The Ultimate Guide to Linear Roller Bearings: Empowering Precision Motion in Industrial Automation
Linear roller bearings, often referred to as linear motion bearings or slide bearings, have become indispensable in modern industrial automation and precision machinery applications. These bearings enable smooth, precise, and low-friction linear motion, catering to a wide range of industries, including manufacturing, packaging, robotics, semiconductor, medical equipment, and more.
Understanding Linear Roller Bearings: A Comprehensive Overview
Definition and Mechanism
A linear roller bearing is a type of bearing designed to facilitate linear motion along a straight axis. It comprises a cylindrical outer sleeve, precision-ground inner rollers, and a cage or retainer that separates and guides the rollers. When a load is applied, the rollers roll smoothly within the sleeve, reducing friction and providing precise linear movement.
Types of Linear Roller Bearings
Linear roller bearings come in various types, each catering to specific application requirements:
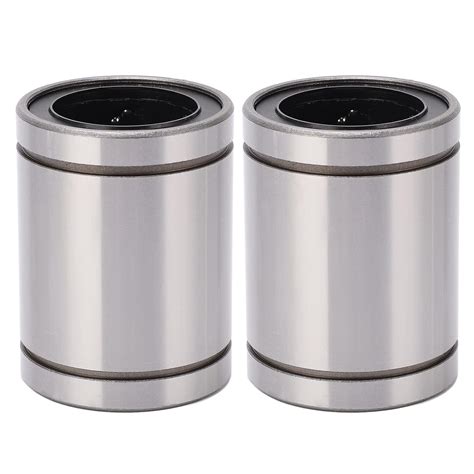
-
Ball linear bearings: Utilize ball elements instead of rollers, offering lower load capacity but higher speeds and less noise.
-
Crossed roller linear bearings: Feature rollers arranged in a 90-degree cross pattern, providing high load capacity and rigidity.
-
Pillow block linear bearings: Pre-mounted in a housing, allowing for easy installation and adjustment.
-
Round rail linear bearings: Feature a circular rail instead of a flat surface, enabling higher precision and smoother motion.
-
Square rail linear bearings: Suitable for applications requiring high rigidity and resistance to moment loads.
Key Features and Benefits
Linear roller bearings offer numerous advantages over other types of linear bearings:

-
Low friction: Rollers minimize friction, ensuring smooth and efficient motion.
-
High load capacity: Designed to withstand heavy axial and radial loads.
-
High precision: Precision-ground components provide accurate and consistent motion.
-
Long lifespan: Durable construction and low wear rates ensure extended service life.
-
Compact design: Compact size allows for space optimization in tight installations.
-
Corrosion resistance: Available in stainless steel or coated versions for corrosion-prone environments.
Applications of Linear Roller Bearings: Empowering Industries
Linear roller bearings find widespread application across various industries:
-
Manufacturing: Automation systems, robotic arms, machine tools, and assembly lines.
-
Packaging: Conveyors, filling machines, and labeling systems.
-
Robotics: Motion control systems, actuators, and manipulators.
-
Semiconductor: Wafer handling, lithography equipment, and inspection machinery.
-
Medical equipment: Surgery robots, imaging systems, and patient positioning equipment.
Selection and Sizing of Linear Roller Bearings: Ensuring Optimal Performance
Selecting the appropriate linear roller bearing is crucial for ensuring optimal performance and reliability. Factors to consider include:
-
Load capacity: Determine the axial and radial loads that the bearing will withstand.
-
Speed: Consider the desired speed of the linear motion.
-
Accuracy: Specify the required precision and accuracy of the movement.
-
Environmental conditions: Consider factors such as temperature, corrosion, and dust.
Installation and Maintenance: Ensuring Longevity and Reliability
Proper installation and maintenance practices are essential for the longevity and reliability of linear roller bearings:

Installation Best Practices
-
Clean and inspect: Clean the bearing and shaft thoroughly before installation.
-
Proper alignment: Ensure proper alignment between the bearing and shaft to prevent premature wear.
-
Correct mounting: Follow the manufacturer's instructions for proper mounting methods.
Maintenance Tips
-
Regular lubrication: Lubricate bearings periodically to reduce friction and extend lifespan.
-
Inspection and monitoring: Conduct regular inspections for wear, damage, or contamination.
-
Replacement: Replace bearings when they reach the end of their service life or if they show signs of failure.
Performance Data and Standards: Assuring Quality and Reliability
Established industry standards ensure the quality and performance of linear roller bearings:
-
ANSI/AFBMA Standard 18: Defines dimensional standards and tolerances for linear roller bearings.
-
ISO 14728-1: Specifies performance requirements and test methods for linear roller bearings.
-
DIN 6415: Provides standards for round rail linear bearings.
-
JIS B1555: Japanese Industrial Standard for linear roller bearings.
Independent organizations conduct rigorous testing to evaluate the performance of linear roller bearings. According to a study by the Bearing Research Institute (BRI), linear roller bearings can achieve a rated life of over 100,000 hours when properly selected and maintained.
Effective Strategies: Maximizing Bearing Performance
Implement effective strategies to optimize the performance and lifespan of linear roller bearings:
-
Load distribution: Distribute loads evenly across multiple bearings to reduce stress concentrations.
-
Preloading: Apply a slight preload to bearings to eliminate slack and increase rigidity.
-
Lubrication optimization: Use high-quality lubricants specifically designed for linear bearings.
-
Environmental protection: Shield bearings from contaminants and moisture to prevent premature failure.
Tips and Tricks: Enhancing Bearing Operation
Follow these tips and tricks to further enhance the operation of linear roller bearings:
-
Use vibration damping materials: Reduce vibrations and noise by incorporating vibration damping materials.
-
Consider thermal effects: Compensate for thermal expansion and contraction to prevent bearing damage.
-
Implement fail-safe mechanisms: Design fail-safe mechanisms to prevent catastrophic failures in critical applications.
Step-by-Step Approach: Installing and Maintaining Linear Roller Bearings
Installation Procedure
-
Prepare the shaft: Clean the shaft and apply a light layer of lubricant.
-
Slide on the bearing: Carefully slide the bearing onto the shaft.
-
Secure the bearing: Secure the bearing using a retaining ring or other appropriate method.
-
Align and preload: Align the bearing properly and apply the necessary preload.
Maintenance Procedure
-
Inspect regularly: Monitor bearings for signs of wear, damage, or contamination.
-
Lubricate periodically: Lubricate bearings according to the manufacturer's recommendations.
-
Avoid overtightening: Overtightening fasteners can damage bearings and impair performance.
-
Replace when necessary: Replace bearings when they reach the end of their service life or exhibit signs of failure.
Frequently Asked Questions (FAQs): Addressing Common Concerns
1. How do linear roller bearings differ from ball bearings?
Linear roller bearings offer higher load capacity and rigidity compared to ball bearings.
2. What factors affect the lifespan of linear roller bearings?
Load, speed, lubrication, alignment, and maintenance practices all influence bearing lifespan.
3. How can I reduce friction in linear roller bearings?
Proper lubrication, using low-friction materials, and optimizing load distribution can minimize friction.
4. What are the advantages of using preloaded linear roller bearings?
Preloading eliminates backlash and improves rigidity, precision, and accuracy.

5. How do I select the right linear roller bearing for my application?
Consider factors such as load capacity, speed, accuracy, environmental conditions, and mounting requirements.
6. Can linear roller bearings be used in corrosive environments?
Yes, stainless steel or coated linear roller bearings are available for corrosion-prone applications.
Call to Action: Enhance Precision and Efficiency with Linear Roller Bearings
Linear roller bearings are essential components for precision motion in industrial automation and machine design. By understanding their operation, selecting the appropriate type, installing and maintaining them correctly, and implementing effective strategies, you can optimize their performance and reliability. Embracing these principles will empower your designs with increased precision, efficiency, and extended service life.