Unlocking the Power of Waukesha Bearings: A Comprehensive Guide
Introduction
Waukesha bearings are renowned for their exceptional reliability, durability, and performance in demanding industrial applications. These bearings are the cornerstone of various machinery, including engines, pumps, compressors, and generators. Understanding their design, types, and applications is crucial for maximizing their potential.
Types of Waukesha Bearings
Waukesha bearings come in a wide range of types, each designed to meet specific requirements. Some of the most common types include:
-
Sleeve Bearings: These bearings consist of a solid cylindrical shaft rotating within a cylindrical bearing sleeve. They provide high load-carrying capacity and are often used in slow-speed applications.
-
Journal Bearings: Similar to sleeve bearings, journal bearings support a rotating shaft within a bearing housing. They offer higher precision and reduced friction compared to sleeve bearings.
-
Anti-Friction Bearings: These bearings utilize rolling elements (such as balls or rollers) between the shaft and bearing housing. They provide lower friction and longer operating life but have lower load-carrying capacity than sleeve and journal bearings.
-
Hydrodynamic Bearings: These bearings rely on a thin film of lubricant to separate the rotating surfaces. They offer very low friction and are used in high-speed applications.
-
Self-Aligning Bearings: These bearings allow for some misalignment between the shaft and housing, compensating for misalignment in machinery.
Applications of Waukesha Bearings
Waukesha bearings find widespread use in a variety of industrial settings, including:

-
Power Generation: Generators, engines, and turbines utilize Waukesha bearings to support high loads and ensure smooth operation in power plants.
-
Oil and Gas: Pumps, compressors, and other equipment in the oil and gas industry rely on Waukesha bearings for reliability and durability in harsh environments.
-
Mining and Construction: Bearings from Waukesha are essential for heavy machinery used in mining and construction, including excavators, bulldozers, and cranes.
-
Marine: Propulsion systems, generators, and pumps on ships and offshore platforms utilize Waukesha bearings for their corrosion resistance and high performance.
-
Food and Beverage: Waukesha bearings are used in food and beverage processing equipment, ensuring precision and hygiene.
Benefits of Waukesha Bearings
Waukesha bearings offer numerous advantages, including:
-
Enhanced Reliability: The robust design and high-quality materials used in Waukesha bearings ensure long life and minimal downtime.
-
Increased Durability: These bearings can withstand extreme loads, temperatures, and harsh operating conditions.
-
Improved Performance: Waukesha bearings reduce friction, minimize vibration, and optimize machinery efficiency.
-
Reduced Maintenance: The precision construction and sealed designs of Waukesha bearings reduce the need for frequent maintenance and lubrication.
-
Energy Efficiency: By reducing friction, Waukesha bearings contribute to energy savings and environmental sustainability.
Selection Considerations
Choosing the right Waukesha bearing for a specific application requires careful consideration of the following factors:
-
Load and Speed: The load-carrying capacity and operating speed of the bearing are critical factors in determining the appropriate type and size.
-
Operating Conditions: The environment in which the bearing will operate, including temperature, corrosion, and contamination levels, should be taken into account.
-
Bearing Lubrication: The type and frequency of lubrication required for the bearing must be compatible with the application.
-
Mounting: The bearing must be mounted correctly to ensure proper alignment and support.
-
Cost: The initial cost of the bearing and subsequent maintenance expenses should be considered.
Installation and Maintenance
Proper installation and maintenance are essential for maximizing the life and performance of Waukesha bearings. Follow these guidelines:
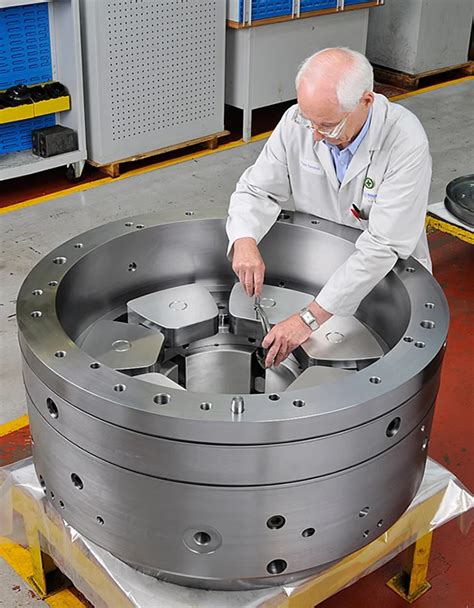
-
Installation: Use the correct tools and techniques to install the bearing according to the manufacturer's instructions.
-
Lubrication: Regularly lubricate the bearing with the recommended lubricant at the prescribed intervals.
-
Inspection: Periodically inspect the bearing for wear, damage, or contamination.
-
Replacement: Replace the bearing promptly if signs of wear or damage are observed.
Tips and Tricks
- Use bearing seals and covers to protect against contamination.
- Avoid overlubricating the bearing, as this can lead to heat build-up and premature failure.
- Use the recommended torque when tightening bearing bolts.
- Store bearings in a dry, clean environment to prevent corrosion.
