Hydrodynamic Bearings: The Key to Frictionless Motion
Hydrodynamic bearings are a type of bearing that uses a thin film of lubricant to separate two surfaces in relative motion. This film of lubricant prevents metal-to-metal contact, which reduces friction and wear. Hydrodynamic bearings are used in a wide variety of applications, including engines, turbines, and pumps.
How Hydrodynamic Bearings Work
Hydrodynamic bearings work by creating a wedge-shaped film of lubricant between the two surfaces in relative motion. This wedge-shaped film is created by the hydrodynamic pressure generated by the relative motion of the surfaces. The hydrodynamic pressure is highest at the point of closest approach between the two surfaces, and it decreases as the distance between the surfaces increases. This pressure gradient creates a force that opposes the relative motion of the surfaces, which reduces friction.
The thickness of the lubricant film in a hydrodynamic bearing is typically very small, on the order of a few micrometers. This thin film of lubricant is sufficient to prevent metal-to-metal contact, but it does not significantly increase the drag on the bearing. As a result, hydrodynamic bearings are very efficient and can operate at high speeds.

Advantages of Hydrodynamic Bearings
Hydrodynamic bearings offer a number of advantages over other types of bearings, including:
-
Low friction: Hydrodynamic bearings have very low friction, which can result in significant energy savings.
-
Long life: Hydrodynamic bearings can last for many years, even in demanding applications.
-
High load capacity: Hydrodynamic bearings can support very high loads, making them ideal for use in heavy-duty applications.
-
Quiet operation: Hydrodynamic bearings are very quiet, making them ideal for use in applications where noise is a concern.
Applications of Hydrodynamic Bearings
Hydrodynamic bearings are used in a wide variety of applications, including:
-
Engines: Hydrodynamic bearings are used in engines to support the crankshaft and camshaft.
-
Turbines: Hydrodynamic bearings are used in turbines to support the rotor.
-
Pumps: Hydrodynamic bearings are used in pumps to support the impeller.
-
Compressors: Hydrodynamic bearings are used in compressors to support the rotor.
-
Machine tools: Hydrodynamic bearings are used in machine tools to support the spindle.
Types of Hydrodynamic Bearings
There are a number of different types of hydrodynamic bearings, including:

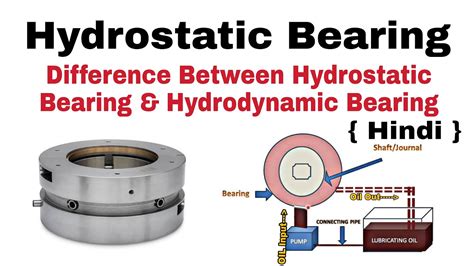
-
Journal bearings: Journal bearings are used to support a rotating shaft.
-
Thrust bearings: Thrust bearings are used to support a load in the axial direction.
-
Radial bearings: Radial bearings are used to support a load in the radial direction.
-
Tilting pad bearings: Tilting pad bearings are used to support a load in both the radial and axial directions.
Design of Hydrodynamic Bearings
The design of a hydrodynamic bearing is critical to its performance. The following factors must be considered when designing a hydrodynamic bearing:
-
Load: The load that the bearing will be supporting.
-
Speed: The speed at which the bearing will be operating.
-
Lubricant: The type of lubricant that will be used.
-
Clearance: The clearance between the bearing surfaces.
Materials for Hydrodynamic Bearings
Hydrodynamic bearings are typically made from steel, bronze, or aluminum. The choice of material depends on the application. Steel is the most common material for hydrodynamic bearings, as it offers a good combination of strength, wear resistance, and corrosion resistance. Bronze is a good choice for applications where corrosion resistance is a concern. Aluminum is a good choice for applications where weight is a concern.
Lubrication of Hydrodynamic Bearings
Hydrodynamic bearings require a lubricant to create the wedge-shaped film that prevents metal-to-metal contact. The lubricant can be oil, grease, or water. The type of lubricant that is used depends on the application. Oil is the most common lubricant for hydrodynamic bearings, as it offers a good combination of lubricity, viscosity, and thermal stability. Grease is a good choice for applications where oil lubrication is not practical. Water is a good choice for applications where the bearing is exposed to water.
Maintenance of Hydrodynamic Bearings
Hydrodynamic bearings require regular maintenance to ensure that they are operating properly. The following maintenance tasks should be performed on a regular basis:
-
Inspection: The bearing should be inspected for wear, damage, and contamination.
-
Cleaning: The bearing should be cleaned to remove any dirt, debris, or contaminants.
-
Lubrication: The bearing should be lubricated with the appropriate lubricant.
-
Adjustment: The bearing should be adjusted to ensure that the clearance between the bearing surfaces is correct.
Troubleshooting Hydrodynamic Bearings
The following problems can occur with hydrodynamic bearings:

