The Essential Guide to Hydraulic Bearing Pullers: Safety, Applications, and Maintenance
Hydraulic bearing pullers are indispensable tools in the maintenance and repair of industrial machinery. They provide a safe and efficient method for removing bearings from shafts, gears, and other components. This comprehensive guide will delve into the intricacies of hydraulic bearing pullers, covering everything from safety precautions to maintenance tips.
Safety Precautions
When working with hydraulic bearing pullers, safety should be paramount. Here are some crucial precautions to observe:
-
Always inspect the puller before use: Check for any signs of damage or wear on the hydraulic lines, fittings, and components. Never use a damaged puller.
-
Use the correct puller for the job: Choose a puller with the appropriate capacity and reach for the bearing you need to remove.
-
Securely attach the puller to the bearing: Use the correct bolts or clamps to ensure a firm grip on the bearing. Ensure the puller is centered on the bearing.
-
Slowly apply hydraulic pressure: Gradually increase the pressure until the bearing loosens. Avoid sudden or excessive force, as this can damage the bearing or the puller.
-
Wear appropriate safety gear: Utilize eye protection, gloves, and earplugs when operating a hydraulic bearing puller.
Applications of Hydraulic Bearing Pullers
Hydraulic bearing pullers have a wide range of applications in various industries, including:
-
Automotive: Removing bearings from transmissions, differentials, and wheels
-
Industrial machinery: Disassembling gearboxes, pumps, and compressors
-
Heavy equipment: Removing bearings from engines, transmissions, and steering systems
-
Aerospace: Servicing aircraft engines and landing gear
-
Marine: Maintaining marine engines and propellers
Maintenance of Hydraulic Bearing Pullers
Proper maintenance is essential to ensure the longevity and reliability of your hydraulic bearing puller. Here are some key maintenance tips:

-
Clean the puller after each use: Remove dirt, grease, and debris from the hydraulic lines, fittings, and components.
-
Lubricate moving parts regularly: Apply a light lubricant to all moving parts, such as the hydraulic cylinder and the puller head.
-
Inspect the hydraulic lines and fittings: Check for leaks or damage on a regular basis. Replace any damaged components immediately.
-
Store the puller properly: Keep the puller in a clean and dry environment when not in use. Protect the hydraulic lines from damage.
Why Hydraulic Bearing Pullers Matter
Hydraulic bearing pullers play a critical role in industrial maintenance by:

-
Providing a safe and efficient method for removing bearings without damaging them or surrounding components.
-
Saving time and labor: Hydraulic pullers can quickly and easily remove bearings, reducing downtime during repairs.
-
Preventing unnecessary damage: Controlled hydraulic force eliminates the need for excessive force, which can damage components.
-
Maintaining equipment reliability: By removing bearings properly, hydraulic pullers help extend the lifespan of machinery and reduce maintenance costs.
Benefits of Using Hydraulic Bearing Pullers
Utilizing hydraulic bearing pullers offers numerous benefits, including:
-
Safety: Hydraulic force reduces the risk of injury to the user.
-
Efficiency: Powerful hydraulics remove bearings quickly and effortlessly.
-
Precision: Controlled force ensures the removal of bearings without damaging surrounding components.
-
Versatility: Hydraulic pullers can be used on various sizes and types of bearings.
-
Cost-effectiveness: Hydraulic pullers save time and labor, thereby reducing maintenance costs.
Pros and Cons of Hydraulic Bearing Pullers
Like any tool, hydraulic bearing pullers have both advantages and disadvantages.

