Industrial Welding Robots: The Future of Welding Applications
Industrial welding robots are revolutionizing the welding industry. They have several distinct advantages over manual welding, including increased efficiency, precision, and repeatability.
Benefits of Industrial Welding Robots
The benefits of industrial welding robots are numerous:
-
Increased efficiency: Industrial welding robots can weld much faster than human welders. This can lead to significant cost savings for businesses.
-
Improved precision: Industrial welding robots are very precise, which can help to ensure that welds are of high quality.
-
Increased repeatability: Industrial welding robots can repeat the same weld over and over again with great accuracy. This can help to reduce the chances of defects.
-
Improved safety: Industrial welding robots can help to eliminate the risks associated with manual welding, such as exposure to fumes and radiation.
-
Increased productivity: Industrial welding robots can operate 24/7, which can help to increase productivity.
Applications of Industrial Welding Robots
Industrial welding robots are used in a wide variety of applications, including:
-
Automotive manufacturing: Industrial welding robots are used to weld car bodies, frames, and other components.
-
Construction: Industrial welding robots are used to weld bridges, buildings, and other structures.
-
Aerospace: Industrial welding robots are used to weld aircraft components, such as wings and fuselages.
-
Medical: Industrial welding robots are used to weld medical devices, such as implants and surgical instruments.
Types of Industrial Welding Robots
There are two main types of industrial welding robots:
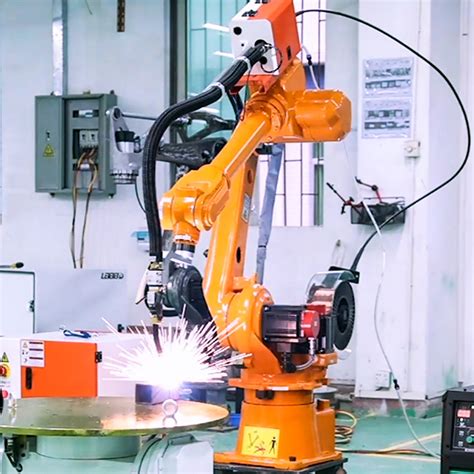
-
Cartesian robots: Cartesian robots move in a straight line along three axes. They are typically used for simple welding applications, such as spot welding.
-
Robotic arms: Robotic arms have a more complex design and can move in all directions. They are typically used for more complex welding applications, such as arc welding.
Components of an Industrial Welding Robot
The main components of an industrial welding robot include:
-
Controller: The controller is the brain of the robot. It controls the robot's movements and welding parameters.
-
Power supply: The power supply provides the robot with the electricity it needs to operate.
-
Welding torch: The welding torch is the tool that melts the metal and creates the weld.
-
Wire feeder: The wire feeder supplies the welding torch with the filler metal.
How to Choose an Industrial Welding Robot
When choosing an industrial welding robot, it is important to consider the following factors:

-
Type of welding: The type of welding that will be performed will determine the type of robot that is needed.
-
Materials to be welded: The materials that will be welded will also determine the type of robot that is needed.
-
Complexity of the weld: The complexity of the weld will determine the type of robot that is needed.
-
Budget: The budget will determine the type of robot that can be purchased.
Tips for Using Industrial Welding Robots
Here are some tips for using industrial welding robots:
-
Use the right welding parameters: The welding parameters must be set correctly in order to ensure that the weld is of high quality.
-
Maintain the robot regularly: The robot must be maintained regularly in order to ensure that it is operating properly.
-
Train operators properly: Operators must be trained properly in order to operate the robot safely and efficiently.
Common Mistakes to Avoid
Here are some common mistakes to avoid when using industrial welding robots:

-
Using the wrong welding parameters: Using the wrong welding parameters can lead to poor quality welds.
-
Not maintaining the robot regularly: Not maintaining the robot regularly can lead to breakdowns and downtime.
-
Not training operators properly: Not training operators properly can lead to accidents and injuries.
Advanced Features
Some industrial welding robots have advanced features, such as:
-
Vision systems: Vision systems can help the robot to align itself with the workpiece and to identify defects in the weld.
-
Laser scanners: Laser scanners can help the robot to create a 3D model of the workpiece so that it can weld it accurately.
-
Artificial intelligence: Artificial intelligence can help the robot to learn and adapt to different welding conditions.
Potential Drawbacks
Industrial welding robots have some potential drawbacks, such as:
-
Cost: Industrial welding robots can be expensive to purchase and maintain.
-
Complexity: Industrial welding robots can be complex to operate and maintain.
-
Safety: Industrial welding robots can be dangerous if they are not operated properly.
Pros and Cons
The pros and cons of industrial welding robots are as follows:

Pros:
- Increased efficiency
- Improved precision
- Enhanced safety
Cons:
- High cost
- Can be complex
- Safety concerns
FAQs
Here are some frequently asked questions about industrial welding robots:
-
How much do industrial welding robots cost? The cost of an industrial welding robot varies depending on the brand, model, and features.
-
What are the benefits of using industrial welding robots? The benefits of using industrial welding robots include increased efficiency, improved precision, and fewer defects.
-
What are the drawbacks of using industrial welding robots? The drawbacks of using industrial welding robots include the high cost, complexity, and safety concerns.
Additional Resources