Unveiling the Industrial Welding Robot: A Transformative Force in Manufacturing
The industrial welding robot, an epitome of technological advancement, has revolutionized the manufacturing industry, transforming production processes with unmatched precision, efficiency, and safety. These automated machines, equipped with advanced capabilities, are driving innovation and productivity across various sectors.
Why Industrial Welding Robots Matter
-
Enhanced Precision: Industrial welding robots execute welds with unparalleled accuracy, eliminating human error and ensuring consistent, high-quality results.
-
Increased Productivity: Robots operate tirelessly, working 24/7 without breaks, significantly boosting production output and minimizing downtime.
-
Reduced Labor Costs: Robots automate repetitive and dangerous tasks, freeing up skilled workers for more complex and value-added activities.
-
Improved Safety: Robots eliminate the risk of accidents and injuries associated with manual welding, creating a safer work environment for employees.
Benefits of Industrial Welding Robots
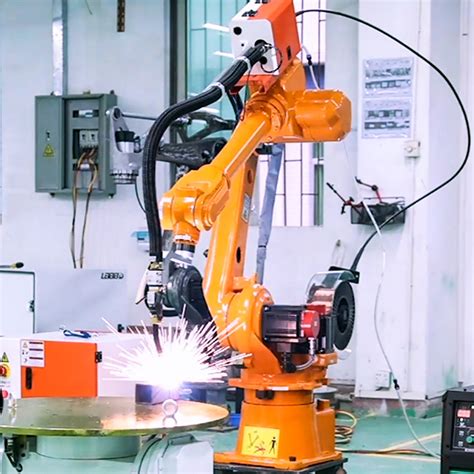
-
Cost Savings: Reduced labor costs, decreased rework, and increased productivity result in significant cost savings for businesses.
-
Enhanced Quality: Precision welding and consistent results lead to superior product quality, reducing defects and customer complaints.
-
Increased Efficiency: Robots operate at higher speeds and with greater accuracy, maximizing production efficiency and minimizing waste.
-
Improved Flexibility: Robots can be programmed to perform a wide range of welding tasks, from simple spot welds to complex robotic welding automation, offering adaptability to changing production needs.
Advanced Features of Industrial Welding Robots
-
Adaptive Control: Sensors and cameras enable robots to adjust welding parameters in real time, compensating for variations in materials and joint geometry.
-
Laser Scanning: Integrated lasers scan the workpiece, creating a digital map that guides the robot's movements for precise weld placement.
-
Intelligent Seam Tracking: Vision systems track the weld joint during the process, ensuring accuracy and preventing gaps or overlaps.
-
Remote Monitoring: Advanced systems allow for remote monitoring and control of robots, enabling real-time adjustments and troubleshooting from anywhere.
Pros and Cons of Industrial Welding Robots
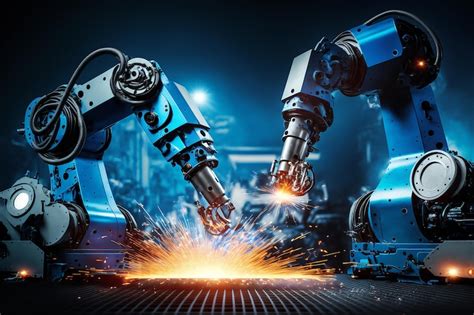
Pros:
- Enhanced precision and accuracy
- Increased productivity and throughput
- Reduced labor costs and improved efficiency
- Improved safety and quality
Cons:
- Higher initial investment costs
- Need for skilled operators and technicians
- Potential for downtime during maintenance or repairs
FAQs About Industrial Welding Robots
-
How much do industrial welding robots cost? Prices vary depending on the size, capabilities, and features of the robot. On average, a basic industrial welding robot can cost between $50,000 and $150,000.
-
What types of welding can industrial robots perform? Robots are capable of a wide range of welding processes, including MIG welding, TIG welding, spot welding, and arc welding.
-
How do I choose the right industrial welding robot for my application? Consider factors such as the size of the workpiece, type of welding required, desired accuracy, and budget. Consulting with an expert is recommended.
Interesting Stories
-
The Welding Robot and the Lollipop: A robot was programmed to weld a candy stick to a lollipop. However, the robot misunderstood the instructions and welded the lollipop to the welding torch, resulting in a sticky situation.
-
The Robot's Dance Party: A robot was left unsupervised during a welding session and started dancing, waving its welding arm around erratically. The resulting weld pattern looked like a modern art masterpiece.
-
The Robot's Mishap: A robot was performing a welding task when it accidentally bumped into a nearby tool, causing the tool to fall into the molten weld. The quick-thinking robot grabbed the tool and held it steady until the weld cooled, preventing a potential disaster.
Lessons Learned
-
Importance of Programming: Clear and precise programming is crucial to avoid unexpected outcomes.
-
Need for Supervision: Robots should be closely monitored to prevent errors and ensure safety.
-
Benefits of Fail-Safes: Implementing fail-safes can minimize the impact of unexpected events and prevent accidents.
Effective Strategies for Implementing Industrial Welding Robots
-
Define Clear Objectives: Determine the specific goals and expected benefits of using industrial welding robots.
-
Assess Existing Processes: Analyze current welding operations to identify areas for improvement and automation.
-
Plan for Implementation: Develop a detailed plan outlining the robot's integration into the production process, including training, maintenance, and safety measures.
-
Invest in Quality Robots: Choose robots from reputable manufacturers with proven reliability and performance records.
-
Provide Comprehensive Training: Ensure operators and technicians receive thorough training on robot operation, programming, and maintenance.
Useful Tables
Robot Vendor |
Model |
Price Range |
ABB |
IRB 6700 |
$100,000 - $150,000 |
KUKA Robotics |
KR 350 |
$60,000 - $100,000 |
Fanuc Robotics |
R-2000iB |
$50,000 - $80,000 |
Welding Process |
Description |
Applications |
MIG Welding |
Metal Inert Gas welding uses a continuously fed wire electrode in a shielding gas environment. |
Automotive, shipbuilding, construction |
TIG Welding |
Tungsten Inert Gas welding uses a non-consumable tungsten electrode in a shielding gas environment. |
Aerospace, medical, food and beverage |
Spot Welding |
Resistance welding process where two metal sheets are joined together using heat and pressure. |
Automotive, electronics, appliance manufacturing |
Industrial Welding Robot Benefits |
Impact on Manufacturing |
Enhanced Precision |
Reduced scrap rates, improved product quality |
Increased Productivity |
Higher production output, shorter lead times |
Reduced Labor Costs |
Redeployment of skilled workers to higher-value tasks |
Improved Safety |
Elimination of hazardous tasks, improved working conditions |
Call to Action
Embrace the transformative power of industrial welding robots to revolutionize your manufacturing operations. By adopting these automated machines, you can achieve unprecedented levels of precision, productivity, and safety, propelling your business to new heights of success.