Unraveling the Secrets of Trailer Bearings and Seals: Empowering Your Transportation Journey
Trailer bearings and seals play a pivotal role in ensuring the seamless and safe operation of trailers, enabling the efficient transportation of goods. Understanding their importance and implementing effective maintenance strategies can significantly enhance trailer performance and longevity. Dive into this comprehensive guide to discover valuable information about trailer bearings and seals, empowering you to make informed decisions and optimize your transportation operations.
1. Understanding the Anatomy of Trailer Bearings and Seals
Trailer bearings are crucial components that support the weight of the trailer and facilitate smooth wheel rotation. They comprise:
-
Inner and Outer Races: These hardened steel rings provide a precision surface for the rolling elements to rotate upon.
-
Rolling Elements: Balls or rollers that minimize friction between the races, reducing wear and heat generation.
-
Cage: A framework that keeps the rolling elements evenly spaced and prevents them from rubbing against each other.
Seals, on the other hand, prevent the ingress of contaminants and retain lubricants within the bearing assembly. Common types include:

-
Lip Seals: Contact-type seals that utilize flexible rubber lips to form a barrier against dirt and moisture.
-
Contact Seals: High-performance seals that create a metal-to-metal contact surface, effectively sealing out contaminants.
-
Labyrinth Seals: Non-contact seals that employ multiple barriers to prevent contaminants from reaching the bearing.
2. Choosing the Right Trailer Bearings and Seals
Selecting the appropriate trailer bearings and seals is essential for optimal performance. Consider these factors:
-
Load Capacity: Determine the weight the bearings will support based on the trailer's weight and cargo capacity.
-
Speed Rating: Choose bearings designed for the maximum speed the trailer will typically reach.
-
Environmental Conditions: Consider the operating environment, such as temperature extremes, moisture, and contamination levels.
-
Seal Type: Select seals that provide the necessary protection from contaminants based on the operating conditions.
3. Proper Trailer Bearing Installation and Maintenance
Meticulous installation and regular maintenance are vital for extending the life of trailer bearings and seals. Follow these guidelines:
- Ensure proper bearing fit and preload to prevent excessive wear or preload.
- Use high-quality lubricants designed specifically for trailer bearings.
- Regularly inspect bearings and seals for any signs of wear or damage.
- Repack bearings with fresh lubricant as recommended by the manufacturer or based on operating conditions.
- Monitor seal performance and replace them promptly if any damage or leakage is observed.
4. Common Problems and Solutions for Trailer Bearings and Seals
Various issues can arise with trailer bearings and seals, leading to performance problems. Common issues include:
-
Bearing Failure: Caused by excessive wear, improper installation, or inadequate lubrication.
-
Seal Damage: Can result from contamination, improper assembly, or wear.
-
Corrosion: Moisture and contaminants can lead to corrosion of bearing components.
-
Lubrication Issues: Insufficient or improper lubrication can cause bearing failure and seal damage.
To address these problems, implement measures such as regular inspections, proper maintenance practices, and prompt repairs or replacements.

5. Effective Strategies for Trailer Bearing and Seal Maintenance
Proactive maintenance strategies are key to ensuring optimal trailer performance. Consider these techniques:
-
Regular Inspections: Check bearings and seals during routine maintenance or when any operational issues arise.
-
Preventive Maintenance: Schedule proactive bearing repacks and seal replacements based on manufacturer recommendations or operating conditions.
-
Condition Monitoring: Employ tools such as vibration analysis or temperature monitoring to detect potential problems early on.
-
Training: Provide training to maintenance personnel on proper installation, lubrication, and inspection procedures.
6. Common Mistakes to Avoid
To avoid costly repairs and downtime, steer clear of these common mistakes:
- Overloading trailers beyond their rated weight capacity.
- Operating trailers at excessive speeds.
- Neglecting regular maintenance and inspections.
- Using improper or contaminated lubricants.
- Ignoring signs of bearing or seal problems.
7. Frequently Asked Questions (FAQs) About Trailer Bearings and Seals
Q: How often should I repack trailer bearings?
A: Repacking intervals vary based on operating conditions, trailer weight, and type of bearings used. Consult the manufacturer's recommendations or follow a six-month or 10,000-mile interval as a general guideline.
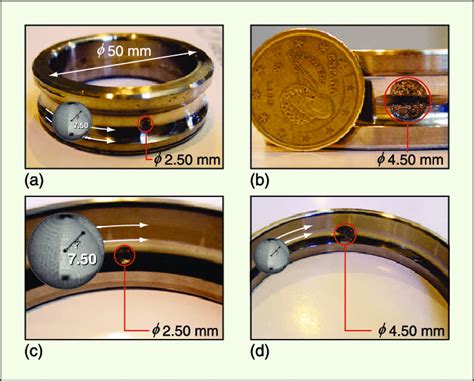
Q: What type of lubricant should I use for trailer bearings?
A: Use high-quality bearing grease specifically designed for trailer applications. Look for greases that meet industry standards such as NLGI GC-LB or NLGL 2.
Q: How do I know if a trailer bearing is failing?
A: Signs of bearing failure include excessive noise, vibration, or heat coming from the bearing assembly. If you notice any of these symptoms, promptly inspect the bearings for any damage or excessive wear.