Cobots vs Industrial Robots: A Guide to Collaborative and Automated Manufacturing
In the rapidly evolving landscape of modern manufacturing, the debate between cobots and industrial robots rages on. While both types of robots offer unique advantages, understanding their distinctions is crucial for businesses seeking to enhance their production capabilities. This comprehensive guide will delve into the realm of collaborative robots (cobots) and industrial robots, highlighting their key differences, benefits, and applications.
Understanding Cobots: A Human-Centric Approach
Cobots, short for collaborative robots, represent a groundbreaking approach to robotic manufacturing. These robots are designed to work alongside human employees, providing assistance and enhancing their productivity. Unlike traditional industrial robots confined to designated workspaces, cobots are equipped with advanced sensors that allow them to interact safely with humans. This collaboration fosters a harmonious work environment where robots and humans complement each other's strengths, fostering innovation and efficiency.
Benefits of Cobots: Unleashing Human Potential
-
Enhanced Productivity: Cobots seamlessly integrate into existing production lines, augmenting human capabilities and increasing overall productivity.
-
Improved Safety: Advanced sensors and safety protocols ensure safe human-robot interaction, reducing the risk of accidents and injuries.
-
Versatility: Cobots excel in various tasks, including assembly, packaging, and material handling, offering greater flexibility and adaptability to changing production demands.
-
Easy to Program: Designed with user-friendly interfaces, cobots can be programmed quickly and easily, reducing downtime and empowering non-technical personnel.
Applications of Cobots: Driving Innovation Across Industries
Cobots find widespread application in diverse industries, including:

-
Automotive: Collaborative robots assist in assembly, welding, and painting tasks, enhancing efficiency and precision.
-
Electronics: Cobots contribute to assembly, testing, and packaging processes, ensuring quality and reducing labor costs.
-
Pharmaceuticals: Cobots facilitate automated packaging and sterile manufacturing, maintaining high standards of hygiene and accuracy.
-
Food and Beverage: Robots assist in food packaging, quality inspection, and material handling, promoting safety and efficiency.
Industrial Robots: Precision and Automation at Scale
Industrial robots have long played a vital role in automating repetitive and complex tasks in manufacturing environments. These robots are typically fixed in place, performing highly specialized operations with precision and speed. They are indispensable for mass production, reducing labor costs and ensuring consistent quality.
Benefits of Industrial Robots: Unlocking Efficiency
-
Increased Speed and Accuracy: Industrial robots excel at repetitive tasks, operating at high speeds with unmatched precision, minimizing defects and maximizing productivity.
-
Heavy Payload Handling: Designed to handle heavy objects, industrial robots facilitate efficient material handling, reducing manual labor and the risk of injuries.
-
Consistency and Quality: By eliminating human error, industrial robots ensure product consistency and quality, meeting stringent manufacturing standards.
-
24/7 Operation: Industrial robots can operate continuously, enabling uninterrupted production, maximizing production capacity, and reducing downtime.
Applications of Industrial Robots: Empowering Automation
Industrial robots are prevalent in industries such as:
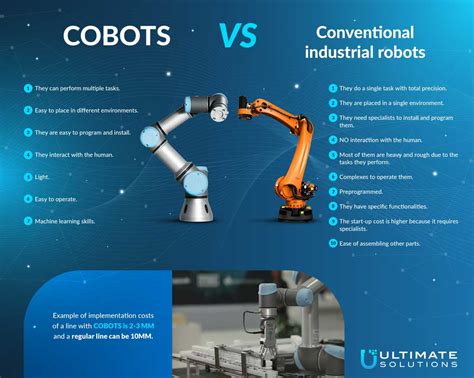
-
Automotive: Robots perform welding, painting, and assembly tasks with precision and speed, enabling large-scale production.
-
Electronics: Industrial robots facilitate automated assembly, testing, and sorting processes, ensuring high productivity and quality.
-
Pharmaceuticals: Robots contribute to automated packaging, filling, and labeling, maintaining sterility and compliance.
-
Metalworking: Robots excel in welding, cutting, and shaping metal components, ensuring precision and safety.
Choosing the Right Robot: A Strategic Decision
The choice between cobots and industrial robots hinges on specific manufacturing requirements. Cobots are ideal for collaborative tasks, enhancing human productivity and flexibility. Conversely, industrial robots are better suited for high-volume, repetitive tasks requiring precision and speed.
Factors to Consider: Guiding Your Decision
-
Task Complexity: Cobots excel in dynamic tasks requiring human-robot collaboration, while industrial robots handle complex, repetitive operations efficiently.
-
Safety: Collaborative robots prioritize human safety through advanced sensors and safety protocols. Industrial robots operate in controlled environments with safety barriers.
-
Cost: Cobots typically require lower upfront investment and are easier to integrate, while industrial robots may involve higher acquisition and deployment costs.
-
Scalability: Industrial robots are suitable for large-scale manufacturing due to their high speed and accuracy, while cobots offer greater flexibility for small-scale production.
Cobots vs Industrial Robots: A Comparison at a Glance
Feature |
Cobot |
Industrial Robot |
Definition |
Collaborative, works alongside humans |
Automated, fixed in place |
Interaction |
Safe human-robot interaction |
Limited human interaction |
Programming |
User-friendly, easy to program |
Complex, requires specialized skills |
Flexibility |
Adaptable to changing tasks |
Specialized for specific tasks |
Cost |
Lower upfront investment |
Higher upfront investment |
Productivity |
Augments human productivity |
High-volume, repetitive tasks |
Applications |
Assembly, packaging, material handling |
Welding, painting, assembly, heavy payload handling |
Effective Strategies: Maximizing Robotic Potential
-
Identify Clear Objectives: Define the specific manufacturing needs and tasks best suited for robotic automation.
