Master the Art of Industrial Welding with Cutting-Edge Robots: A Comprehensive Guide
A Symbiotic Alliance in Modern Manufacturing
In the ever-evolving landscape of industrial manufacturing, the integration of welding robots has emerged as a transformative force. These sophisticated machines are revolutionizing the way we fabricate and assemble metal components, offering a plethora of benefits that elevate efficiency, precision, and safety in the workplace.
Unlocking the Potential of Welding Robots
The adoption of welding robots has catapulted the manufacturing industry into a new era of productivity and competitiveness. By harnessing the power of automation, these robotic systems can execute complex welding tasks with unmatched speed, accuracy, and consistency. This translates into significant reductions in manufacturing lead times and production costs, enabling businesses to meet the demands of a rapidly evolving global marketplace.
Industry-Specific Advantages
Each industry reaps unique dividends from the deployment of welding robots. In the automotive sector, for instance, these machines play a pivotal role in the assembly of vehicle frames, doors, and other critical components. The aerospace industry leverages robotic welding to construct lightweight yet robust aircraft structures, ensuring safety and fuel efficiency. Similarly, in the shipyards, welding robots streamline the fabrication of hulls and other complex structures, enhancing the overall productivity and quality of the shipbuilding process.
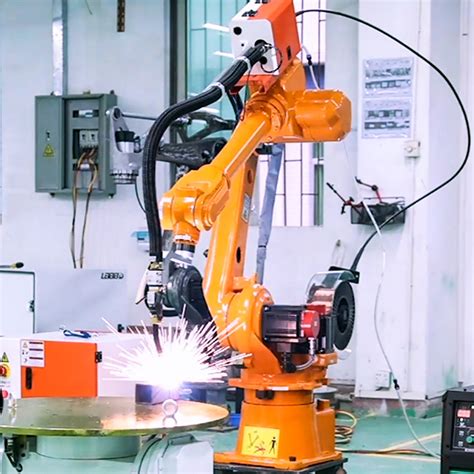
Key Benefits of Robotic Welding
The benefits of deploying welding robots extend far beyond increased efficiency and cost savings. These machines offer a host of advantages that have a profound impact on the overall competitiveness and success of manufacturing businesses.

-
Enhanced Productivity: Robots operate tirelessly 24/7, without the need for breaks or vacations, maximizing production output and minimizing downtime.
-
Superior Precision: Equipped with advanced sensors and computer-controlled systems, welding robots deliver exceptional precision and repeatability, ensuring consistent weld quality and reducing the risk of defects.
-
Improved Safety: Robots eliminate the need for human exposure to hazardous welding fumes, sparks, and molten metal, minimizing the risk of workplace accidents and injuries.
-
Versatility: Robots excel at handling a wide range of welding applications, from simple spot welding to complex arc welding processes, providing flexibility and adaptability to changing production demands.
-
Reduced Labor Costs: While welding robots represent a substantial upfront investment, their long-term cost savings are undeniable. They eliminate the need for overtime pay, sick leave, and other employee-related expenses.
-
Improved Quality Control: By eliminating human error from the welding process, robots ensure consistent weld quality, reducing the risk of product defects and rework, which ultimately enhances customer satisfaction.
The Costs of Robotic Welding
The cost of implementing robotic welding systems can vary depending on the specific application, the size and complexity of the robot, and the required peripherals. However, it is essential to consider the long-term return on investment (ROI) when evaluating the affordability of robotic welding. The potential savings in labor costs, increased productivity, and improved quality can far outweigh the initial investment, leading to a substantial payback period.
Choosing the Right Welding Robot
Selecting the ideal welding robot for your specific application requires careful consideration of several key factors:
-
Payload: The robot's payload capacity should be sufficient to handle the weight of the welding torch and the workpiece being welded.
-
Reach: The robot's reach must be sufficient to cover the entire welding area, ensuring access to all critical welding points.
-
Speed: The robot's welding speed should be compatible with the production requirements, considering factors such as the type of weld joint and the material thickness.
-
Accuracy: The robot's accuracy plays a crucial role in ensuring weld quality and consistency, minimizing the risk of defects and rework.
-
Safety Features: The robot should be equipped with safety features such as emergency stop buttons, collision detection systems, and interlocks to prevent accidents and injuries.
Effective Strategies for Successful Implementation
To maximize the benefits of robotic welding, it is essential to adopt effective implementation strategies. These include:
-
Proper Planning: Thorough planning is crucial for a successful robotic welding implementation, including identifying application requirements, selecting the appropriate equipment, and developing a comprehensive training program.
-
Operator Training: Operators should receive comprehensive training on the specific robot and welding process to ensure safe and efficient operation.
-
Maintenance: Regular maintenance and calibration of the robot are paramount to ensure optimal performance, prevent breakdowns, and extend the lifespan of the equipment.
