Angular Contact Bearings: The Ultimate Guide
Angular contact bearings, a type of rolling element bearing, are critical components in a wide range of applications, from high-speed machinery to heavy-duty industrial equipment. Their unique design and features make them ideal for applications requiring high precision, axial load capacity, and reduced friction.
Understanding Angular Contact Bearings
Essentially, angular contact bearings are designed to support both radial and axial loads acting in a single direction. The bearings consist of an inner ring, an outer ring, and a set of rolling elements (usually balls or rollers) arranged in a contact angle. This contact angle, typically ranging from 15 to 45 degrees, determines the bearing's load carrying capacity and axial rigidity.
Types of Angular Contact Bearings
Angular contact bearings are categorized based on their design and construction. Common types include:
-
Single-row angular contact bearings: The most widely used type, supporting axial loads in one direction only.
-
Double-row angular contact bearings: Consisting of two rows of rolling elements, these bearings support axial loads in both directions.
-
Four-point contact bearings: Designed with four rows of rolling elements, they provide high rigidity and load capacity.
-
Tapered roller bearings: A specialized type of angular contact bearing with tapered rollers, suitable for heavy axial and radial loads.
Advantages and Applications of Angular Contact Bearings
Angular contact bearings offer several advantages, including:

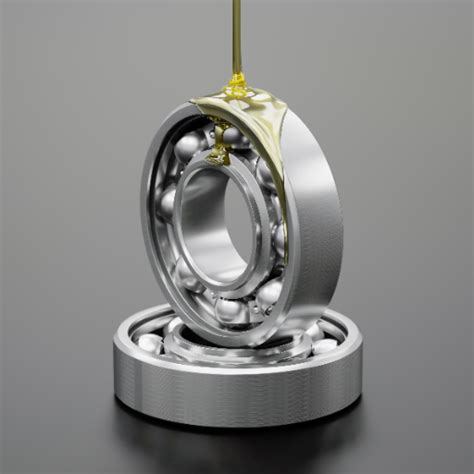
-
High precision: Their precision manufacturing and accurate contact ensure minimal runout and wobble.
-
Axial load capacity: The contact angle allows them to support significant axial loads along with radial loads.
-
Reduced friction: The rolling elements minimize friction, resulting in lower power loss and increased efficiency.
-
Durability and longevity: Proper lubrication and maintenance extend the life of angular contact bearings.
These advantages make angular contact bearings suitable for various applications, such as:
- Machine tool spindles
- Electric motors and generators
- Aerospace components
- Precision instruments
- High-speed machinery
Selecting the Right Angular Contact Bearings
Choosing the appropriate angular contact bearing for a specific application requires careful consideration of several factors:

-
Load requirements: Determine the axial and radial loads the bearing will encounter.
-
Speed: Consider the rotational speed of the application.
-
Accuracy: Specify the required precision and runout tolerances.
-
Lubrication: Choose a bearing type compatible with the intended lubrication method.
-
Size and space limitations: Take into account the available space and dimensional constraints.
Mounting and Maintenance of Angular Contact Bearings
Proper mounting and maintenance are crucial for optimal performance and longevity of angular contact bearings. Key considerations include:
-
Preload: Apply the appropriate preload to minimize bearing clearances and improve accuracy.
-
Lubrication: Use high-quality lubricants compatible with the bearing type and application conditions.
-
Alignment: Ensure precise alignment between the inner and outer rings to distribute loads evenly.
-
Regular inspection: Monitor the bearings periodically for wear, damage, or excessive vibration.
Tips and Tricks
- Consider using prelubricated bearings to extend maintenance intervals.
-
Lubricate bearings twice as often during the initial run-in period.
-
Avoid overtightening bearing mountings, as it can increase friction and reduce bearing life.
-
Use proper tools for mounting and dismounting bearings to prevent damage.
-
Store bearings in a clean and dry environment to prevent corrosion.
Common Mistakes to Avoid
-
Incorrect preload: Too little or excessive preload can lead to premature bearing failure.
