Unlocking the Potential of Industrial Automation: A Comprehensive Guide to KUKA Industrial Robots
Introduction to KUKA Industrial Robots
KUKA Industrial Robots: Reshaping the Future of Manufacturing
KUKA Industrial Robots are at the forefront of industrial automation, empowering businesses to achieve unprecedented levels of efficiency, precision, and productivity. As a leading provider of robotic solutions, KUKA offers a comprehensive portfolio of robots tailored to diverse applications across various industries, from automotive to aerospace and logistics.
10 Transformative Applications of KUKA Industrial Robots
-
Automotive Assembly: Robots perform intricate tasks such as welding, painting, and assembly, enhancing quality and reducing production time.
-
Aerospace Manufacturing: Robots handle delicate components and perform precision operations, ensuring compliance with stringent industry standards.
-
Electronics Production: Robots automate repetitive tasks, such as component placement and soldering, with high accuracy and speed.
-
Food and Beverage Processing: Robots maintain hygiene standards, improve efficiency, and increase productivity in food processing operations.
-
Healthcare: Robots assist in surgeries, rehabilitation, and dispensing medications, enhancing accuracy and patient outcomes.
-
Logistics and Warehousing: Robots automate material handling, order fulfillment, and inventory management, optimizing logistics operations.
-
Metal Fabrication: Robots perform welding, cutting, and bending operations with precision and consistency, reducing production time and material waste.
-
Pharmaceutical Manufacturing: Robots handle sterile environments, package drugs with precision, and increase production efficiency.
-
Plastics Manufacturing: Robots automate injection molding, trimming, and assembly processes, ensuring high-quality products and reducing defects.
-
Woodworking: Robots perform intricate cuts, shaping, and assembly tasks, enhancing efficiency and product quality in woodworking operations.
3 Inspiring Stories of KUKA Robots in Action
Story 1: The Robot Painter

Company X sought to automate its painting process to achieve higher quality and reduce costs. They deployed a KUKA robot equipped with a state-of-the-art spray gun. The robot's precision and consistency eliminated human error, resulting in flawless paint finishes and a 25% reduction in production time.
Lesson Learned: Investing in automation can dramatically improve product quality and reduce manufacturing costs.

Story 2: The Unmanned Forklift
Company Y faced challenges in meeting increasing order fulfillment demands. They implemented a fleet of KUKA autonomous mobile robots (AMRs) to automate material handling. The robots seamlessly navigated the warehouse, transporting goods efficiently and reducing labor costs by 30%.
Lesson Learned: AMRs can dramatically increase productivity and cost-effectiveness in logistics operations.

