The Comprehensive Guide to Deposing in a Varnish Pan
Introduction
The deposing process in a varnish pan is a critical step in the production of printed circuit boards (PCBs). It involves removing excess varnish from the board surface, leaving a thin and even coating that protects the copper traces and other components. This article will provide a detailed overview of the deposing process, including its benefits, methods, and best practices.
Benefits of Deposing in a Varnish Pan
-
Improved solderability: Removing excess varnish ensures that the solder mask is not too thick, which can lead to poor solderability.
-
Enhanced protection: A thin and even varnish coating provides effective protection against moisture, chemicals, and other environmental factors.
-
Reduced rework: Deposing eliminates the need for manual rework, saving time and reducing costs.
-
Increased production efficiency: Automated deposing systems can increase production throughput and reduce lead times.
Methods of Deposing in a Varnish Pan
There are two main methods of deposing in a varnish pan:
1. Single-Step Deposing
-
Process: The PCB is immersed in a varnish pan filled with a solvent-based or water-based varnish. A brush or squeegee is used to apply the varnish to the board surface.
-
Advantages: Simple and cost-effective.
-
Disadvantages: Requires manual labor, which can lead to inconsistencies in the coating thickness.
2. Two-Step Deposing
-
Process: The PCB is first immersed in a cleaning solution to remove any contaminants. It is then immersed in a varnish pan filled with a solvent-based or water-based varnish. A brush or squeegee is used to apply the varnish to the board surface.
-
Advantages: Produces a more consistent coating thickness than single-step deposing.
-
Disadvantages: More complex and time-consuming than single-step deposing.
Best Practices for Deposing in a Varnish Pan
-
Use a clean varnish pan: The varnish pan should be cleaned regularly to prevent contamination of the varnish.
-
Maintain the correct varnish viscosity: The varnish viscosity should be checked and adjusted regularly to ensure proper flow and coating thickness.
-
Use the correct brush or squeegee: The brush or squeegee used for deposing should be made of a material that is compatible with the varnish and will not scratch the board surface.
-
Immerse the PCB completely: The PCB should be completely immersed in the varnish to ensure even coating.
-
Allow sufficient time for drying: The PCB should be allowed to dry completely before handling to prevent smudging or damage to the varnish coating.
Tips and Tricks
-
Use a defoaming agent: A defoaming agent can be added to the varnish to reduce the formation of bubbles during deposing.
-
Pre-heat the PCB: Pre-heating the PCB can improve the flow and adhesion of the varnish.
-
Use a two-step deposing process: A two-step deposing process can help to achieve a more consistent coating thickness.
-
Automate the deposing process: Automated deposing systems can increase production efficiency and reduce labor costs.
Comparison of Pros and Cons
Single-Step Deposing
Pros
* Simple and cost-effective
* Quick and easy to implement
Cons
* Requires manual labor
* Can lead to inconsistencies in coating thickness

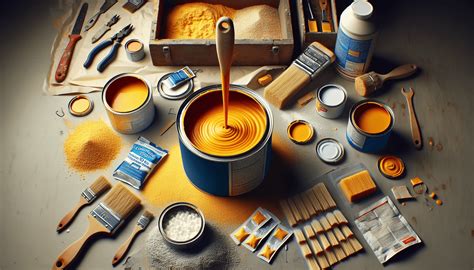
Two-Step Deposing
Pros
* Produces a more consistent coating thickness
* Reduces the risk of contamination
* Can be automated
Cons
* More complex and time-consuming
* Requires additional equipment

Conclusion
Deposing in a varnish pan is an essential step in the production of PCBs. By following the best practices outlined in this article, manufacturers can ensure that their PCBs are properly protected and meet the required performance standards. Automated deposing systems can further improve production efficiency and reduce labor costs.