-
Improper lubrication: Insufficient or unsuitable lubrication can increase friction and wear.
-
Misalignment: Poor alignment can create uneven load distribution, causing premature bearing damage.
-
Overloading: Exceeding the bearing's load capacity can lead to catastrophic failure.
-
Contamination: Dirt or debris entering the bearing can cause wear, noise, and reduced performance.
Humorous Stories and Lessons Learned
-
The Wobbly Turbine: A technician was tasked with installing angular contact bearings in a critical gas turbine application. They neglected to apply the proper preload, resulting in a wobbly rotor and excessive vibration. The subsequent investigation revealed the technician had confused the preload with the torque settings for the bearing locknuts.
Lesson: Always follow manufacturer's instructions and double-check preload specifications.
-
The Greasy Dilemma: A maintenance engineer was responsible for servicing angular contact bearings in a high-speed conveyor system. Overzealous in their duties, they liberally applied grease to the bearings, mistakenly believing "more is better." Unfortunately, the excessive grease acted as a trap for dirt and debris, leading to accelerated bearing wear and premature failure.
Lesson: Use the correct amount of lubricant and follow maintenance schedules to avoid over-greasing.
-
The Bearing Burnout: An operator was troubleshooting a malfunctioning machine, which exhibited overheating and noise from the angular contact bearings. Upon inspection, the bearings were found to be completely dry, indicating a lack of lubrication. Further investigation revealed the operator had bypassed the automatic lubrication system, believing it to be unnecessary.
Lesson: Regular lubrication is essential for bearing performance and longevity.
Step-by-Step Approach to Mounting Angular Contact Bearings
-
Prepare the mounting surfaces: Clean and inspect the inner and outer bearing seats to ensure they are free of debris and damage.
-
Apply preload: Measure and apply the appropriate preload using a hydraulic nut, spring washer, or other preload mechanism.
-
Lubricate the bearings: Apply a thin layer of compatible lubricant to the rolling elements and contact surfaces.
-
Install the bearings: Carefully align and insert the bearings into their respective seats, ensuring proper seating and orientation.
-
Tighten the mounting bolts: Hand-tighten the bolts initially, then gradually tighten them using a torque wrench to the specified values.
-
Verify alignment: Check the alignment using a dial indicator or other precision instrument to ensure concentricity and axial runout are within acceptable limits.
FAQs
-
What is the difference between single-row and double-row angular contact bearings?
Single-row bearings support axial loads in one direction, while double-row bearings support axial loads in both directions.
-
How do I determine the appropriate preload for angular contact bearings?
Refer to the manufacturer's specifications or use preload calculation formulas based on the bearing type, size, and application requirements.
-
What type of lubrication is recommended for angular contact bearings?
High-quality mineral or synthetic oils or greases specifically designed for rolling element bearings are recommended.
-
How often should I inspect angular contact bearings?
Regular inspection intervals depend on the application and operating conditions. A general guideline is to inspect bearings every 2,000 - 4,000 operating hours.
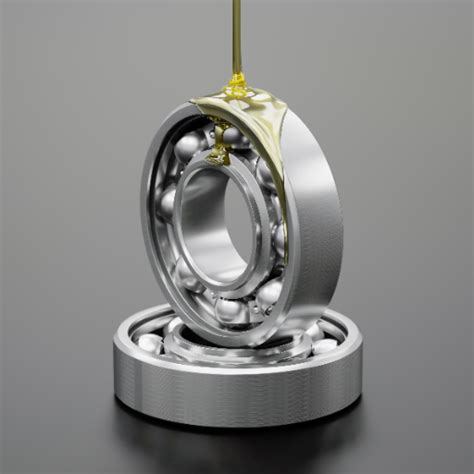
-
What is the shelf life of angular contact bearings?
Properly stored angular contact bearings can have a shelf life of 5 years or more.
-
How can I extend the life of angular contact bearings?
Follow proper mounting and maintenance procedures, avoid overloading, ensure proper lubrication, and regularly inspect the bearings for wear or damage.