Waukesha Bearings: A Comprehensive Guide for Optimal Performance and Maintenance
Introduction
Waukesha bearings are renowned for their exceptional quality and reliability in demanding industrial applications. Their precision engineering and robust construction ensure smooth operation, reduced downtime, and extended equipment life. Understanding the intricacies of Waukesha bearings is crucial for industries seeking to maximize their equipment's performance and minimize maintenance costs. This comprehensive guide delves into the characteristics, types, applications, and best practices for maintaining Waukesha bearings, equipping readers with the knowledge to optimize their operations.
Transition: Overview of Waukesha Bearings
According to the American Bearing Manufacturers Association (ABMA), approximately 80% of all bearing failures are preventable with proper maintenance. Waukesha bearings are designed and manufactured with stringent quality standards to minimize these failures. Let's explore the key aspects of these bearings.
Characteristics of Waukesha Bearings
-
Precision Manufacturing: Waukesha bearings are meticulously crafted to meet precise tolerances, ensuring proper fit and minimizing friction.
-
Robust Construction: Constructed from high-grade materials and featuring sturdy designs, Waukesha bearings withstand heavy loads and harsh operating conditions.
-
Long Service Life: Proper maintenance practices and optimal operating conditions contribute to the exceptional longevity of Waukesha bearings, reducing replacement costs and downtime.
-
Reliability: Waukesha bearings are renowned for their ability to operate under varying loads and speeds, delivering consistent performance across a wide range of applications.
-
Efficiency: The precision design and low-friction operation of Waukesha bearings minimize energy consumption, promoting machinery efficiency.
Transition: Types of Waukesha Bearings
Waukesha bearings come in various types to suit specific application requirements. Let's examine the most common types.
Types of Waukesha Bearings
1. Roller Bearings
-
Cylindrical Roller Bearings: Designed for high radial loads and moderate thrust loads, these bearings are suitable for demanding applications such as gearboxes and rolling mills.
-
Tapered Roller Bearings: Ideal for applications involving combined radial and thrust loads, tapered roller bearings are commonly found in heavy machinery, such as cranes and construction equipment.
-
Spherical Roller Bearings: These bearings accommodate misalignment and heavy radial and thrust loads, making them suitable for machinery subjected to shock loads or harsh operating conditions.
2. Ball Bearings
-
Deep Groove Ball Bearings: Versatile and widely used, deep groove ball bearings support radial loads and moderate axial loads in various applications, including electric motors and conveyors.
-
Angular Contact Ball Bearings: Designed to accommodate combined radial and axial loads, angular contact ball bearings are commonly used in high-speed applications, such as machine tool spindles and gas turbines.
Transition: Applications of Waukesha Bearings
Waukesha bearings find diverse applications across industries. Let's explore some key sectors that rely on their reliability.

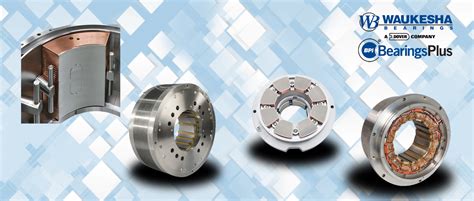
Applications of Waukesha Bearings
-
Power Generation: Waukesha bearings support high-speed turbines and generators, ensuring smooth operation and long service life in power plants.
-
Mining: The rugged construction of Waukesha bearings makes them ideal for heavy-duty machinery used in mining operations, including conveyors and excavators.
-
Oil and Gas: The ability of Waukesha bearings to withstand extreme temperatures and corrosive environments makes them essential for equipment in oil and gas extraction and processing.
-
Aerospace: The high precision and reliability of Waukesha bearings are critical for aerospace applications, such as aircraft engines and landing gear.
-
Construction: Waukesha bearings are used in heavy machinery, such as cranes and bulldozers, to support heavy loads and demanding operating conditions.
Transition: Maintenance Best Practices for Waukesha Bearings
Proper maintenance is paramount for maximizing the performance and service life of Waukesha bearings. Let's review essential best practices.
Best Practices for Maintaining Waukesha Bearings
-
Regular Inspection: Periodically inspect bearings for signs of wear, damage, or contamination to identify potential problems early on.
-
Proper Lubrication: Use the recommended lubricants and follow the prescribed lubrication schedule to maintain optimal bearing performance and prevent premature failure.
-
Avoid Overloading: Ensure that bearings are not subjected to excessive loads, which can cause deformation or premature wear.
-
Monitor Operating Conditions: Keep track of bearing temperature, vibration levels, and other operating parameters to detect abnormalities and address them promptly.
-
Clean Storage: Store bearings in a clean, dry environment to prevent corrosion and contamination, especially during extended periods of non-use.
Transition: Troubleshooting Common Problems
Despite following best practices, some common problems can arise with Waukesha bearings. Let's explore how to identify and resolve these issues.

