The Ultimate Guide to Lock Nuts: Ensuring Secure Fastening in Critical Applications
Lock nuts, also known as self-locking nuts, play a vital role in a wide range of industries, including aerospace, automotive, construction, and manufacturing. Their unique designs prevent loosening under extreme vibration, shock, or thermal cycling, ensuring reliable and safe fastening in critical applications.
Understanding Lock Nuts
Lock nuts are typically hexagonal in shape and feature a variety of locking mechanisms, such as:
-
Nylon Inserts: A synthetic nylon insert is molded into the nut, creating friction against the bolt threads to prevent rotation.
-
Split Thread: The nut is split in the middle, creating two independent threads that clamp onto the bolt under tightening.
-
Deformed Threads: The threads are deformed during manufacturing, ensuring a tight fit and preventing loosening.
Types of Lock Nuts
Various types of lock nuts are available to meet specific application requirements:
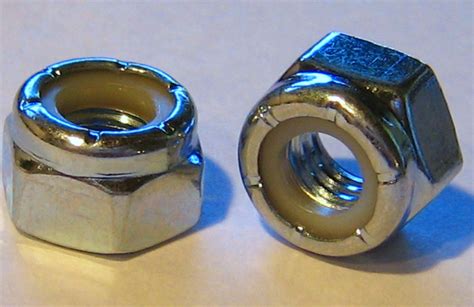
-
Full Metal Lock Nuts: These nuts are made entirely of metal and provide maximum locking torque.
-
Prevailing Torque Lock Nuts: These nuts offer a moderate locking torque and are suitable for applications with limited tightening capabilities.
-
Slotted Lock Nuts: These nuts feature a slotted design that allows for thread lubrication during assembly.
Benefits of Using Lock Nuts
Incorporating lock nuts into your fastening applications offers numerous benefits, including:
-
Enhanced Safety: Lock nuts prevent bolts from loosening, reducing the risk of catastrophic failures and enhancing overall system safety.
-
Increased Reliability: By eliminating the possibility of unintentional loosening, lock nuts ensure the integrity and performance of bolted joints over time.
-
Cost Savings: Avoiding failures and rework associated with loose bolts can save significant costs in maintenance and downtime.
-
Simplified Assembly: Lock nuts simplify assembly by eliminating the need for additional locking devices such as washers or thread adhesives.
Applications of Lock Nuts
Lock nuts find applications in a wide variety of industries, including:
-
Aerospace: Securing critical components in aircraft engines, landing gear, and flight control systems.
-
Automotive: Fastening brake calipers, steering components, and suspension systems.
-
Construction: Connecting structural members in bridges, buildings, and other heavy-duty structures.
-
Manufacturing: Assembling heavy machinery, equipment, and industrial systems.
Common Mistakes to Avoid
When using lock nuts, it is crucial to avoid common mistakes that can compromise their effectiveness:
-
Overtightening: Excessive tightening can damage the locking mechanism and reduce its integrity.
-
Insufficient Tightening: Loosely tightened lock nuts may not provide adequate locking force and can result in relaxation.
-
Lubrication: Avoid lubricating the threads of lock nuts, as this can reduce their locking capabilities.
-
Reusing Lock Nuts: Single-use lock nuts should not be reused, as they may have lost their locking properties after initial use.
Effective Strategies for Using Lock Nuts
To maximize the effectiveness of lock nuts, consider the following strategies:
-
Proper Selection: Identify the appropriate type and size of lock nut for the specific application.
-
Correct Tightening: Use a torque wrench to apply the recommended tightening torque specified for the lock nut.
-
Regular Inspection: Regularly inspect bolted joints using lock nuts to ensure they remain tight and secure.
-
Maintenance: Replace worn or damaged lock nuts to maintain proper fastening and integrity.
Tips and Tricks for Successful Lock Nut Applications
- Use double lock nuts in high-vibration environments for added security.
- Consider using lock nuts with a nylon insert to prevent galvanic corrosion between dissimilar metals.
- If tightening the lock nut is difficult, try pre-lubricating the bolt threads with anti-seize compound.
- Secure the threads of lock nuts with thread-locking adhesive in extreme applications.
Conclusion
Lock nuts are essential components in demanding applications where secure and reliable fastening is critical. By understanding the types, benefits, and proper use of lock nuts, engineers and technicians can ensure the integrity and performance of their bolted joints. By avoiding common mistakes and implementing effective strategies, lock nuts can provide unwavering safety, reliability, and cost-effectiveness.

Tables
Table 1: Common Lock Nut Types and Features
Type |
Locking Mechanism |
Material |
Tensile Strength (Mpa) |
Nylon Insert |
Nylon insert |
Steel, Stainless Steel |
414-1200 |
Split Thread |
Split threads |
Steel, Stainless Steel |
660-1480 |
Deformed Threads |
Deformed threads |
Steel, Stainless Steel |
750-1760 |
Table 2: Lock Nut Applications in Various Industries
Industry |
Application |
Aerospace |
Aircraft engines, landing gear, flight control systems |
Automotive |
Brake calipers, steering components, suspension systems |
Construction |
Structural members, bridges, buildings |
Manufacturing |
Heavy machinery, equipment, industrial systems |
Table 3: Common Mistakes to Avoid When Using Lock Nuts
Mistake |
Consequence |
Overtightening |
Damaged locking mechanism, reduced effectiveness |
Insufficient Tightening |
Loosely tightened joints, risk of loosening |
Lubricating Threads |
Reduced locking capabilities |
Reusing Lock Nuts |
Loss of locking properties, compromised safety |