Turntable Bearings: A Symphony of Rotation in Industrial Applications
The world of precision engineering revolves around turntable bearings, the unsung heroes of many industries, enabling seamless rotation and unparalleled accuracy in countless applications. These remarkable components are the maestro of motion, orchestrating smooth and effortless movements in machinery as diverse as wind turbines, medical imaging systems, and heavy-duty construction equipment.
Understanding Turntable Bearings
Turntable bearings, also known as slewing rings, are specialized bearing assemblies that facilitate rotation around a central axis. They consist of an outer race, an inner race, and a set of rolling elements, typically balls or rollers. The rolling elements are housed within the raceways of the inner and outer races, providing smooth and precise movement as the bearing rotates.
Applications of Turntable Bearings
The versatility of turntable bearings extends across a wide range of industries, including:

-
Wind turbines: Turntable bearings support the massive nacelles of wind turbines, enabling them to rotate smoothly to capture optimal wind conditions.
-
Medical imaging systems: In CT scanners and MRI machines, turntable bearings ensure precise rotation of the imaging components, delivering accurate diagnostic results.
-
Construction equipment: Excavators, cranes, and other heavy machinery rely on turntable bearings for stable and controlled movement during digging, lifting, and positioning operations.
-
Automotive engineering: Turntable bearings play a critical role in steering systems and suspension components, contributing to vehicle stability and maneuverability.
-
Aerospace applications: Turntable bearings support radar systems, antennas, and other mission-critical equipment in aircraft and spacecraft.
Types of Turntable Bearings
Turntable bearings come in various types, each designed to meet specific application requirements:
-
Single-row: Single-row turntable bearings are compact and economical, featuring a single row of rolling elements for moderate load capacities.
-
Double-row: Double-row turntable bearings offer enhanced load-carrying capacity and stability, utilizing two rows of rolling elements in a back-to-back arrangement.
-
Three-row: Three-row turntable bearings are designed for heavy-duty applications, providing exceptional load capacity and rigidity with triple rows of rolling elements.
-
Crossed-roller: Crossed-roller turntable bearings are characterized by crossed rollers arranged in perpendicular orientation, enabling high load capacity and precision in both radial and axial directions.
Key Features of Turntable Bearings
The performance of turntable bearings hinges on several key features:
-
Load capacity: The maximum load that a bearing can support, including radial, axial, and moment loads.
-
Precision: The accuracy of rotation, measured in terms of angular play and runout.
-
Durability: The bearing's ability to withstand wear, fatigue, and environmental conditions over its lifespan.
-
Efficiency: The amount of friction generated during rotation, which impacts energy consumption and bearing performance.
Benefits of Turntable Bearings
The integration of turntable bearings in various industries offers numerous advantages:

-
Smooth and precise rotation: Turntable bearings enable smooth and controlled rotation, reducing vibration and ensuring accurate positioning.
-
Increased load capacity: The robust construction of turntable bearings enables them to handle heavy loads, supporting demanding applications.
-
Enhanced stability: The wide contact area between the rolling elements and raceways provides exceptional stability, preventing unwanted movement.
-
Reduced maintenance: Turntable bearings are designed for low maintenance, with extended lubrication intervals and minimal need for adjustments.
-
Long lifespan: With proper lubrication and care, turntable bearings can provide years of reliable operation in demanding conditions.
Specifications of Turntable Bearings
When selecting a turntable bearing for a particular application, engineers consider several specifications:
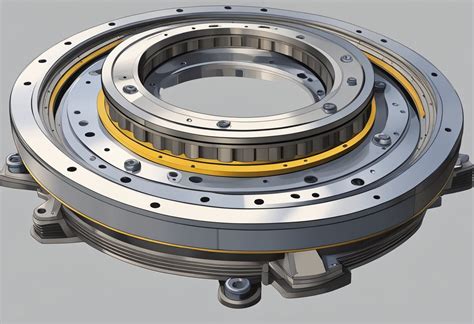
-
Bore size: The inner diameter of the bearing, which determines its compatibility with the shaft.
-
Outer diameter: The outer diameter of the bearing, which dictates the size of the supporting structure.
-
Thickness: The height of the bearing, which impacts its overall size and weight.
-
Weight: The mass of the bearing, which is a factor in equipment design and transportation.
Installation and Maintenance of Turntable Bearings
Proper installation and maintenance are crucial for maximizing the performance and lifespan of turntable bearings:

-
Installation: Turntable bearings should be installed according to manufacturer specifications, using appropriate tools and techniques to avoid damage.
-
Lubrication: Regular lubrication is essential to reduce friction and prevent premature wear. The type of lubricant and frequency of lubrication depend on the specific bearing design and application.
-
Inspection: Periodic inspections should be conducted to check for any signs of wear, damage, or contamination.
-
Troubleshooting: If problems arise, consulting an experienced technician or the bearing manufacturer is advisable to identify and resolve the issue promptly.
Potential Drawbacks of Turntable Bearings
While turntable bearings offer numerous benefits, it is important to consider potential drawbacks:
-
Cost: Turntable bearings can be relatively expensive, especially for large or high-performance models.
-
Size and weight: The size and weight of turntable bearings can be a limiting factor in space-constrained applications.
-
Complexity: The design and manufacturing of turntable bearings require precision engineering, which can increase the complexity and cost of the bearing.
FAQs on Turntable Bearings
For further clarification, here are answers to some frequently asked questions about turntable bearings:
- What are the typical materials used in turntable bearings?
-
Steel is a common material for turntable bearings, offering a balance of strength, durability, and affordability. Other materials include stainless steel, aluminum, and composite materials for specific performance requirements.
-
How do I determine the correct turntable bearing for my application?
-
Consider the load capacity, precision, durability, efficiency, and specifications (bore size, outer diameter, thickness, weight) in relation to the specific requirements of the application. Consulting an experienced engineer or bearing manufacturer is recommended.
-
What is the expected lifespan of a turntable bearing?
- The lifespan of a turntable bearing depends on various factors, including load conditions, lubrication, maintenance practices, and environmental conditions. With proper care, turntable bearings can provide years of reliable operation.
Call to Action
Embrace the power of turntable bearings to enhance the performance, precision, and durability of your machinery. Contact a reputable bearing manufacturer today to explore your options and find the ideal solution for your application.