Troubleshooting Common Problems with Waukesha Bearings
Problem |
Possible Cause |
Solution |
Excessive Noise |
Defective bearing |
Replace the bearing |
High Temperature |
Overloading |
Reduce the load on the bearing |
Vibration |
Misalignment |
Check alignment and correct as necessary |
Premature Wear |
Insufficient lubrication |
Follow the recommended lubrication schedule and use high-quality lubricants |
Corrosion |
Exposure to moisture |
Keep bearings clean and dry, apply rust preventive coatings if necessary |
Transition: Effective Strategies for Optimizing Performance
Beyond proper maintenance, several strategies can enhance the overall performance of Waukesha bearings.
Effective Strategies for Optimizing Waukesha Bearing Performance
-
Use the Right Bearing for the Application: Selecting the appropriate bearing type for the specific operating conditions is crucial for optimal performance and longevity.
-
Monitor Bearing Condition Regularly: Implementing a proactive maintenance program, including regular inspections and condition monitoring, can identify potential issues early and prevent catastrophic failures.
-
Invest in High-Quality Lubricants: Using high-quality lubricants specifically designed for Waukesha bearings ensures optimal performance and extended service life.
-
Train Maintenance Personnel: Proper training of maintenance personnel on Waukesha bearings and their maintenance procedures is essential for effective operations.
-
Collaborate with Bearing Manufacturers: Consulting with Waukesha bearing manufacturers can provide valuable insights and recommendations for specific applications and operating conditions.
Transition: Humorous Stories and Lessons Learned
While technical aspects are crucial, a bit of humor can also shed light on lessons learned in the field. Let's share some amusing stories related to Waukesha bearings.
Humorous Stories and Lessons Learned
-
The Overzealous Maintenance Technician: Once upon a time, a maintenance technician was so eager to replace a Waukesha bearing that he accidentally installed it upside down. The machine promptly seized up, much to his embarrassment. Lesson learned: Always double-check your work.
-
The Misaligned Motor: A manufacturing plant was experiencing excessive vibration from a motor. After hours of troubleshooting, it was discovered that the motor had been misaligned by a mere fraction of an inch. Once properly aligned, the vibration disappeared. Lesson learned: Even small misalignments can have significant consequences.
-
The Forgotten Grease Gun: An operator neglected to lubricate a crucial Waukesha bearing on a conveyor belt. The result was a seized bearing and a halted production line. Lesson learned: Never underestimate the importance of proper lubrication.
Transition: Common Mistakes to Avoid
To ensure the longevity and optimal performance of Waukesha bearings, it's important to avoid common mistakes.
Common Mistakes to Avoid with Waukesha Bearings
-
Overloading the Bearing: Exceeding the load capacity of a bearing can cause premature failure or deformation. Always ensure that bearings are properly sized for the application.
-
Improper Lubrication: Using the wrong lubricant or neglecting to lubricate bearings can lead to increased friction, wear, and eventual failure. Follow the manufacturer's recommendations for lubrication.
-
Ignoring Bearing Condition: Failing to monitor bearing condition through regular inspections and condition monitoring can result in undetected problems that escalate into major failures.
-
Improper Storage: Bearings should be stored in a clean, dry environment to prevent corrosion and contamination. Never store bearings directly on the floor or in humid conditions.
-
Mishandling Bearings: Using improper tools or techniques to handle bearings can damage their precision surfaces or seals, leading to premature failure. Always handle bearings with care.
Transition: Step-by-Step Approach to Bearing Maintenance
To ensure effective and comprehensive maintenance of Waukesha bearings, follow these steps.
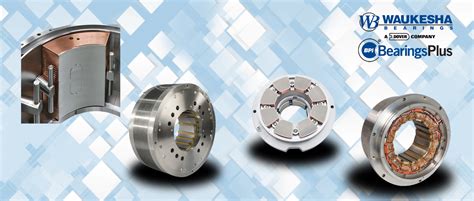
Step-by-Step Approach to Waukesha Bearing Maintenance
-
Preparation: Gather the necessary tools, lubricants, and cleaning supplies. Inspect the bearing and surrounding area for any signs of damage or contamination.
-
Removal: Carefully remove the bearing from its housing using the appropriate tools. Note the orientation of the bearing and any special mounting arrangements.
-
Cleaning: Clean the bearing thoroughly using a suitable solvent and a soft brush. Inspect the bearing for any signs of wear, damage, or debris.
-
Inspection: Examine the bearing's races, rollers, and seals for any signs of damage or wear. If significant damage is present, the bearing may need to be replaced.
-
Lubrication: Apply the recommended lubricant to the bearing's races and rollers. Ensure that the bearing is properly lubricated before reinstallation.
-
Reinstallation: Carefully reinstall the bearing into its housing, ensuring proper alignment and orientation. Tighten the bearing to the manufacturer's specifications.
-
Testing: Operate the bearing under load to verify its proper function. Monitor the bearing for any unusual noises or vibrations, indicating potential problems.
Transition: Pros and Cons of Different Waukesha Bearing Types
Different types of Waukesha bearings have varying advantages and disadvantages. Let's compare the most common types.
Pros and Cons of Different Waukesha Bearing Types