The Industrial Robot Controller: The Brains Behind the Brawn
The industrial robot controller is the unsung hero of the manufacturing world, orchestrating every move of the robots that power our modern factories. This sophisticated device serves as the central nervous system of robotic systems, translating high-level commands into precise actions while ensuring safety and efficiency.
What is an Industrial Robot Controller?
The industrial robot controller is a specialized computer system that acts as the interface between humans and robots. It receives commands from the user, interprets them, and sends signals to the robot's motors and other actuators to execute the desired actions.
Functions and Capabilities
The controller performs a wide range of functions, including:

- Motion control: Calculates and sends movement commands to the robot's joints to achieve precise trajectories.
- Trajectory planning: Determines the optimal path the robot must follow to complete a given task.
- Sensor integration: Processes data from various sensors (e.g., cameras, force sensors) to provide situational awareness and enable autonomous navigation.
- Safety monitoring: Ensures the robot operates within predefined safety limits, halting operations if necessary.
- User interface: Provides a graphical interface for operators to program and control the robot.
Importance of the Industrial Robot Controller
The industrial robot controller is essential for the smooth and efficient operation of robotic systems. It:

-
Improves productivity: By enabling robots to perform tasks with precision and speed, controllers increase production efficiency and output.
-
Enhances safety: The controller monitors safety parameters and intervenes if the robot deviates from safe limits.
-
Reduces downtime: Continuous monitoring and diagnostic capabilities help identify potential issues early on, minimizing unplanned downtime.
-
Facilitates customization: Controllers can be tailored to specific applications, allowing for flexibility and adaptability.
Types of Industrial Robot Controllers
Various types of industrial robot controllers exist, each with its strengths and use cases:
-
Teach pendants: Handheld devices that allow operators to program robots by manually guiding them through desired motions.
-
Panel-mounted controllers: Stationary units mounted on the robot or nearby, providing a more advanced interface with a keyboard and display.
-
PC-based controllers: Utilize industrial-grade PCs for high-performance computing and advanced algorithms.
Common Mistakes to Avoid
To ensure optimal performance and safety, it is important to avoid common mistakes when working with industrial robot controllers:
-
Overloading the controller: Assigning too many tasks to the controller can lead to overloads and performance issues.
-
Ignoring safety considerations: Failing to set up proper safety measures can compromise the safety of operators and equipment.
-
Insufficient training: Inadequate training of operators can result in accidents and suboptimal controller utilization.
Advanced Features
Modern industrial robot controllers offer advanced features to enhance functionality and productivity:
-
Artificial intelligence (AI): Incorporates machine learning and other AI techniques for autonomous decision-making and path planning.
-
Cloud connectivity: Allows for remote access, monitoring, and data analysis.
-
Collaborative operation: Enables robots to work safely alongside human operators.
Benefits of an Advanced Robot Controller
Investing in an advanced robot controller can yield significant benefits:
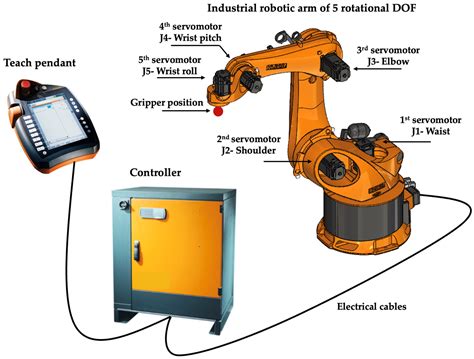
-
Increased efficiency: AI-powered controllers optimize robot movements and reduce cycle times.
-
Improved flexibility: Collaborative operation allows robots to adapt to changing production requirements.
-
Enhanced safety: Advanced safety features mitigate risks and protect operators and equipment.
Tips and Tricks
Here are some tips and tricks for getting the most out of your industrial robot controller:
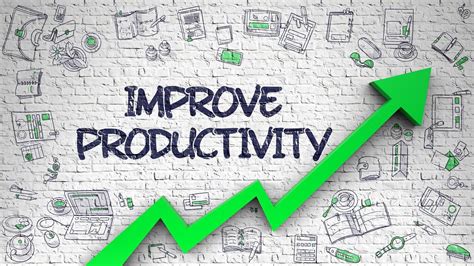
-
Regular maintenance: Ensure proper maintenance and calibration to maintain optimal performance.
-
Optimize code: Write efficient code to minimize controller workload and maximize efficiency.
-
Monitor performance: Track controller performance metrics and make adjustments as needed to improve productivity.
Stories from the Field
-
The Mischievous Robot: A robot accidentally loaded a heavy workpiece into a delicate machine, causing a costly breakdown. The culprit? A malfunction in the controller's load-sensing algorithm.
-
The Determined Engineer: A controller issue led to a robot performing erratic movements. After days of troubleshooting, the engineer discovered a loose connection caused by an overzealous assembly technician.
-
The Robot's Revenge: A controller glitch caused a robot to repeatedly slam a door on the operator's hand. The lesson? Always prioritize safety and ensure rigorous testing before deploying controllers.
Conclusion
The industrial robot controller is a critical component of modern manufacturing, enabling robots to execute tasks with precision, efficiency, and safety. By choosing the right controller for your application and following best practices, you can maximize productivity, minimize downtime, and harness the full potential of robotic automation.
FAQs
1. What is the difference between a robot controller and a PLC?
-
Robot controllers: Specifically designed for robot motion control, offering advanced trajectory planning and safety features.
-
PLCs: General-purpose controllers used in various industrial applications, with limited robotics capabilities.
2. How long does an industrial robot controller typically last?
- With proper maintenance, industrial robot controllers can last for 5-10 years or more.
3. What are the key factors to consider when choosing an industrial robot controller?
-
Application requirements: Determine the specific tasks the robot will perform.
-
Robot type: Consider the robot's size, payload, and kinematics.
-
Safety features: Prioritize safety by ensuring the controller meets industry standards.
Call to Action
If you're looking to optimize the performance of your industrial robots, invest in an advanced robot controller. With its sophisticated features and advanced capabilities, you can unlock new levels of efficiency, flexibility, and safety. Contact our team today to learn more and find the perfect controller for your needs.
Table 1: Comparison of Industrial Robot Controller Types
Type |
Features |
Pros |
Cons |
Teach Pendant |
Handheld interface |
Easy to use |
Limited functionality |
Panel-Mounted Controller |
Stationary unit |
Advanced interface |
Less portable |
PC-Based Controller |
Industrial-grade PC |
High performance |
May require specialized programming |
Table 2: Benefits of an Advanced Robot Controller
Benefit |
Explanation |
Impact |
Increased Efficiency |
AI-powered optimization |
Reduced cycle times |
Improved Flexibility |
Collaborative operation |
Ability to adapt to changing production requirements |
Enhanced Safety |
Advanced safety features |
Mitigated risks and increased operator protection |
Table 3: Common Mistakes to Avoid When Using Industrial Robot Controllers
Mistake |
Consequences |
Overloading the Controller |
performance issues, potential downtime |
Ignoring Safety Considerations |
Compromised safety, accidents |
Insufficient Training |
Accidents, suboptimal controller utilization |