Welding Robots: The Future of Industrial Manufacturing
Introduction
Industrial welding robots are revolutionizing the manufacturing industry, transforming production processes and enhancing productivity. These automated systems offer unprecedented accuracy, efficiency, and safety, making them essential for businesses seeking to optimize their operations and stay competitive in a demanding global market.
Evolution of Industrial Welding Robots: A Historical Perspective
The advent of industrial welding robots can be traced back to the 1960s, with the introduction of early models by Unimation and Cincinnati Milacron. These early robots were relatively simple, designed primarily for spot welding applications. However, rapid technological advancements over the years have led to the development of highly sophisticated robots capable of performing a wide range of complex welding tasks.
Types of Industrial Welding Robots
Industrial welding robots come in various types, each suited for specific applications. Some of the most common types include:
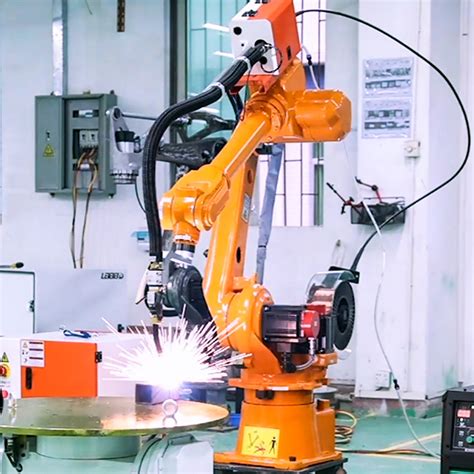
-
Cartesian Robots: These robots move along three linear axes, providing precise movements for applications such as spot welding and arc welding.
-
Articulated Robots: With multiple rotational joints, articulated robots offer a high degree of flexibility and are commonly used in complex welding operations requiring access to hard-to-reach areas.
-
SCARA Robots: Designed for assembly and pick-and-place tasks, SCARA robots (Selective Compliance Assembly Robot Arm) excel in high-speed and precise operations.
Benefits of Using Industrial Welding Robots
The adoption of industrial welding robots offers numerous benefits for manufacturing businesses:
-
Increased Productivity: Robots can operate continuously, reducing downtime and minimizing production delays.
-
Enhanced Quality: Automated welding processes ensure consistent and precise welds, reducing defects and improving product quality.
-
Labor Cost Savings: Robots eliminate the need for manual welding, freeing up workers to focus on other tasks and reducing labor costs.
-
Improved Safety: Robots can handle hazardous welding operations, minimizing worker exposure to risks and improving workplace safety.
-
Flexibility: Many industrial welding robots can be programmed to perform multiple welding tasks, increasing flexibility and adaptability in production processes.
Applications of Industrial Welding Robots
Industrial welding robots find widespread applications in various industries, including:

-
Automotive: Welding of vehicle frames, body panels, and chassis.
-
Construction: Fabrication of steel structures, bridges, and buildings.
-
Aerospace: Welding of aircraft components, spacecraft, and satellites.
-
Consumer Products: Manufacturing of appliances, electronics, and machinery.
-
Medical Devices: Welding of surgical instruments, prosthetics, and medical equipment.
Effective Strategies for Implementing Industrial Welding Robots
To maximize the benefits of industrial welding robots, effective implementation strategies are crucial:
-
Proper Planning: Conduct thorough research, define welding requirements, and determine robot capabilities before purchasing.
-
Skilled Labor: Train staff to operate, maintain, and program the robots effectively.
-
Safety Considerations: Implement rigorous safety protocols to minimize risks and ensure compliance with industry standards.
-
Optimization: Continuously monitor and adjust robot parameters to optimize welding processes and reduce downtime.
-
Maintenance and Troubleshooting: Establish a proactive maintenance plan and train staff to troubleshoot and resolve issues promptly.
Tips and Tricks for Efficient Welding Robot Operations
-
Pre-Welding Preparation: Ensure proper workpiece preparation, including cleaning, degreasing, and alignment, to optimize welding results.
-
Nozzle Selection: Choose the appropriate welding nozzle size and shape for the specific welding application and joint geometry.
-
Wire Feed Speed: Adjust the wire feed speed to match the welding parameters and maintain a consistent arc length.
-
Travel Speed: Optimize the robot's travel speed to achieve the desired weld quality and penetration.
-
Parameter Monitoring: Monitor key welding parameters, such as voltage, current, and travel speed, to ensure process stability.
Common Mistakes to Avoid When Using Welding Robots
-
Lack of Proper Training: Inadequate training of operators can lead to errors and potential safety hazards.
-
Incorrect Programming: Programming errors can result in inaccurate welding, reduced productivity, and machine damage.
-
Neglecting Maintenance: Failure to maintain the robot regularly can lead to breakdowns, decreased performance, and increased downtime.
-
Ignoring Safety Protocols: Compromising on safety measures can put workers at risk and lead to workplace accidents.
-
Overloading the Robot: Attempting to weld beyond the robot's capacity can strain the system and cause damage.
How Industrial Welding Robots Matter: The Future of Manufacturing
Industrial welding robots play a pivotal role in the future of manufacturing. Here's why:

-
Enhanced Competitiveness: By automating welding processes, businesses can improve productivity, reduce costs, and stay competitive in a global market.
-
Increased Efficiency and Accuracy: Robots ensure consistent and precise welding, reducing defects and minimizing material waste.
-
Labor Force Optimization: Robots free up skilled workers for other tasks, allowing them to focus on higher-value activities.
-
Improved Safety and Ergonomics: Robots eliminate human exposure to hazardous welding operations, improving workplace safety and ergonomics.
-
Sustainability: Robots can optimize welding processes, reducing energy consumption and waste generation, promoting sustainable manufacturing practices.
Benefits of Industrial Welding Robots: A Numerical Perspective
- According to the International Federation of Robotics (IFR), the global industrial robot stock is projected to reach 5.6 million units by 2025.
- A study by McKinsey & Company found that automation of welding processes can reduce labor costs by up to 50%.
- A report by the American Welding Society (AWS) estimates that the use of welding robots can increase productivity by 30-50%.
- Research by the University of California, Berkeley, shows that robots can achieve welding accuracy within a tolerance of ±0.005 inches.
- A survey by the Robotic Industries Association (RIA) indicates that 80% of manufacturers using welding robots have experienced significant improvements in product quality.
Humorous Stories and Lessons Learned
Story 1:
A welding robot malfunctioned during a production run, causing a series of defective welds. The maintenance team spent hours troubleshooting, only to discover that the robot had simply run out of welding wire. Lesson: Even robots need regular supplies.
Story 2:
One day, a programmer accidentally reversed the polarity of the welding electrodes, resulting in a comical display of sparks and laughter throughout the factory. Lesson: Double-check your programming before starting any welding operation.
Story 3:

A welding robot was programmed to weld a complex part, but a minor programming error caused it to weld the part upside down. The manager had a good laugh, and the team learned the importance of thorough testing. Lesson: Test your programs before putting them into production.
Step-by-Step Approach to Implementing Industrial Welding Robots
-
Planning: Research, define requirements, and determine robot capabilities.
-
Selection: Choose the appropriate robot type and model for your application.
-
Installation: Install the robot and associated equipment according to safety standards.
-
Training: Train staff to operate, maintain, and program the robot effectively.
-
Programming: Program the robot with specific welding parameters and instructions.
-
Testing: Test the robot's performance and make necessary adjustments.
-
Production: Implement the robot into the production process and monitor its performance.
-
Maintenance: Establish a regular maintenance schedule to prevent breakdowns and ensure optimal operation.
Interesting Tables
Table 1: Types of Industrial Welding Robots
Type |
Description |
Cartesian |
Moves along three linear axes, providing precise movements for spot welding and arc welding |
Articulated |
Features multiple rotational joints, offering flexibility and access to hard-to-reach areas |
SCARA |
Designed for high-speed and precise assembly and pick-and-place tasks |
Table 2: Applications of Industrial Welding Robots
Industry |
Applications |
Automotive |
Welding of vehicle frames, body panels, and chassis |
Construction |
Fabrication of steel structures, bridges, and buildings |
Aerospace |
Welding of aircraft components, spacecraft, and satellites |
Consumer Products |
Manufacturing of appliances, electronics, and machinery |
Medical Devices |
Welding of surgical instruments, prosthetics, and medical equipment |
Table 3: Benefits of Industrial Welding Robots
Benefit |
Description |
Increased Productivity |
Robots operate continuously, reducing downtime and minimizing production delays |
Enhanced Quality |
Automated welding processes ensure consistent and precise welds, reducing defects and improving product quality |
Labor Cost Savings |
Robots eliminate the need for manual welding, freeing up workers for other tasks and reducing labor costs |
Improved Safety |
Robots can handle hazardous welding operations, minimizing worker exposure to risks and improving workplace safety |
Flexibility |
Many industrial welding robots can be programmed to perform multiple welding tasks, increasing flexibility and adaptability in production processes |
Frequently Asked Questions (FAQs)
1. Are industrial welding robots expensive to purchase and maintain?
While initial costs can be significant, the long-term savings in labor costs, increased productivity, and improved quality often outweigh the investment. Maintenance costs can be minimized with proper care and adherence to recommended maintenance schedules.
2. How do I choose the right industrial welding robot for my application?
Consider the specific welding requirements, workpiece size and complexity, and production volume. Consult with vendors and industry experts to determine the robot type and capabilities that best suit your needs.
3. What are the safety considerations when using industrial welding robots?
Implement rigorous safety protocols, including proper guarding, training, and regular maintenance. Adhere to industry standards and guidelines