-
Continuous Improvement: Embrace a culture of continuous improvement by monitoring welding performance, identifying areas for optimization, and implementing ongoing training and upgrades.
Common Mistakes to Avoid
Implementing robotic welding systems can be a complex undertaking, and it is crucial to avoid common pitfalls to ensure a successful deployment. These include:

-
Underestimating Installation Costs: Failing to account for the full cost of installation, including site preparation, electrical upgrades, and operator training, can lead to budget overruns and project delays.
-
Ignoring Training: Inadequate training of operators can result in improper operation, safety hazards, and reduced productivity, negating the potential benefits of robotic welding.
-
Neglecting Maintenance: Failing to adhere to recommended maintenance schedules can lead to premature breakdowns, costly repairs, and reduced robot lifespan.
-
Lack of Integration: Failure to integrate the robot with other production systems, such as material handling and quality control, can result in inefficiencies and production bottlenecks.
Why Robotic Welding Matters
The adoption of welding robots is not merely a technological upgrade; it is a strategic investment that transforms manufacturing operations. By automating complex welding tasks, businesses can achieve:
-
Increased Productivity and Reduced Costs: Robots operate tirelessly and consistently, maximizing production output while reducing labor costs and overtime expenses.
-
Enhanced Quality and Reliability: Robots eliminate human error from the welding process, ensuring consistent weld quality, reducing defects, and enhancing product reliability.
-
Improved Safety and Ergonomics: Robots eliminate the need for human exposure to hazardous welding fumes and sparks, improving workplace safety and reducing the risk of repetitive strain injuries.
-
Innovation and Competitiveness: Robotic welding enables the adoption of advanced welding technologies, such as laser welding and friction stir welding, enhancing manufacturing capabilities and increasing competitiveness.
The Pros and Cons of Robotic Welding
As with any technology, robotic welding has both advantages and disadvantages. It is important to carefully consider these factors when evaluating its suitability for your specific application.
Pros |
Cons |
Increased productivity |
High upfront investment |
Enhanced quality and consistency |
Requires skilled operators |
Improved safety |
Training can be time-consuming |
Reduced labor costs |
Maintenance and repairs can be costly |
Versatility and adaptability |
Not suitable for all welding applications |
Frequently Asked Questions (FAQs)
-
What is the payback period for a robotic welding system? The payback period can vary depending on the specific application and production volume, but it is typically in the range of 2-5 years.
-
Can welding robots be used for all types of welding? While welding robots are capable of handling a wide range of welding applications, they may not be suitable for all types of welding, such as manual arc welding or underwater welding.
-
How much maintenance is required for a welding robot? Regular maintenance is essential for optimal performance and longevity of the robot, including daily inspections, periodic lubrication, and scheduled maintenance intervals.
-
What safety precautions should be taken when working with welding robots? Safety precautions include wearing appropriate personal protective equipment, maintaining a safe working distance, and following established safety procedures.
-
How can I learn more about robotic welding? Numerous resources are available online, including technical articles, webinars, and training courses, to help you gain a deeper understanding of robotic welding.
-
Who are the leading manufacturers of welding robots? Some of the leading manufacturers of welding robots include ABB, Fanuc, Yaskawa, KUKA, and Kawasaki.
Humorous Stories and Lessons Learned
-
The Robot Who Was Always Hungry: A welding robot was programmed to stop welding every time it heard a loud noise. One day, the robot stopped welding every time the factory manager shouted at his employees. Lesson learned: Define clear parameters and test the robot thoroughly before deploying it in a production environment.
-
The Robot Who Went on a Rampage: A welding robot was not properly calibrated and started welding random objects on the factory floor, including a forklift and a supervisor's desk. Lesson learned: Always double-check the robot's programming and safety features before starting production.
-
The Robot Who Fell in Love: A welding robot was programmed to follow a laser pointer. One day, a mischievous employee pointed the laser pointer at a female robot on the other side of the factory. The welding robot proceeded to follow the laser pointer, welding all the way across the factory floor. Lesson learned: Keep an eye on your robots and make sure they are not distracted by external stimuli.
Call to Action
Embracing robotic welding is a transformative step towards enhancing productivity, improving quality, and increasing competitiveness in the modern manufacturing landscape. By partnering with [Robot Welding Solutions], you can access the expertise, experience, and cutting-edge technology necessary to unlock the full potential of robotic welding in your operations. With a comprehensive range of welding robots, tailored integration services, and ongoing support, we empower you to achieve your manufacturing goals and drive your business forward.
Contact us today for a consultation and discover how robotic welding can revolutionize your manufacturing processes. Together, let us transform your operations and forge a path to manufacturing excellence.
[Website URL]
[Contact Information]