest industrial welding robots are equipped with groundbreaking features that push the boundaries of welding capabilities. These advancements empower robots to tackle even the most demanding tasks with unparalleled precision and efficiency.
Embracing the Future: Innovative Features
-
Collaborative Robots (Cobots): These robots work alongside human welders, enhancing productivity and safety while enabling a more flexible work environment.
-
Artificial Intelligence (AI): AI-powered robots can analyze weld data, optimize welding parameters, and autonomously detect and correct errors, ensuring consistent high-quality welds.
-
Laser Welding: Laser welding robots utilize concentrated beams of light to produce precise and intricate welds, ideal for delicate applications and dissimilar material joining.
-
3D Printing Integration: Robots can seamlessly integrate with 3D printing processes, enabling the production of complex welded structures directly from digital designs.
-
Welding Simulation Software: Advanced simulation software enables offline programming and testing of welding processes, reducing setup time and optimizing robot performance.
Potential Drawbacks: A Balanced Perspective
Despite their remarkable capabilities, industrial welding robots are not without potential drawbacks that must be carefully considered.
Considerations for Implementation
-
High Initial Investment: The acquisition and implementation of industrial welding robots require a significant upfront investment.
-
Skilled Labor Requirements: Programming, maintenance, and operation of industrial welding robots necessitate specialized skills, which may require additional training or hiring.
-
Limited Flexibility: While robots offer versatility, they may not be suitable for all welding applications, particularly those requiring extensive human intervention or customization.
-
Safety Concerns: Improper installation, operation, or maintenance of industrial welding robots can pose safety risks, highlighting the need for comprehensive safety measures.
-
Environmental Impact: The energy consumption and disposal of industrial welding robots must be carefully managed to minimize their environmental footprint.
Comparing Pros and Cons: Weighing the Evidence
To make an informed decision about incorporating industrial welding robots into your operations, carefully weigh the advantages and disadvantages:
Pros |
Cons |
Increased Productivity |
High Initial Investment |
Improved Quality |
Skilled Labor Requirements |
Reduced Costs |
Limited Flexibility |
Enhanced Safety |
Safety Concerns |
Increased Flexibility |
Environmental Impact |
FAQs: Unraveling Common Questions
Here are answers to frequently asked questions regarding industrial welding robots:
-
What industries benefit most from industrial welding robots?
- Automotive, shipbuilding, heavy equipment manufacturing, aerospace, and construction industries are prime candidates for industrial welding robots.
-
How do industrial welding robots improve safety?
- Robots eliminate human exposure to hazardous fumes, sparks, and heavy lifting, creating a safer work environment.
-
Are industrial welding robots easy to program?
- Modern industrial welding robots feature intuitive programming interfaces that simplify the learning curve for operators.
-
How much do industrial welding robots cost?
- The cost of industrial welding robots varies depending on size, capabilities, and features, but typically range from $50,000 to $500,000.
Inspiring Stories: Lessons from the Field
-
The Curious Case of the Misaligned Robot: A welding robot was persistently producing misaligned welds. After hours of troubleshooting, it was discovered that a playful cat had knocked the robot's laser pointer out of alignment, causing the robot to weld off-center.
-
The Robot's Uncanny Accuracy: In a high-stakes welding competition, an industrial welding robot astounded the judges by welding a perfect circle, demonstrating its exceptional precision and reliability.
-
The Robot that Saved Christmas: During a holiday production rush, an industrial welding robot heroically welded thousands of toys overnight, ensuring that children would wake up to gifts on Christmas morning.
Call to Action: Embracing the Future of Welding
The time is ripe to embrace the transformative power of industrial welding robots. With their unparalleled efficiency, precision, and versatility, these technological marvels can revolutionize your welding operations, driving productivity, quality, and profitability to new heights. Contact our team of experts today to schedule a consultation and unlock the future of welding in your organization. Let us guide you on the path to welding excellence and empower your business with the competitive edge it deserves.