The Robot Revolution: Unlocking the Potential of Industrial Automation
Introduction
Industrial robots are the cornerstone of modern manufacturing, playing a vital role in automating repetitive and hazardous tasks, improving productivity, and reducing costs. These machines have evolved significantly over the years, from their humble beginnings in the automotive industry to their ubiquitous presence across a wide range of applications.
History and Evolution
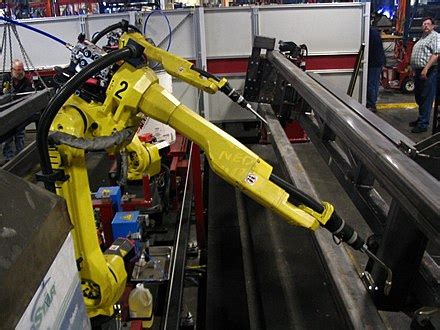
The concept of industrial robots emerged in the 1950s, with the first programmable robot developed by George Devol in 1954. Early industrial robots were large, expensive, and limited in their capabilities. However, advancements in technology, particularly in the fields of electronics and computer science, have led to significant advancements in the design and functionality of industrial robots.
Classification

Industrial robots can be classified into several types based on their design and functionality:
-
Articulated robots: These robots have a jointed arm that can move in multiple directions, providing a high degree of flexibility and reach.
-
Cartesian robots: These robots move along three axes (X, Y, and Z), offering precise positioning and repeatability.
-
Delta robots: These robots have a triangular base and three arms that move independently, providing high speed and acceleration.
-
Collaborative robots (cobots): These robots are designed to work alongside human workers, providing assistance and enhancing productivity without the need for safety cages.
Applications
Industrial robots are used in a vast array of applications, including:
-
Manufacturing: Assembly, welding, painting, packaging, and material handling.
-
Automotive: Body panel assembly, welding, painting, and inspection.
-
Electronics: Circuit board assembly, soldering, and testing.
-
Food and beverage: Food processing, packaging, and inspection.
-
Healthcare: Surgery, drug delivery, and rehabilitation.
Benefits of Industrial Robots
The adoption of industrial robots offers numerous benefits, including:
-
Increased productivity: Robots can operate 24/7, performing tasks with greater speed and precision than humans.
-
Lower labor costs: While robots have a higher upfront cost, they can significantly reduce labor expenses in the long run.
-
Improved quality: Robots can maintain consistent accuracy and repeatability, reducing errors and increasing product quality.
-
Enhanced safety: Robots can handle hazardous tasks that are dangerous for human workers.
-
Flexibility: Modern robots can be easily programmed to perform a variety of tasks, offering manufacturers the ability to adapt quickly to changing market demands.
Potential Drawbacks
While industrial robots offer significant benefits, there are also some potential drawbacks to consider:
-
High capital investment: The cost of acquiring and implementing industrial robots can be substantial.
-
Job displacement: The adoption of robots can lead to job losses in certain industries, particularly for tasks that are easily automated.
-
Skills gap: Operating and maintaining industrial robots requires specialized skills, which may not be readily available in the workforce.
-
Safety concerns: Industrial robots must be properly installed, maintained, and operated to avoid accidents and injuries.
The Future of Industrial Robots

The future of industrial robots is bright. Advances in artificial intelligence (AI), machine learning, and other technologies are expected to further enhance the capabilities and functionality of these machines. Collaborative robots are becoming increasingly popular, enabling humans and robots to work together in a safe and productive environment. The adoption of industrial robots is expected to continue to grow, as manufacturers seek ways to improve efficiency, reduce costs, and address the challenges of a changing global economy.
Effective Strategies for Implementing Industrial Robots
To effectively implement industrial robots, manufacturers should consider the following strategies:
-
Identify suitable applications: Determine which tasks can be automated with industrial robots to maximize return on investment.
-
Plan and prepare: Conduct a thorough assessment of the manufacturing process and infrastructure to ensure that robots can be successfully integrated.
-
Train personnel: Invest in training programs to develop the skills required to operate and maintain industrial robots.
-
Implement safety measures: Develop and implement comprehensive safety protocols to minimize the risk of accidents and injuries.
-
Monitor and evaluate: Regularly monitor the performance of industrial robots and make adjustments as needed to improve efficiency and productivity.
How to Step-by-Step Approach to Industrial Robot Implementation
-
Define the task: Identify the specific task or process that needs to be automated.