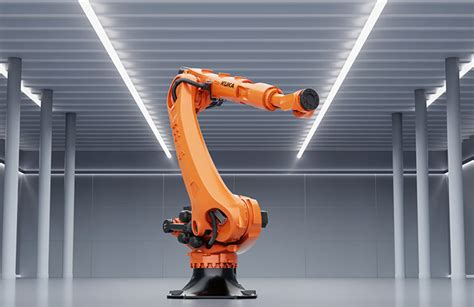
Story 3: The Surgical Precision
Company Z sought to enhance surgical accuracy and reduce patient downtime. They integrated a KUKA robotic system into their surgical suite. The robot assisted in complex procedures, providing surgeons with unparalleled precision and control, reducing surgery time by 15% and improving patient outcomes.
Lesson Learned: Robotic assistance in healthcare can significantly improve patient care and reduce recovery time.
Effective Strategies for Deploying KUKA Industrial Robots
-
Identify Suitable Applications: Carefully assess which processes in your workflow can benefit from automation. Focus on repetitive, high-volume, or hazardous tasks.
-
Choose the Right Robot: Select the appropriate robot model based on your specific application requirements, such as payload capacity, reach, and accuracy.
-
Plan the Integration: Develop a comprehensive plan for integrating the robots into your existing infrastructure, considering factors such as space, power, and communication.
-
Train Your Team: Provide thorough training to operators and maintenance staff to ensure safe and efficient operation of the robots.
-
Monitor and Maintain: Establish a regular maintenance schedule and monitor the performance of the robots to optimize uptime and prevent downtime.
6 Common Mistakes to Avoid When Deploying KUKA Industrial Robots
-
Lack of Proper Planning: Failing to plan the integration of the robots can lead to inefficiencies, delays, and increased costs.
-
Choosing the Wrong Robot: Selecting a robot not suited for the intended application can result in poor performance, reduced productivity, and increased maintenance costs.
-
Inadequate Training: Untrained or improperly trained staff can compromise the safety and effectiveness of the robotic system.
-
Neglecting Maintenance: Lack of regular maintenance can lead to breakdowns, reduced lifespan, and increased downtime.
-
Overestimating Capabilities: Understanding the limitations of the robots is crucial to avoid overloading or using them in applications beyond their capabilities.
-
Ignoring Safety Precautions: Failure to follow safety protocols can result in accidents and injuries.
Advanced Features of KUKA Industrial Robots
-
Vision Guided Robotics: Robots equipped with cameras and advanced software can perform tasks based on visual feedback, enabling precise object recognition and manipulation.
-
Collaborative Robotics: Cobots can safely work alongside human operators, performing tasks that require human-robot interaction.
-
Artificial Intelligence (AI): AI-powered robots can analyze data, adapt to changes, and make autonomous decisions, enhancing productivity and efficiency.
-
Cloud Connectivity: Robots can be connected to cloud-based platforms, enabling remote monitoring, data analytics, and predictive maintenance.
-
Industry 4.0 Integration: KUKA robots can seamlessly integrate into Industry 4.0 environments, facilitating data exchange and automation.
Potential Drawbacks of KUKA Industrial Robots
-
High Investment Costs: The initial investment in purchasing and installing industrial robots can be significant.
-
Ongoing Maintenance Costs: Regular maintenance, repairs, and software updates are required to ensure optimal performance and prevent downtime.
-
Job Displacement: Automation can potentially lead to the displacement of jobs for tasks that are easily automated.
-
Safety Concerns: Improper installation or operation of the robots can pose safety risks to workers and equipment.
-
Training Requirements: Deploying industrial robots requires specialized training for operators and maintenance personnel.
Pros and Cons of KUKA Industrial Robots
Pros:
- Improved efficiency and productivity
- Enhanced accuracy and precision
- Reduced labor costs
- Increased safety
- Consistency in performance
Cons:
- High investment costs
- Potential for job displacement
- Ongoing maintenance expenses
- Training requirements
- Safety risks
FAQs About KUKA Industrial Robots
1. What industries use KUKA industrial robots?
KUKA robots are deployed in a wide range of industries, including automotive, aerospace, electronics, healthcare, logistics, pharmaceuticals, plastics, and woodworking.
2. How much do KUKA industrial robots cost?
The cost of KUKA robots varies depending on the model, size, and configuration. The average price range is between $100,000 and $500,000.
3. What is the average lifespan of a KUKA industrial robot?
With proper maintenance, KUKA industrial robots have an average lifespan of 10 to 15 years.
10 Essential Tips for Successful KUKA Robot Deployment
-
Consult with Experts: Engage with KUKA or authorized distributors for guidance and support in selecting and deploying the right robot.
-
Conduct a Thorough Feasibility Study: Assess the potential benefits, costs, and risks of deploying robots in your operations.
-
Invest in Operator Training: Provide comprehensive training to ensure operators can safely and effectively operate the robots.
-
Establish a Maintenance Plan: Develop a regular maintenance schedule to keep the robots in optimal condition.
-
Embrace Advanced Features: Explore the potential of vision guidance, AI, and cloud connectivity to maximize the capabilities of the robots.
-
Consider Safety Precautions: Implement robust safety protocols and ensure the proper installation and operation of the robots.
-
Leverage Industry 4.0 Opportunities: Integrate the robots into a connected ecosystem to enhance data exchange and automation.
-
Anticipate Potential Drawbacks: Be aware of the potential investment costs, maintenance expenses, and safety risks associated with robot deployment.
-
Monitor Performance Regularly: Track the performance of the robots to identify areas for improvement and optimization.
-
Foster a Culture of Innovation: Encourage innovation and creativity to explore new applications and maximize the value of the robots.
Tables on KUKA Industrial Robots
Table 1: Specifications of Popular KUKA Robot Models
Model |
Payload Capacity |
Reach |
Repeatability |
KR 30 |
30 kg |
900 mm |
+/- 0.04 mm |
KR 60 |
60 kg |
1200 mm |
+/- 0.06 mm |
KR 100 |
100 kg |
1500 mm |
+/- 0.08 mm |
KR 16 |
16 kg |
900 mm |
+/- 0.03 mm |
KR 500 |
500 kg |
2400 mm |
+/- 0.12 mm |
Table 2: Applications of KUKA Industrial Robots by Industry
Industry |
Applications |
Automotive |
Welding, painting, assembly |
Aerospace |
Component handling, precision operations |
Electronics |
Component placement, soldering |
Healthcare |
Surgery assistance, rehabilitation |
Logistics |
Material handling, order fulfillment, inventory management |
Pharmaceuticals |
Sterile handling, drug packaging |
Plastics |
Injection molding, trimming, assembly |
Food and Beverage |
Hygiene maintenance, packaging, processing |
Table 3: Key Features and Benefits of KUKA Industrial Robots
Feature |
Explanation |
Benefits |
Robotics |
Automate tasks to improve efficiency and productivity |
|