Angular Contact Bearings: The Ultimate Guide for Engineers and Designers
Angular contact bearings are indispensable components in a wide range of industries, where precise rotation and efficient load management are crucial. This comprehensive guide delves into the world of angular contact bearings, providing valuable insights into their types, design considerations, applications, and maintenance tips.

1. Introduction: Understanding Angular Contact Bearings
- Angular contact bearings are rolling-element bearings that accommodate combined radial and axial loads acting in the same direction.
- The unique design of angular contact bearings allows them to withstand thrust loads while handling radial loads simultaneously.
- They are characterized by their ability to transmit axial loads up to 60% of their radial load capacity.
2. Types of Angular Contact Bearings
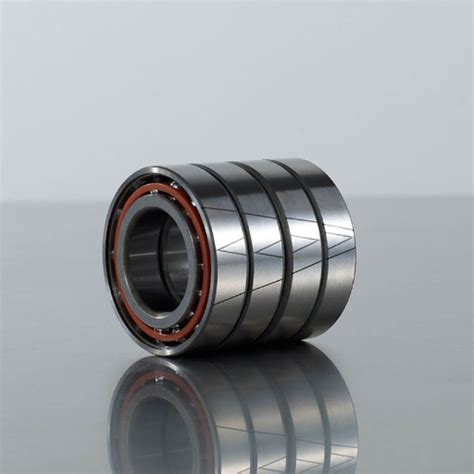
Angular contact bearings come in two main configurations:

Single-Row Angular Contact Bearings
- Designed with a single row of rolling elements, these bearings are compact and suitable for applications with limited axial load requirements.
- They are often used in high-speed applications due to their reduced friction and heat generation.
Double-Row Angular Contact Bearings
- Feature two rows of rolling elements, providing higher axial load capacity and rigidity.
- Double-row bearings are commonly used in applications where high thrust loads and precision are required, such as machine tools and aerospace components.
Contact Angle and Preload
- The contact angle, measured between the bearing raceway and the ball path, determines the axial load capacity of the bearing.
- Bearings with larger contact angles handle higher axial loads, while those with smaller contact angles offer better radial load capacity.
- Preload can be applied to angular contact bearings to enhance stiffness and reduce axial play.
Materials
- Angular contact bearings are typically made of high-grade bearing steel, such as AISI 52100 or M50.
- For corrosive environments, stainless steel or ceramic materials can be used.
3. Applications of Angular Contact Bearings
Angular contact bearings find applications in diverse industries, including:

