Industrial Robots: Revolutionizing the Manufacturing Landscape
Industrial robots, the epitome of automation and precision, have transformed the manufacturing industry, ushering in an era of increased efficiency, productivity, and safety. Defined as programmable machines capable of performing diverse tasks with high accuracy and repeatability, these robotic marvels have become an indispensable asset in modern factories and warehouses.
History and Evolution
The genesis of industrial robots can be traced back to the mid-20th century, with the development of Unimate, the world's first operational industrial robot, in 1954. Initially designed for tasks involving material handling and welding, industrial robots have since evolved exponentially, incorporating advancements in robotics, computer science, and artificial intelligence.
Types of Industrial Robots
The diverse range of industrial applications has led to the development of various types of robots, each tailored to specific tasks. Prominent types include:
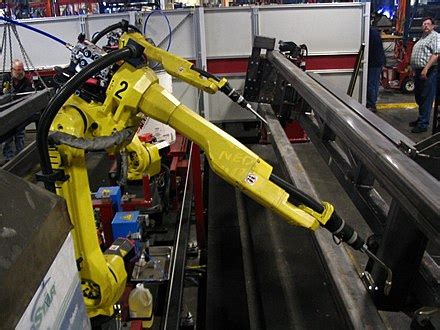
-
Articulated Robots: With their multiple rotating joints, articulated robots offer exceptional flexibility and can maneuver in complex spaces, making them suitable for complex assembly and painting tasks.
-
Cartesian Robots: Cartesian robots move along three linear axes (X, Y, Z), providing high precision for operations like pick-and-place and packaging.
-
Cylindrical Robots: Cylindrical robots combine vertical and radial movements, offering a versatile solution for tasks such as welding and assembly.
-
SCARA Robots: SCARA (Selective Compliance Assembly Robot Arm) robots feature a parallel kinematic structure that enables high-speed and precise movements, making them ideal for assembly and electronic component insertion.
-
Mobile Robots: Mobile robots, equipped with wheels or tracks, provide exceptional mobility, allowing them to navigate dynamic environments and perform tasks like transportation and inspection.
Applications in Industry
Industrial robots find widespread application across a multitude of industries, including:

-
Automotive: Welding, assembly, painting, and material handling
-
Electronics: Assembly, inspection, and testing
-
Food and Beverage: Packaging, processing, and quality control
-
Pharmaceuticals: Drug discovery, production, and packaging
-
Logistics: Warehouse automation, inventory management, and material handling
Benefits of Industrial Robots
The adoption of industrial robots brings forth numerous benefits for manufacturers:
-
Increased Efficiency: Robots work tirelessly, reducing cycle times and minimizing production bottlenecks.
-
Enhanced Accuracy: Robots perform tasks with unmatched precision, improving product quality and consistency.
-
Improved Safety: Robots can handle hazardous tasks, reducing workplace accidents and injuries for human workers.
-
Reduced Labor Costs: While robots require substantial upfront investment, they can significantly reduce labor costs over time by eliminating overtime and increasing productivity.
-
Increased Flexibility: Robots can be easily reprogrammed for different tasks, enabling manufacturers to adapt to changing market demands and product requirements.
Challenges and Considerations
Despite their numerous advantages, industrial robots also present certain challenges:
-
High Initial Investment: The acquisition and implementation of industrial robots require significant capital investment, which may be prohibitive for some businesses.
-
Skill Shortage: Training and maintaining a skilled workforce with expertise in robotics can be challenging, especially in regions with limited access to specialized training programs.
-
Safety Concerns: While industrial robots are designed with safety features, it is crucial to implement proper safety protocols and training to prevent accidents.
The Future of Industrial Robots
The future of industrial robots holds immense promise, with advancements in technology poised to unlock even greater capabilities. Some key trends include:
-
Collaborative Robots: Cobots, designed to work alongside human workers, will further enhance productivity and safety.
-
AI and Machine Learning: Integration of artificial intelligence and machine learning will empower robots with self-learning and decision-making capabilities.
