Trailer Wheel Bearings: Everything You Need to Know to Keep Your Wheels Rolling
Introduction
Trailer wheel bearings are critical components that enable your trailer to roll smoothly and safely. They support the weight of the trailer and reduce friction between the axle and the wheel. Neglecting trailer wheel bearings can lead to premature failure, costly repairs, and even dangerous road conditions. Understanding the importance of trailer wheel bearings and implementing proper maintenance practices is essential for the longevity and safety of your trailer.
The Importance of Trailer Wheel Bearings
Trailer wheel bearings play a vital role in ensuring the smooth and efficient operation of your trailer. They:
-
Reduce Friction: Bearings enable the wheels to rotate freely by minimizing friction between the axle and wheel. This reduces the effort required to pull the trailer and improves fuel efficiency.
-
Support Weight: The bearings support the weight of the trailer, acting as a load-bearing surface between the axle and wheel. Proper bearing lubrication and adjustment are crucial to ensure even weight distribution and prevent premature failure.
-
Prevent Excessive Heat: Well-lubricated bearings dissipate heat effectively, preventing excessive heat buildup that can damage the bearings, seals, and other trailer components.
-
Extend Tire Life: Properly maintained bearings prevent excessive wear and tear on tires, extending their lifespan and improving overall trailer performance.
Common Types of Trailer Wheel Bearings
There are two primary types of trailer wheel bearings:

-
Tapered Roller Bearings: Conical-shaped rollers that are positioned between two tapered races. They are known for their durability, high load capacity, and ability to withstand misalignment.
-
Ball Bearings: Ball-shaped bearings that run between an inner and outer race. They offer lower resistance and are commonly used in smaller trailers.
Signs of Failing Trailer Wheel Bearings
Ignoring trailer wheel bearing issues can result in severe consequences. Early detection and prompt repair are crucial to prevent catastrophic failures. Common signs of failing bearings include:
-
Noise: Squealing, grinding, or humming noises coming from the wheels while driving.
-
Vibration: Excessive vibration felt through the trailer or steering wheel.
-
Wobbly Wheels: Wheels that appear loose or wobble when shaken by hand.
-
Grease Leakage: Grease leaking from the wheel hubs, indicating damaged seals or worn bearings.
-
Increased Temperature: Unusually hot wheel hubs due to friction and lack of lubrication.
Failure Causes and Prevention
Trailer wheel bearing failures can occur due to several factors, including:

-
Inadequate Lubrication: Insufficient or contaminated grease leads to excessive friction and wear.
-
Overloading: Exceeding the trailer's weight capacity puts excessive stress on the bearings.
-
Improper Installation: Incorrect bearing installation or adjustment can result in misalignment and premature failure.
-
Water and Contaminant Ingress: Water and dirt can penetrate the bearing seals, causing corrosion and abrasive damage.
-
Lack of Maintenance: Neglecting regular inspections, lubrication, and adjustment can lead to premature bearing failure.
To prevent trailer wheel bearing failures, implement these best practices:

-
Regular Maintenance: Inspect bearings regularly, check grease levels, and adjust them as needed.
-
Proper Lubrication: Use high-quality, trailer-specific grease and follow the manufacturer's recommended lubrication intervals.
-
Avoid Overloading: Ensure the trailer is not overloaded to prevent excessive stress on the bearings.
-
Correct Installation: Have bearings installed and adjusted by trained professionals to ensure proper alignment and longevity.
-
Prevent Contaminant Ingress: Use bearing seals and protective covers to prevent water and dirt from entering the bearings.
Maintenance and Adjustment
Proper trailer wheel bearing maintenance is crucial for optimal performance and extended lifespan. Follow these steps:
-
Safety First: Engage the parking brake, chock the wheels, and lift the trailer safely before performing any maintenance.
-
Remove the Hubcap: Remove the hubcap or dust cover to expose the wheel hub and bearings.
-
Clean and Inspect: Thoroughly clean and inspect the bearings, races, and seals for any wear, damage, or contamination.
-
Lubricate: Apply a generous amount of high-quality, trailer-specific grease to the bearings and races.
-
Adjust: Tighten the axle nut to the manufacturer's recommended torque specifications to achieve proper bearing adjustment.
-
Install and Check: Reinstall the hubcap or dust cover and check for excessive play or binding.
Common Mistakes to Avoid
Avoid these common pitfalls when working with trailer wheel bearings:
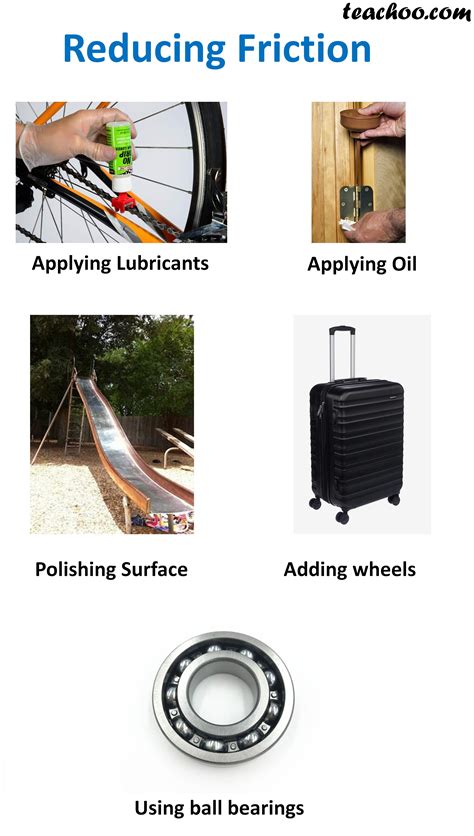
-
Using Automotive Grease: Automotive grease is not suitable for trailer bearings and can lead to premature failure.
-
Overtightening: Exceeding the recommended torque specifications can damage bearings and races.
-
Ignoring Loose Bearings: Loose bearings can cause excessive wear and vibration.
-
Skipping Regular Maintenance: Neglecting regular inspections and lubrication can significantly shorten bearing life.
-
Delaying Repairs: Ignoring early signs of bearing failure can lead to catastrophic consequences and expensive repairs.
Step-by-Step Bearing Replacement Guide
Replacing trailer wheel bearings is a relatively straightforward task. Here's a step-by-step guide:
-
Safety First: Engage the parking brake, chock the wheels, and lift the trailer safely before proceeding.
-
Remove the Wheel: Remove the lug nuts and carefully lift the wheel off the axle.
-
Remove the Hub: Using a hub puller or a hammer and chisel, carefully remove the hub assembly from the spindle.
-
Extract Bearings: Inspect the bearings, races, and seals for any wear or damage. Remove the old bearings from the hub and spindle.
-
Clean and Prepare: Thoroughly clean the hub, spindle, and new bearings using a degreaser and a clean cloth.
-
Install Bearings: Press or carefully tap the new bearings onto the spindle and into the hub.
-
Install Seals: Replace the old seals with new ones, ensuring they are properly seated in their grooves.
-
Repack Bearings: Apply a generous amount of high-quality, trailer-specific grease to the bearings, races, hub, and spindle.
-
Reassemble Hub: Carefully reassemble the hub assembly back onto the spindle.
-
Adjust and Install: Tighten the axle nut to the manufacturer's recommended torque specifications to achieve proper bearing adjustment.
-
Reinstall Wheel: Reinstall the wheel and tighten the lug nuts to the specified torque.
Troubleshooting and FAQs
1. What causes my trailer wheels to wobble?
Wobbly trailer wheels can indicate worn or loose wheel bearings, loose lug nuts, or a bent axle.
2. How often should I lubricate my trailer wheel bearings?
For most trailers, it is recommended to lubricate the wheel bearings every 5,000-7,500 miles or annually, whichever comes first.
3. Can I adjust trailer wheel bearings too tightly?
Yes, overtightening the axle nut can damage the bearings, races, and seals, leading to premature failure.
4. What type of grease should I use for trailer wheel bearings?
Always use high-quality, trailer-specific grease designed for heavy-duty applications.
5. Is it safe to drive with worn trailer wheel bearings?
No, operating a trailer with worn wheel bearings is dangerous and can result in catastrophic bearing failure, potentially causing an accident.
6. How much does it cost to replace trailer wheel bearings?
The cost of replacing trailer wheel bearings varies depending on the trailer size, bearing type, and labor charges. On average, you can expect to pay between $150-$500 per wheel.
Humorous Stories and Conclusion
-
The Squeaky Wheel: A trailer owner ignored the squeaking sound coming from his trailer's wheels. As he drove down the highway, the bearings seized, causing the wheel to detach and roll down the road, narrowly missing a speeding car. Lesson learned: Never ignore strange noises coming from your trailer.
-
The Towing Nightmare: A driver towed a heavy trailer for over 100 miles without checking the wheel bearings. The bearings overheated and seized, causing the trailer to sway violently and fishtail dangerously on the road. By the time he pulled over, the bearings were completely destroyed, requiring a roadside repair and a hefty tow bill. Lesson learned: Regular bearing inspection and lubrication are crucial for safe towing.
-
The Overtightened Nut: A novice mechanic tightened the trailer wheel bearing axle nut with all his might. After a short drive, the wheel hub began to smoke, emitting a burning smell. The mechanic had overtightened the nut, damaging the bearings and spindle. Lesson learned: Always follow the manufacturer's recommended torque specifications when adjusting bearings.
Conclusion
Trailer wheel bearings play a vital role in the safe and efficient operation of your trailer. Regular maintenance, proper lubrication, and timely repairs are essential for their longevity. Ignoring wheel bearing issues can lead to premature failure, costly repairs, and even dangerous road conditions. By understanding the importance of trailer wheel bearings and implementing best practices, you can ensure your trailer rolls smoothly and safely for years to come.