Automating Industrial Processes with KUKA Robots: A Comprehensive Guide
KUKA robots are the epitome of industrial automation, revolutionizing various industries with their precision, efficiency, and reliability. This comprehensive guide delves into the world of KUKA industrial robots, exploring their capabilities, applications, and the transformative impact they have on modern manufacturing.
The Rise of Collaborative Robotics
In the past decade, the rise of collaborative robotics has significantly impacted industrial automation. KUKA robots are at the forefront of this revolution, allowing humans and robots to work side-by-side, leading to increased productivity, reduced costs, and improved workplace safety.
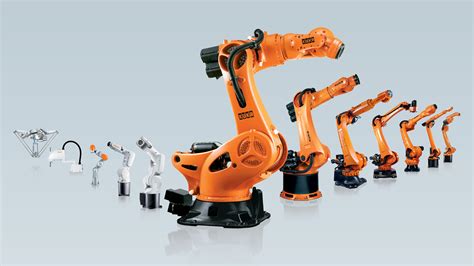
Key Advantages of KUKA Industrial Robots
-
Unmatched Precision: KUKA robots boast exceptional precision and repeatability, ensuring consistent and high-quality results.
-
Versatility and Agility: They are designed to seamlessly integrate into various production lines, adapting to complex tasks and diverse manufacturing environments.
-
Robust and Durable: Constructed using durable materials and advanced engineering, KUKA robots withstand harsh industrial conditions and extended periods of operation.
-
User-Friendly Interface: Their intuitive software and easy-to-use programming interfaces enable quick setup and straightforward operation, minimizing downtime.
Applications of KUKA Robots in Industry
KUKA industrial robots find applications across a wide range of industries, performing tasks that are hazardous, repetitive, or require extreme precision.
-
Automotive Manufacturing: Assembly, welding, painting, and part inspection.
-
Electronics Assembly: Component insertion, soldering, and testing.
-
Pharmaceutical Industry: Packaging, dispensing, and laboratory automation.
-
Healthcare: Surgical assistance, rehabilitation, and medical device manufacturing.
-
Food and Beverage: Packaging, processing, and quality control.
The Economic Impact of KUKA Robots
The adoption of KUKA industrial robots has resulted in significant economic benefits for businesses:

-
Increased Productivity: They automate tasks, freeing up human workers to focus on higher-value activities.
-
Reduced Labor Costs: Robots can operate 24/7, reducing the need for additional shifts and overtime pay.
-
Improved Product Quality: Precision and consistency ensure consistent product quality, minimizing defects and reducing waste.
-
Enhanced Safety: Robots handle hazardous tasks, reducing the risk of injuries or accidents in the workplace.
Case Studies: KUKA Robots in Action
Story 1
A manufacturing company struggling with persistent bottlenecks on its assembly line invested in a KUKA robot. The robot's precision and speed increased production by 25%, significantly reducing downtime and improving overall efficiency.
Lesson Learned: KUKA robots can solve production bottlenecks, leading to substantial productivity gains.
Story 2
A medical device manufacturer found itself facing ergonomic challenges in its assembly process. By implementing a KUKA collaborative robot, the company reduced repetitive motions and improved the well-being of its workers, resulting in a happier and more productive workforce.
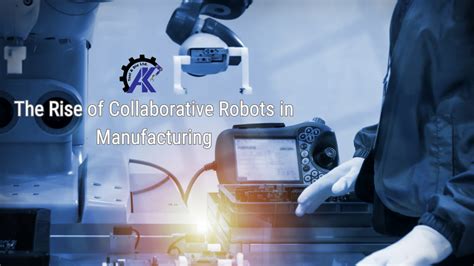
Lesson Learned: Collaborative robotics can enhance workplace ergonomics, promoting both efficiency and employee satisfaction.
Story 3
A food processing plant faced the challenge of maintaining consistent product quality. A KUKA robot was installed to perform delicate packaging tasks, ensuring that every package met the highest standards. The result was a significant reduction in product damage and customer complaints.
Lesson Learned: KUKA robots can elevate product quality and minimize waste, enhancing customer satisfaction.
Effective Strategies for Implementing KUKA Robots
-
Identify Suitable Applications: Assess your production processes to determine where KUKA robots can replace or enhance human tasks.
-
Consider Training and Development: Invest in training for staff to operate, program, and maintain the robots effectively.