-
Excessive wear: Excessive wear can be caused by a number of factors, including overloading, improper lubrication, and contamination.
-
Seizure: Seizure can occur if the bearing is overloaded or if the lubricant is not sufficient.
-
Noise: Noise can be caused by a number of factors, including misalignment, improper lubrication, and wear.
Stories About Hydrodynamic Bearings
Here are three humorous stories about hydrodynamic bearings:
-
The case of the disappearing oil: A technician was called to repair a hydrodynamic bearing that was making a lot of noise. The technician discovered that the bearing was not getting any oil. He traced the oil line back to the oil reservoir and found that the reservoir was empty. The technician then refilled the reservoir and the bearing started working properly again.
-
The case of the worn-out bearing: A technician was called to repair a hydrodynamic bearing that was not supporting the load properly. The technician discovered that the bearing was worn out. He replaced the bearing and the machine started working properly again.
-
The case of the misaligned bearing: A technician was called to repair a hydrodynamic bearing that was making a lot of noise. The technician discovered that the bearing was misaligned. He realigned the bearing and the noise went away.
What We Can Learn from These Stories
These stories teach us that it is important to:
-
Inspect: Inspect hydrodynamic bearings on a regular basis to identify any problems early.
-
Maintain: Perform regular maintenance on hydrodynamic bearings to keep them operating properly.
-
Troubleshoot: Troubleshoot hydrodynamic bearings if they are not operating properly.
Tips and Tricks for Using Hydrodynamic Bearings
Here are some tips and tricks for using hydrodynamic bearings:
-
Use the right lubricant: The type of lubricant that you use is critical to the performance of a hydrodynamic bearing. Choose a lubricant that is appropriate for the application.
-
Maintain the correct clearance: The clearance between the bearing surfaces is critical to the performance of a hydrodynamic bearing. Adjust the clearance to the manufacturer's specifications.
-
Monitor the bearing temperature: The temperature of a hydrodynamic bearing is an indication of its condition. Monitor the bearing temperature to identify any problems early.
-
Consider using a bearing isolator: A bearing isolator can help to protect a hydrodynamic bearing from contamination.
Advanced Features of Hydrodynamic Bearings
Some hydrodynamic bearings are equipped with advanced features, such as:
-
Grooves: Grooves can be machined into the bearing surfaces to improve the flow of lubricant.
-
Pockets: Pockets can be machined into the bearing surfaces to trap lubricant.
-
Coatings: Coatings can be applied to the bearing surfaces to improve wear resistance and corrosion resistance.
Why Hydrodynamic Bearings Matter
Hydrodynamic bearings are an important part of many machines. They reduce friction, wear, and noise, and they can extend the life of a machine. Hydrodynamic bearings are used in a wide variety of applications, from engines and turbines to pumps and compressors.
How Hydrodynamic Bearings Benefit You
Hydrodynamic bearings offer a number of benefits, including:
-
Energy savings: Hydrodynamic bearings can reduce friction, which can result in significant energy savings.
-
Longer life: Hydrodynamic bearings can last for many years, even in demanding applications.
-
Improved performance: Hydrodynamic bearings can improve the performance of a machine by reducing friction and wear.
-
Reduced noise: Hydrodynamic bearings are very quiet, making them ideal for use in applications where noise is a concern.
Conclusion
Hydrodynamic bearings are an important part of many machines. They offer a number of benefits, including energy savings, longer life, improved performance, and reduced noise. If you are looking for a bearing that will provide you with the best possible performance, then a hydrodynamic bearing is the right choice for you.
References