-
Evaluate Current Processes: Analyze existing workflows to identify areas where robots can add value and improve efficiency.
-
Choose the Right Robot: Carefully consider the factors outlined above to determine if cobots or industrial robots align better with your requirements.
-
Implement Thoroughly: Plan the robot's integration into the production line, including training for employees and ensuring safety protocols are in place.
-
Monitor and Improve: Regularly assess the robot's performance and make adjustments as needed to optimize productivity and efficiency.
Common Mistakes to Avoid: Pitfalls to Watch Out For
-
Underestimating Training Needs: Failure to provide adequate training to employees can hamper robot adoption and limit its potential benefits.
-
Ignoring Safety Protocols: Overlooking safety measures when working with robots can lead to accidents and injuries, compromising productivity.
-
Overestimating Robot Capabilities: Understanding the limitations of robots is crucial to avoid disappointment and maximize their deployment effectively.
-
Failing to Integrate Properly: Inadequate integration of robots into the production process can disrupt workflows and undermine efficiency gains.
-
Lack of Maintenance: Neglecting regular maintenance can lead to robot malfunctions, downtime, and productivity losses.
A Step-by-Step Approach: A Proven Path to Success
-
Define Goals: Establish clear production objectives and identify areas where robots can enhance performance.
-
Assess Needs: Conduct a thorough analysis of current processes and identify the most suitable robot type.
-
Plan Integration: Develop a comprehensive plan for robot implementation, including safety protocols, training, and workflow adjustments.
-
Implement and Train: Deploy the robot and provide thorough training to ensure safe and efficient operation.
-
Monitor and Evaluate: Regularly assess robot performance, gather feedback, and make necessary adjustments to optimize productivity.
Advanced Features: Enhancing Robotic Capabilities
Cobots and industrial robots offer a range of advanced features to enhance their functionality:
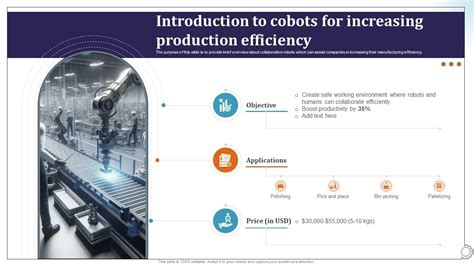
-
Computer Vision: Cameras and image processing capabilities enable robots to "see" their environment, facilitating object recognition and quality inspection.
-
Force Control: Sensors allow robots to apply precise force, enabling delicate assembly tasks and ensuring product quality.
-
AI and Machine Learning: Integration of AI and machine learning empowers robots to learn from data, adapt to changing conditions, and make autonomous decisions.
-
Cloud Connectivity: Robots can connect to the cloud, enabling remote monitoring, data analysis, and software updates, streamlining maintenance and optimization.
Pros and Cons: A Balanced Comparison
Cobots
Pros:
- Safe human-robot collaboration
- Easy to program and integrate
- Versatile and adaptable
- Reduce labor costs and enhance productivity
Cons:
- Lower speed and payload capacity than industrial robots
- May require additional safety measures
- Limited to collaborative tasks
Industrial Robots
Pros:
- High speed and precision
- Handle heavy payloads and repetitive tasks
- Ensure consistent product quality
- Operate 24/7, maximizing production capacity
Cons:
- Require specialized programming and maintenance
- Higher upfront investment costs
- Limited flexibility and adaptability
- Safety protocols must be strictly followed
FAQs: Answering the Most Common Questions
-
Can cobots replace human workers?
Cobots are designed to collaborate with humans, not replace them. They enhance human productivity and replace repetitive or hazardous tasks.
-
Are industrial robots dangerous?
Industrial robots operate in controlled environments and must follow strict safety protocols. Proper training and adherence to safety measures minimize the risk of accidents.
-
Which is better for small businesses: cobots or industrial robots?
Cobots are generally more suitable for small businesses due to their lower cost, ease of integration, and flexibility for diverse tasks.
Humorous Stories: Lessons Learned in Robotics
-
The Disappearing Robot:
A manufacturer installed a new industrial robot but was perplexed when it kept vanishing. Upon investigation, they discovered the robot was programmed to find the nearest outlet to recharge itself when low on battery, resulting in it disappearing into the factory's electrical system.
Lesson Learned: Ensure thorough testing and debugging before deploying robots to avoid unexpected behavior.
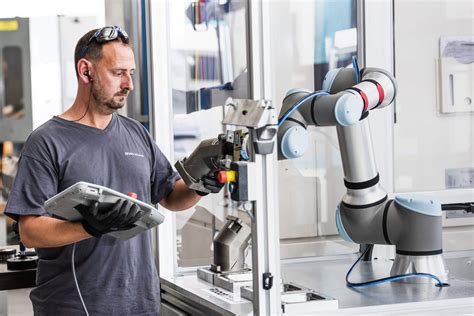
-
The Robot that Became a Dancer:
A cobot was deployed to assist in a warehouse but caused chaos when it started dancing unexpectedly. It turned out that the cobot's sensors mistook the rhythmical vibrations from nearby machinery for dance moves, triggering its programming to join in.
Lesson Learned: Consider the environmental factors that may affect robot behavior and program accordingly.
- **The Robot that Learned