-
Integrate with Existing Systems: Ensure seamless integration with existing production lines and software to maximize efficiency.
-
Monitor and Optimize Performance: Regularly monitor robot performance and make adjustments to improve productivity and ROI.
Tips and Tricks for Using KUKA Robots
-
Optimize Path Planning: Optimize robot movements to minimize cycle times and improve efficiency.
-
Use Simulation Tools: Utilize simulation software to plan and test robot programs before implementation, reducing downtime.
-
Automate as Much as Possible: Leverage the full capabilities of KUKA robots to automate a wide range of tasks, maximizing cost savings.
-
Monitor Maintenance Regularly: Adhere to maintenance schedules and proactively identify and resolve potential issues to extend the robots' lifespan.
Step-by-Step Approach to Implementing KUKA Robots
-
Assessment and Planning: Determine suitable applications, identify required equipment, and plan the integration process.
-
Robot Selection: Choose the appropriate KUKA robot model based on performance, payload, and application requirements.
-
System Design and Integration: Design the robot cell layout, integrate with existing systems, and conduct safety risk assessments.
-
Programming and Training: Program the robot, train staff, and optimize path planning.
-
Implementation and Monitoring: Implement the robot cell, monitor performance, and continuously improve processes.
Pros and Cons of KUKA Industrial Robots
Pros:
- Exceptional precision and repeatability
- Versatility and adaptability to various applications
- Robust and durable construction for harsh environments
- Intuitive software and user-friendly interface
- Proven record of increasing productivity and reducing costs
Cons:
- Higher initial investment compared to manual labor
- May require specialized training for programming and maintenance
- Can be susceptible to power outages or technical issues
- May displace certain jobs, requiring workforce retraining and upskilling
Frequently Asked Questions (FAQs)
-
What are the different types of KUKA industrial robots?
- KUKA offers a wide range of robots, including articulated arms, SCARA robots, and delta robots, each suited for specific applications.
-
How do I choose the right KUKA robot for my application?
- Consider factors such as payload capacity, reach, speed, and environmental conditions to select the optimal robot model.
-
What is the cost of a KUKA industrial robot?
- Costs vary depending on the robot model, configuration, and application; it is recommended to consult with authorized KUKA distributors.
-
How do I program a KUKA robot?
- KUKA provides intuitive programming software, making it accessible for both experienced and novice users.
-
What are the safety considerations when using KUKA robots?
- KUKA robots adhere to stringent safety standards; proper training, risk assessments, and protective measures are crucial to ensure operator safety.
-
How do I maintain a KUKA industrial robot?
- Regular maintenance is essential to ensure optimal performance; follow recommended inspection and maintenance schedules to extend the robot's lifespan.
Call to Action
Embracing KUKA industrial robots is a strategic investment that can transform your manufacturing processes. Contact an authorized KUKA distributor today to discuss your specific needs and explore how these advanced robots can unlock new levels of efficiency, precision, and cost savings. Invest in the future of industrial automation with KUKA and witness the transformative power of collaborative robotics.
Appendix
Table 1: KUKA Robot Models and Specifications
Robot Model |
Payload Capacity (kg) |
Reach (m) |
Speed (m/s) |
KR 6 R900 SIXX |
6 |
900 |
3.7 |
KR 10 R1100 SIXX |
10 |
1100 |
4.5 |
KR 16 R1000 SIXX |
16 |
1000 |
5.4 |
KR 210 R2700 ultra |
210 |
2700 |
2.5 |
KR QUANTEC PA |
1300 |
3200 |
3.4 |
Table 2: Applications of KUKA Industrial Robots
Industry |
Applications |
Automotive |
Assembly, welding, painting |
Electronics |
Component insertion, soldering, testing |
Pharmaceutical |
Packaging, dispensing, laboratory automation |
Healthcare |
Surgical assistance, rehabilitation, medical device manufacturing |
Food and Beverage |
Packaging, processing, quality control |
Table 3: Benefits of KUKA Industrial Robots
Benefit |
Description |
Increased Productivity |
Automate tasks, free up human workers for higher-value activities |
Reduced Labor Costs |
Robots can operate 24/7, reduce need for additional shifts and overtime pay |
Improved Product Quality |
Precision and consistency ensure consistent product quality, minimize defects and reduce waste |
Enhanced Safety |
Robots handle hazardous tasks, reduce risk of injuries or accidents in the workplace |