Machine Tools
- High-speed spindles and rotary tables rely on angular contact bearings to handle combined loads and ensure precision.
Aerospace
- Jet engines, landing gear, and flight control systems utilize angular contact bearings for their exceptional load capacity and reliability.
Automotive
- Transmissions, gearboxes, and wheel bearings benefit from the durability and load-carrying capabilities of angular contact bearings.
Industrial Machinery
- Pumps, compressors, and turbines employ angular contact bearings to withstand harsh operating conditions and extended lifespans.
4. Design Considerations for Angular Contact Bearings
-
Load Capacity: Determine the required radial and axial load capacities based on the application requirements.
-
Contact Angle: Select the appropriate contact angle to balance axial and radial load capacity needs.
-
Preload: Consider applying preload to enhance stiffness and reduce axial play.
-
Lubrication: Choose the appropriate lubricant and lubrication method to maintain bearing performance and extend its life.
-
Sealing: Select suitable seals to prevent contamination and retain lubricants.
5. Maintenance of Angular Contact Bearings
Proper maintenance is crucial to ensure optimal performance and extended lifespan of angular contact bearings. Key maintenance practices include:
Regular Inspection
- Monitor bearing temperature, vibration, and noise levels regularly.
- Inspect for signs of wear, contamination, or damage.
Lubrication
- Ensure timely lubrication according to manufacturer recommendations.
- Choose the appropriate lubricant and lubrication method for the specific application and operating conditions.
Cleaning
- Clean bearings periodically to remove contamination and debris.
- Use appropriate cleaning methods and solvents to avoid bearing damage.
Replacement
- Replace bearings when they reach the end of their service life or show signs of severe wear or damage.
- Follow proper mounting procedures to ensure correct installation and avoid premature failure.
6. Tips and Tricks
- Use matched bearing sets to ensure proper load distribution and reduce vibration.
- Consider using angular contact bearings with integrated sensors for real-time monitoring and predictive maintenance.
- Apply surface treatments, such as nitriding or coatings, to enhance bearing durability and corrosion resistance.
7. Interesting Stories
Story 1
An engineer was troubleshooting a faulty bearing in a high-speed spindle. After meticulous inspection, he discovered that the bearing raceway had been damaged due to insufficient lubrication. The engineer promptly replaced the bearing and implemented a more rigorous lubrication schedule, resulting in improved spindle performance and extended bearing life.
Story 2
A team of designers was tasked with developing a new gearbox for a heavy-duty industrial application. They initially chose a double-row angular contact bearing for its high axial load capacity. However, during testing, they encountered excessive noise and vibration. Upon further analysis, they realized that a single-row bearing with a larger contact angle would have been more suitable for the application, providing both the required load capacity and reduced noise levels.
Story 3
In a humorous incident, a maintenance technician was inspecting a bearing assembly and accidentally dropped a wrench into the bearing. The wrench wedged between the rolling elements, causing the bearing to seize up. The quick-thinking technician used a magnet to retrieve the wrench and prevented any further damage to the machine.
What We Learn
- Proper lubrication is essential for the longevity of angular contact bearings.
- Careful design considerations can lead to optimal bearing performance and reduced noise levels.
- Unexpected incidents during maintenance require quick thinking and the correct tools to avoid costly downtime.
8. How to Step-by-Step Approach
Step 1: Identify Application Requirements
- Determine the operating conditions, including radial and axial load requirements, speed, and temperature range.
Step 2: Select Bearing Type and Contact Angle
- Choose a single-row or double-row bearing based on the load capacity needs.
- Select the appropriate contact angle to balance axial and radial load requirements.
Step 3: Determine Preload and Lubrication
- Consider applying preload to enhance stiffness and reduce axial play.
- Choose the appropriate lubricant and lubrication method for the specific application conditions.
Step 4: Select Materials and Seals
- Choose high-grade bearing steel or specialized materials based on operating conditions and corrosion resistance needs.
- Select suitable seals to prevent contamination and retain lubricants.
Step 5: Mount and Maintain Bearings
- Follow proper mounting procedures to ensure correct installation and prevent premature failure.
- Implement regular inspection, lubrication, and cleaning practices to maximize bearing performance and lifespan.
9. Why Angular Contact Bearings Matter
Angular contact bearings play a crucial role in numerous industries due to their:
- Ability to handle combined radial and axial loads
- High load capacity and precision
- Compact design for space-constrained applications
- Durability and long service life
10. Benefits of Using Angular Contact Bearings
-
Improved Load Capacity: Handle heavy combined loads in both radial and axial directions.
-
Enhanced Rigidity: Provide higher stiffness compared to other bearing types.
-
Reduced Friction and Heat Generation: Single-row bearings offer low friction and heat generation in high-speed applications.
-
Compact Design: Allow for smaller bearing arrangements in space-limited machinery.
-
Extended Lifespan: Offer long-lasting performance with proper lubrication and maintenance.
11. FAQs
11.1 What is the difference between single-row and double-row angular contact bearings?
- Single-row bearings have one row of rolling elements, while double-row bearings have two rows.
- Double-row bearings offer higher axial load capacity and rigidity than single-row bearings.
11.2 What is the purpose of contact angle in angular contact bearings?
- The contact angle determines the axial load capacity of the bearing.
- Bearings with larger contact angles can handle higher axial loads, while those with smaller contact angles offer better radial load capacity.
11.3 What are the common applications of angular contact bearings?
- Machine tools, aerospace components, automotive transmissions, and industrial machinery.
11.4 How to maintain angular contact bearings?
- Regular inspection, lubrication, cleaning, and replacement when necessary.
11.5 What materials are used in angular contact bearings?
- High-grade bearing steel, stainless steel, or ceramic materials.
11.6 Can angular contact bearings be used in high-temperature applications?
- Yes, but special materials and lubricants may be required.
11.7 What are the typical industry standards for angular contact bearings?
- ISO 15:232, DIN 623-1, and ANSI/ABMA Std 15.
## 12. Conclusion
Angular contact bearings are vital components in modern machinery, providing efficient load management and precise rotation. By understanding their types, design considerations, applications, and maintenance practices