-
Select the right robot: Choose the type of robot that is best suited for the task, considering factors such as payload, reach, and accuracy.
-
Design the workspace: Create a safe and efficient workspace for the robot, including safety cages, guards, and lighting.
-
Program the robot: Develop a program that defines the robot's movements and actions.
-
Install and integrate the robot: Install the robot in the workspace and integrate it with other equipment as needed.
-
Test and evaluate the robot: Conduct thorough testing and evaluation to ensure that the robot is operating properly and safely.
-
Train operators: Train operators on how to safely operate and maintain the robot.
Why Industrial Robot Implementation Matters
Industrial robot implementation matters for several reasons:
-
Increased productivity: Robots can significantly increase productivity, freeing up human workers to focus on more complex tasks.
-
Lower labor costs: Robots can reduce labor costs, leading to lower production costs and increased profitability.
-
Improved quality: Robots can improve product quality by eliminating errors and maintaining consistent accuracy.
-
Enhanced safety: Robots can handle hazardous tasks, reducing the risk of accidents and injuries for human workers.
-
Flexibility: Robots can be easily reprogrammed to perform different tasks, providing manufacturers with the ability to adapt quickly to changing market demands.
Potential Drawbacks of Industrial Robot Implementation
While industrial robot implementation offers significant benefits, there are also some potential drawbacks to consider:
-
High capital investment: Robots can be expensive to purchase and implement, particularly for small businesses.
-
Job displacement: Robots can displace human workers, potentially leading to job losses.
-
Skills gap: Operating and maintaining robots requires specialized skills, which may not be readily available in the workforce.
-
Safety concerns: Robots must be properly installed, maintained, and operated to avoid accidents and injuries.
Frequently Asked Questions about Industrial Robots
-
What is the difference between a robot and a cobot? A robot is a fully autonomous machine that can perform tasks without human intervention, while a cobot is a robot that is designed to work alongside human workers.
-
Are robots safe? Robots are inherently safe, but they must be properly installed, maintained, and operated to avoid accidents and injuries.
-
How much does a robot cost? The cost of a robot can vary significantly depending on the type of robot, its capabilities, and the manufacturer. However, most industrial robots cost between $100,000 and $500,000.
-
How long does it take to implement a robot? The time it takes to implement a robot can vary depending on the complexity of the task and the size of the operation. However, most robots can be implemented within a few months.
-
What are the benefits of using industrial robots? The benefits of using industrial robots include increased productivity, lower labor costs, improved quality, enhanced safety, and flexibility.
-
What are the challenges of using industrial robots? The challenges of using industrial robots include the high capital investment, the potential for job displacement, the skills gap, and safety concerns.
Call to Action
Industrial robots have the potential to revolutionize manufacturing and other industries. By implementing robots effectively, manufacturers can improve productivity, reduce costs, and address the challenges of a changing global economy. If you are considering implementing industrial robots, it is important to carefully consider the strategies and approaches outlined in this article to ensure a successful implementation.
Table 1: Industrial Robot Market Statistics
Year |
Number of Industrial Robots Sold |
2017 |
381,000 |
2018 |
422,000 |
2019 |
420,000 |
2020 |
373,000 |
2021 |
484,000 |
Source: International Federation of Robotics
Table 2: Benefits of Industrial Robots
Benefit |
Description |
Increased productivity |
Robots can work 24/7, perform tasks more quickly and accurately than humans, and eliminate downtime. |
Lower labor costs |
Robots can reduce labor costs by automating repetitive and hazardous tasks, freeing up human workers to focus on more complex and value-added activities. |
Improved quality |
Robots can maintain consistent accuracy and repeatability, reducing errors and improving product quality. |
Enhanced safety |
Robots can handle hazardous tasks that are dangerous for human workers, reducing the risk of accidents and injuries. |
Flexibility |
Robots can be easily reprogrammed to perform different tasks, providing manufacturers with the ability to adapt quickly to changing market demands. |
Source: International Federation of Robotics
Table 3: Potential Drawbacks of Industrial Robots
Drawback |
Description |
High capital investment |
Robots can be expensive to purchase and implement, particularly for small businesses. |
Job displacement |
Robots can displace human workers, potentially leading to job losses. |
Skills gap |
Operating and maintaining robots requires specialized skills, which may not be readily available in the workforce. |
Safety concerns |
Robots must be properly installed, maintained, and operated to avoid |