-
Cloud Connectivity: Cloud-based systems will provide remote monitoring, predictive maintenance, and data analytics capabilities for improved robot performance.
Interesting Stories and Lessons Learned
Humorous Story 1
During a robot installation, a technician accidentally reversed the wiring, causing the robot to spin clockwise instead of counterclockwise. The robot became an instant factory joke, earning the nickname "The Dizzy Robot." The lesson learned: Double-check all connections before starting a robot.

Humorous Story 2
A robot tasked with painting a car went haywire, leaving streaks and splotches all over the vehicle. The resulting "abstract masterpiece" became a laughing stock. The lesson learned: Ensure proper programming and maintenance to avoid costly mistakes.
Humorous Story 3
A robot assigned to assemble a delicate electronic component failed to grasp the part with the required precision, crushing it instead. The team labeled the incident "The Robot's Thumbs of Steel." The lesson learned: Choose the right robot for the task and provide adequate training.
Tips and Tricks
-
Conduct a thorough needs assessment: Determine the specific needs and challenges your business faces before investing in industrial robots.
-
Choose the right robot: Consider the application, payload capacity, and required speed and precision when selecting a robot.
-
Provide proper training: Train operators and maintenance personnel to ensure safe and efficient operation.
-
Implement safety protocols: Establish clear safety guidelines and procedures to protect workers and prevent accidents.
-
Monitor and maintain: Regularly monitor robot performance and conduct preventive maintenance to minimize downtime and extend the robot's lifespan.
Common Mistakes to Avoid
-
Underestimating the investment: Recognize that robotic integration requires substantial upfront costs and ongoing maintenance expenses.
-
Ignoring safety: Failure to implement proper safety measures can lead to accidents and injuries.
-
Lack of training: Inadequate training can result in improper operation and reduced productivity.
-
Overreliance on automation: While robots can automate many tasks, they should complement human workers rather than replace them entirely.
-
Neglecting maintenance: Ignoring routine maintenance can lead to breakdowns and reduced robot performance.
How to Step-by-Step Approach
Step 1: Assess Needs and Goals
Define the specific tasks and challenges that industrial robots could address within your business.
Step 2: Research and Select
Conduct thorough research on different types of robots, manufacturers, and vendors to find the best fit for your needs.
Step 3: Plan and Implement
Develop an implementation plan that includes site preparation, robot installation, and operator training.
Step 4: Monitor and Evaluate
Regularly monitor robot performance and collect data to optimize operations and identify areas for improvement.
Potential Drawbacks
-
Job Displacement: While robots can increase productivity, they can also lead to job displacement for certain types of manual labor.
-
Technology Obsolescence: Rapid advancements in robotics may require frequent upgrades, resulting in additional costs.
-
System Complexity: Implementing industrial robots can introduce complexity into manufacturing processes, requiring specialized knowledge and support.
Pros and Cons
Pros |
Cons |
Increased efficiency and productivity |
High initial investment |
Enhanced accuracy and precision |
Skilled workforce requirement |
Improved safety for human workers |
Safety concerns if not implemented properly |
Reduced labor costs |
Job displacement |
Increased flexibility and adaptability |
Technology obsolescence |
Integration with other automated systems |
System complexity |
Cost Considerations
Type of Robot |
Average Cost |
Articulated Robot |
$50,000 - $250,000 |
Cartesian Robot |
$20,000 - $100,000 |
Cylindrical Robot |
$30,000 - $150,000 |
SCARA Robot |
$25,000 - $125,000 |
Mobile Robot |
$15,000 - $75,000 |
Market Size and Projections
Global Industrial Robot Market
Year |
Market Size (USD Billion) |
Growth Rate |
2021 |
50.3 |
12.0% |
2026 |
85.8 |
8.0% |
2031 |
125.5 |
5.0% |
Key Industry Players
- ABB
- Fanuc
- KUKA
- Yaskawa
- Mitsubishi Electric
Further Reading