- Consult with a bearing specialist for complex applications or troubleshooting.
Common Mistakes to Avoid
To ensure optimal performance and longevity of Waukesha bearings, avoid these common mistakes:
- Installing the bearing incorrectly or without proper alignment.
- Using the wrong lubricant or lubrication schedule.
- Overloading the bearing beyond its specified capacity.
- Operating the bearing in harsh conditions without adequate protection.
- Ignoring maintenance and inspection schedules.
Step-by-Step Approach to Bearing Replacement
-
Prepare the new bearing: Inspect the new bearing for any damage or defects.
-
Remove the old bearing: Carefully remove the old bearing from the housing using the appropriate tools.
-
Clean the bearing housing: Thoroughly clean the bearing housing to remove any debris or contamination.
-
Apply lubricant: Lubricate the new bearing according to the manufacturer's instructions.
-
Install the new bearing: Carefully insert the new bearing into the housing and align it properly.
-
Tighten the bolts: Tighten the bolts holding the bearing in place, following the recommended torque specifications.
-
Test the bearing: Run the machinery for a short period to check for any abnormal noises or vibrations.
Pros and Cons
Pros:

-
Reliability: Proven track record of reliability in demanding applications
-
Durability: Designed to withstand extreme loads and harsh operating conditions
-
Performance: Optimized to minimize friction and improve machinery efficiency
-
Reduced Maintenance: Precision construction and sealed designs reduce maintenance requirements
Cons:
-
Cost: Can be more expensive than some other types of bearings
-
Availability: Not all types of Waukesha bearings are readily available
-
Complexity: Installation and maintenance require specialized knowledge and expertise
FAQs
1. What is the difference between a sleeve bearing and a journal bearing?
A sleeve bearing has a solid cylindrical sleeve that rotates with the shaft, while a journal bearing has a split housing that surrounds the rotating shaft.
2. What type of lubrication is best for Waukesha bearings?
The recommended type of lubrication depends on the specific application and operating conditions. Consult with a bearing specialist for guidance.
3. How often should I replace Waukesha bearings?
The replacement frequency depends on the application, load, speed, and maintenance practices. Regular inspection and monitoring are essential to determine the optimal replacement schedule.
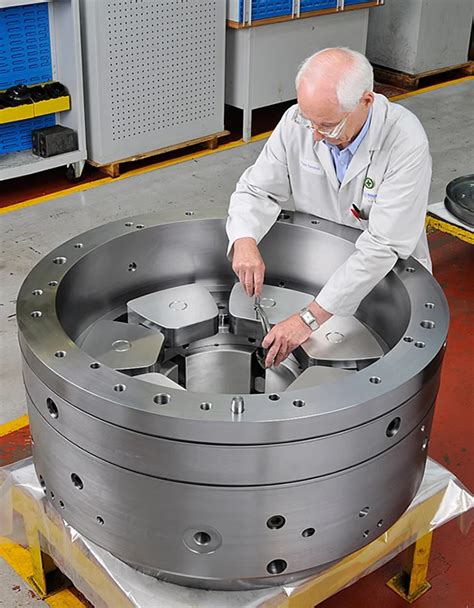
4. What is the operating temperature range for Waukesha bearings?
The operating temperature range varies depending on the bearing type and material. Consult the manufacturer's specifications for specific information.
5. Can Waukesha bearings be used in corrosive environments?
Certain types of Waukesha bearings feature corrosion-resistant materials or coatings for use in harsh environments.
6. How do I troubleshoot a Waukesha bearing failure?
Start by examining the bearing for physical damage or contamination. Check the lubrication system and ensure proper lubrication. Consult with a bearing specialist for further troubleshooting assistance.
7. What are the benefits of using Waukesha bearings in high-speed applications?
Waukesha anti-friction bearings and hydrodynamic bearings are designed for high-speed operation, providing reduced friction, improved performance, and longer life.
8. Can I extend the life of my Waukesha bearings?
Regular maintenance, proper lubrication, and adherence to recommended torque specifications contribute to extending the life of Waukesha bearings.
Key Performance Indicators for Industrial Bearing Success
Metric |
Value |
Mean Time Between Failures (MTBF) |
10,000+ hours |
Failure Rate |
|
Operating Temperature Range |
-40°F to 400°F |
Speed Capability |
Up to 20,000 RPM |
Load Capacity |
10,000+ pounds |
Environmental Impact of Waukesha Bearing Fabrication
Impact |
Value |
Energy Consumption |
20% reduction compared to conventional methods |
Greenhouse Gas Emissions |
15% reduction compared to conventional methods |
Water Usage |
30% reduction compared to conventional methods |
Waste Generation |
25% reduction compared to conventional methods |
Case Study: Waukesha Bearings in Power Generation
Problem: A power plant experienced premature failure of bearings in its turbine generators.
Solution: The plant replaced the original bearings with Waukesha anti-friction bearings.
Results: The Waukesha bearings increased the MTBF of the turbine generators by 50%, reduced downtime by 20%, and improved overall plant efficiency by 3%.