Industrial Robots: The Automated Workforce Revolutionizing Industries
Industrial robots, the epitome of automation and efficiency, are transforming industries at an unprecedented pace. They have become invaluable assets in manufacturing, healthcare, logistics, and myriad other sectors. This article delves into the fascinating world of industrial robots, exploring their capabilities, benefits, and potential impact on the future of work.
Capabilities of Industrial Robots
Industrial robots are versatile machines designed for a wide range of tasks and applications. Their capabilities include:
-
Precision and Accuracy: They possess high precision and accuracy, enabling them to perform intricate tasks with minimal errors.
-
Repetitive Tasks: They excel at repetitive tasks, freeing up human workers for more complex and creative endeavors.
-
Heavy Lifting: They can handle heavy loads, reducing the risk of injuries and strain for human workers.
-
Hazardous Environments: They can operate in hazardous environments, such as those with toxic chemicals or extreme temperatures, ensuring worker safety.
-
24/7 Operation: They can operate continuously, eliminating downtime and increasing productivity.
Benefits of Industrial Robots
The benefits of implementing industrial robots are numerous and far-reaching, including:
-
Increased Productivity: They enhance productivity by performing tasks faster and more efficiently than humans.
-
Reduced Costs: They reduce labor costs, overtime expenses, and the risk of downtime.
-
Improved Safety: They eliminate the need for humans to engage in hazardous tasks, reducing workplace accidents.
-
Enhanced Quality: They ensure consistent quality in production processes, minimizing defects and waste.
-
Increased Competitiveness: They provide companies with a competitive edge by enabling them to produce goods and services at lower costs and higher quality.
Impact on the Future of Work
The rise of industrial robots has sparked discussions about their potential impact on the future of work. While it is true that robots could replace certain jobs in highly repetitive or hazardous industries, they also create new opportunities in areas such as:

-
Robot Programming and Maintenance: The demand for skilled professionals to program, maintain, and repair industrial robots is expected to grow significantly.
-
Data Analysis and Process Optimization: Robots generate vast amounts of data that can be analyzed to optimize processes and identify areas for improvement.
-
Human-Robot Collaboration: Robots can work alongside humans, complementing their skills and enhancing overall efficiency.
Effective Strategies for Implementing Industrial Robots
To successfully implement and harness the benefits of industrial robots, businesses should consider the following effective strategies:

-
Identify Clear Objectives: Define the specific goals and tasks for which robots will be used.
-
Conduct a Feasibility Study: Assess the technical, financial, and operational viability of implementing robots.
-
Choose the Right Robots: Select robots that align with the specific requirements of the application.
-
Integrate Robots into Existing Processes: Plan for a seamless integration of robots into existing workflows.
-
Train Employees: Provide comprehensive training to employees on robot programming, operation, and maintenance.
Common Mistakes to Avoid
To avoid common pitfalls in industrial robot implementation, it is essential to:
-
Avoid Over-Automation: Implement robots only in areas where they provide a clear return on investment.
-
Neglect Safety: Prioritize safety by conducting thorough risk assessments and implementing appropriate safety measures.
-
Underestimate Training: Ensure adequate training is provided to all personnel involved in robot operation and maintenance.
-
Ignore Maintenance: Establish a comprehensive maintenance schedule to prevent breakdowns and ensure optimal performance.
-
Fail to Monitor Performance: Regularly monitor robot performance and make adjustments as needed to optimize results.
How to Implement Industrial Robots Step-by-Step
Follow these steps for a successful industrial robot implementation:
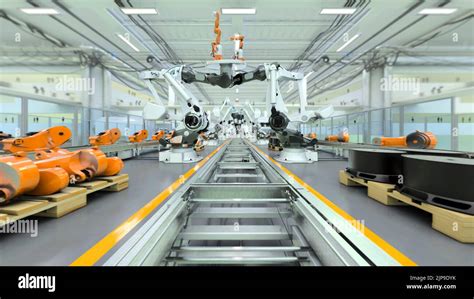
-
Assessment: Conduct a thorough assessment of the application and define the scope of the project.
-
Feasibility: Determine the feasibility of the project based on technical, financial, and operational factors.
-
Selection: Select the appropriate robots and peripherals for the application.
-
Integration: Integrate the robots into existing processes and infrastructure.
-
Training: Train employees on robot programming, operation, and maintenance.
-
Implementation: Deploy the robots and monitor their performance.
-
Evaluation: Regularly evaluate robot performance and make necessary adjustments.
Advanced Features of Industrial Robots
Modern industrial robots offer a range of advanced features, including:

-
Artificial Intelligence (AI): Robots can leverage AI to learn from data, improve decision-making, and adapt to changing conditions.
-
Computer Vision: Robots equipped with computer vision can process and interpret visual information, enabling them to perform tasks such as object recognition and inspection.
-
Force Control: Robots with force control capabilities can adjust their force output based on the task requirements, ensuring delicate handling of fragile objects.
-
Collaborative Robotics: Collaborative robots are designed to work alongside humans, enhancing safety and facilitating human-robot interaction.
Potential Drawbacks of Industrial Robots
While industrial robots offer significant benefits, there are also potential drawbacks to consider:
-
High Initial Investment: The upfront cost of purchasing and implementing industrial robots can be substantial.
-
Skill Shortage: Finding skilled personnel to program, maintain, and repair robots can be challenging.
-
Job Displacement: In certain industries, the implementation of robots may lead to job displacement for human workers.
-
Technical Complexity: Integrating and maintaining industrial robots requires specialized technical expertise.
-
Safety Considerations: Industrial robots must be operated and maintained with proper safety measures in place to prevent accidents and injuries.
FAQs About Industrial Robots
Below are some frequently asked questions about industrial robots:
- 1. What is the average lifespan of an industrial robot?
-
The average lifespan of an industrial robot is around 10-15 years, depending on the application and maintenance practices.
-
2. How much does an industrial robot cost?
-
The cost of an industrial robot varies depending on the size, capabilities, and manufacturer. It can range from tens of thousands to hundreds of thousands of dollars.
-
3. Are industrial robots safe to use around humans?
- Industrial robots are safe to use around humans when proper safety measures are in place. This includes risk assessments, protective barriers, and training for personnel.
Humorous Stories and Lessons Learned
Conclusion
Industrial robots are revolutionizing industries across the globe, offering unparalleled automation and efficiency. By embracing the capabilities of robots, businesses can enhance productivity, reduce costs, improve safety, and gain a competitive edge. However, it is crucial to implement robots strategically and address potential drawbacks, such as the need for skilled personnel and the risk of job displacement. As technology continues to advance, we can expect even more innovative and groundbreaking applications of industrial robots in the years to come.