Pros:
- Safe and efficient
- Powerful and versatile
- Easy to use
- Durable and reliable
Cons:
- Can be expensive
- Require hydraulic power source
- May not be suitable for removing very large bearings
Effective Strategies for Using Hydraulic Bearing Pullers
To maximize the effectiveness of hydraulic bearing pullers, consider these strategies:
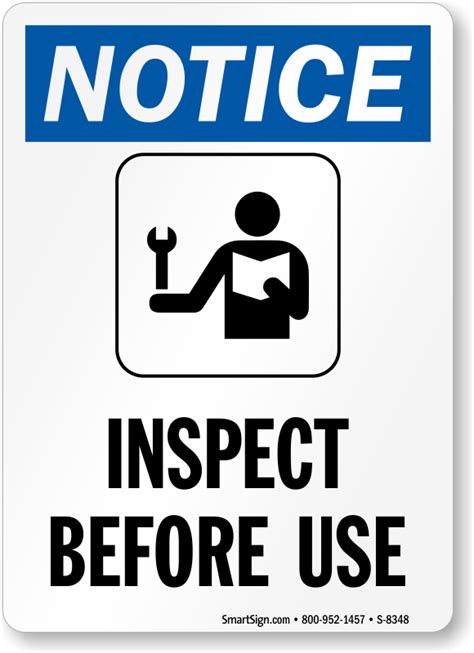
-
Choose the correct puller: Select a puller with the appropriate capacity, reach, and design for the bearing you need to remove.
-
Center the puller: Align the puller head directly over the center of the bearing. This ensures even force distribution and prevents damage to the bearing or the puller.
-
Apply pressure gradually: Increase hydraulic pressure slowly until the bearing starts to loosen. Avoid sudden or excessive force.
-
Monitor pressure: Use a pressure gauge to monitor the hydraulic pressure and avoid exceeding the rated capacity of the puller.
-
Use the correct attachments: Select the appropriate attachment for the type of bearing you are removing. This ensures maximum grip and prevents damage to the bearing.
Tips and Tricks for Using Hydraulic Bearing Pullers
Here are some helpful tips and tricks to enhance your hydraulic bearing puller usage:
-
Use a penetrating lubricant: Apply a penetrating lubricant to the bearing surface to loosen it before applying hydraulic force.
-
Protect the bearing surface: Use a thin layer of cloth or soft metal between the bearing surface and the puller head to prevent damage.
-
Use a hydraulic booster: Consider using a hydraulic booster to increase the force output of the puller for stubborn bearings.
-
Take breaks: Allow the puller to cool down after extended use. This prevents overheating and damage to the hydraulic components.
-
Keep the puller clean: Regularly clean the puller head, hydraulic lines, and fittings to prevent dirt and debris from affecting performance.
Common Mistakes to Avoid When Using Hydraulic Bearing Pullers
To prevent potential problems, avoid these common mistakes:
-
Overloading the puller: Using a puller beyond its rated capacity can damage the puller or cause injury.
-
Using excessive force: Sudden or excessive force can damage the bearing or the puller. Always apply pressure gradually.
-
Misaligning the puller: Improper alignment can cause damage to the bearing or the puller. Center the puller head directly over the bearing.
-
Neglecting maintenance: Poor maintenance can compromise the safety and performance of the puller. Regularly inspect, clean, and lubricate the puller.
-
Using the wrong attachments: Improper attachments can damage the bearing or prevent effective removal. Always use the correct attachment for the type of bearing you are removing.
Story 1: The Stubborn Bearing
A mechanic was tasked with removing a bearing from an industrial gearbox. He used a hydraulic bearing puller, but the bearing refused to budge. Frustrated, he applied more and more force, but the bearing remained stuck. Finally, he realized that he had neglected to lubricate the bearing surface. After applying a penetrating lubricant, the bearing loosened easily with a gentle pull.
Lesson: Patience and proper lubrication are crucial for successful bearing removal.
Story 2: The Broken Puller
A technician attempted to remove a bearing from a heavy-duty truck engine. He used a hydraulic bearing puller, but the puller head suddenly snapped off. Upon inspection, he discovered that he had overloaded the puller by using an extension bar that exceeded the rated capacity.
Lesson: Always use the correct puller and avoid exceeding its rated capacity.
Story 3: The Misaligned Puller
A repair technician was removing a bearing from an aircraft landing gear. He positioned the hydraulic bearing puller head slightly off-center. As he applied pressure, the bearing tilted and became jammed. The technician had to disassemble the entire landing gear to free the bearing.
Lesson: Proper alignment of the puller head is essential to prevent damage to the bearing and the puller.
Table 1: Common Hydraulic Bearing Puller Sizes and Capacities
Size |
Capacity |
Applications |
Small |
Up to 5 tons |
Automotive, small machinery |
Medium |
5-15 tons |
Industrial machinery, heavy equipment |
Large |
15-50 tons |
Heavy machinery, marine engines |
Extra Large |
Over 50 tons |
Specialized applications, such as aircraft engines |
Table 2: Features and Benefits of Different Hydraulic Bearing Puller Head Designs
Design |
Features |
Benefits |
Single-Acting |
Uses hydraulic pressure to extend the ram |
Simple and economical |
Double-Acting |
Uses hydraulic pressure to extend and retract the ram |
More versatile and powerful |
Self-Centering |
Automatically aligns the puller head |
Easy to use and reduces the risk of damage |
Table 3: Maintenance Schedule for Hydraulic Bearing Pullers
Component |
Maintenance Task |
Frequency |
Hydraulic Lines |
Inspect for leaks and damage |
Every 6 months |
Hydraulic Fittings |
Inspect for leaks and corrosion |
Every 6 months |
Hydraulic Cylinder |
Inspect for leaks and wear |
Annually |
Puller Head |
Inspect for wear and damage |
Annually |
Moving Parts |
Lubricate with a light lubricant |
Every 6 months |
Conclusion
Hydraulic bearing pullers are essential tools for safely and efficiently removing bearings from a wide range of machinery and equipment. By understanding the safety precautions, applications, maintenance requirements, and effective usage techniques discussed in this guide, you can maximize the benefits of hydraulic bearing pullers and ensure the safe and efficient operation of your machinery.