The Comprehensive Guide to Tapered Roller Bearings: Unlocking Performance and Longevity in Critical Applications
Introduction:
Tapered roller bearings are indispensable components in a wide range of industrial machinery and engineering applications, renowned for their ability to withstand heavy axial and radial loads while delivering exceptional performance and durability. This comprehensive guide delves into the intricate world of tapered roller bearings, exploring their design principles, key characteristics, and the various applications where they excel.

Design and Principles of Tapered Roller Bearings
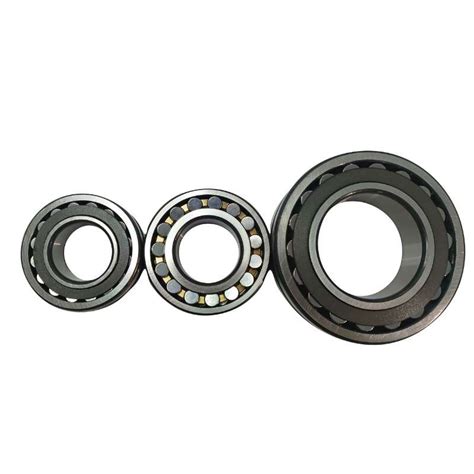
Tapered roller bearings are distinguished by their unique design, featuring conical rollers that are positioned between two tapered raceways. The cone angle of the rollers and raceways is typically between 10 and 15 degrees, enabling the bearing to accommodate both axial and radial loads.

Key Characteristics:
-
High Load Capacity: Tapered roller bearings are renowned for their exceptional load-carrying capacity, making them ideal for applications involving heavy loads and demanding operating conditions.
-
Axial and Radial Loads: These bearings can simultaneously handle both axial and radial loads, eliminating the need for separate thrust bearings and simplifying system design.
-
Self-Aligning Capability: Tapered roller bearings possess a self-aligning feature, allowing for minor misalignments between the shaft and housing, which is particularly beneficial in applications where precision alignment is challenging.
-
Durability: The conical rollers and tapered raceways distribute loads over a larger contact area, resulting in reduced stress and enhanced durability compared to other bearing types.
Applications of Tapered Roller Bearings
Tapered roller bearings find widespread application in various industries due to their exceptional performance characteristics. Some prominent examples include:
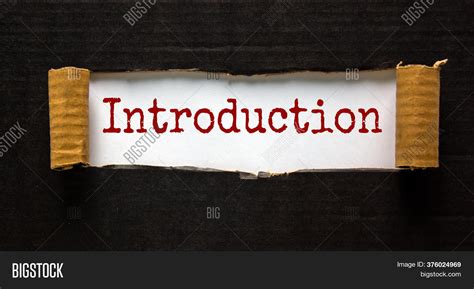
- Automotive (transmissions, differentials, wheel bearings)
- Construction machinery (cranes, excavators, bulldozers)
- Industrial machinery (gearboxes, rolling mills, crushers)
- Aerospace (engine mounts, landing gear)
- Power generation (turbines, generators)
Types of Tapered Roller Bearings
There are two primary types of tapered roller bearings based on their design:
-
Single-Row Tapered Roller Bearings: These bearings consist of a single row of conical rollers positioned between two tapered raceways. They are commonly used in applications where axial loads are minimal.
-
Double-Row Tapered Roller Bearings: As the name suggests, double-row tapered roller bearings feature two rows of conical rollers arranged back-to-back. They offer superior axial load-carrying capacity compared to single-row bearings.
Selection Criteria for Tapered Roller Bearings
When selecting a tapered roller bearing, several key factors should be considered:
-
Load Capacity: The bearing should have sufficient load-carrying capacity to withstand the expected axial and radial loads in the application.
-
Speed: The maximum operating speed of the bearing must be compatible with the rotational speeds encountered in the application.
-
Lubrication: The bearing should be compatible with the available lubrication system and operating environment.
-
Environmental Conditions: The bearing should be suitable for the environmental conditions, such as temperature, humidity, and exposure to contaminants.
Maintenance and Lubrication of Tapered Roller Bearings
To ensure optimal performance and longevity, tapered roller bearings require regular maintenance and lubrication. Some key practices include:
-
Inspection and Cleaning: Periodically inspect the bearing for wear, damage, or contamination. Clean the bearing and surrounding components as needed.
-
Lubrication: Use the correct lubricant type and quantity as recommended by the bearing manufacturer. Proper lubrication reduces friction and wear, extending bearing life.
-
Retightening: Monitor bearing adjustment and retighten as necessary to maintain proper clearance and prevent excessive play.
Advantages of Tapered Roller Bearings
-
High Load Capacity: Exceptional load-carrying capacity for handling heavy axial and radial loads.
-
Compact Design: Relatively compact design compared to other bearing types with similar load capacity.
-
Self-Aligning: Ability to accommodate minor misalignments, simplifying installation and reducing stress on other components.
-
Durability: Long operating life under demanding conditions due to the large contact area and reduced stress.
-
Versatility: Suitable for a wide range of applications, from automotive to industrial machinery.
Disadvantages of Tapered Roller Bearings
-
Sensitivity to Contamination: Contamination can affect bearing performance and reduce its life.
-
Higher Noise Levels: Tapered roller bearings can produce slightly higher noise levels compared to some other bearing types.
-
Mounting Precision: Precise mounting is crucial to ensure proper bearing function and longevity.
Tips and Tricks for Using Tapered Roller Bearings
- Use a mounting tool or arbor press to properly install the bearing.
- Ensure proper lubrication and follow the manufacturer's recommendations.
- Monitor bearing temperatures during operation to detect any potential issues.
- Regularly inspect the bearing and surrounding components for wear or damage.
- Store bearings in a clean and dry environment to prevent corrosion.
How to Step-by-Step Install a Tapered Roller Bearing:
-
Prepare the Shaft and Housing: Clean the shaft and housing surfaces. Apply a thin layer of sealant or anti-seize compound to the shaft.
-
Position the Inner Race: Place the inner race on the shaft and slide it into the housing bore. Use a mounting sleeve or arbor press to ensure proper seating.
-
Mount the Outer Race: Position the outer race in the housing and apply pressure to seat it. Use a mounting sleeve or arbor press to avoid damaging the bearing.
-
Set the Bearing Clearance: Follow the manufacturer's instructions to adjust the bearing clearance using shims or a preload nut.
-
Lubricate the Bearing: Fill the bearing cavity with the recommended lubricant.
-
Finalize Installation: Secure the bearing using the appropriate locking device, such as a retaining nut or split collar.
Tables for Reference
Table 1: Typical Dimensions and Ratings of Single-Row Tapered Roller Bearings
Bore Diameter (mm) |
Outside Diameter (mm) |
Width (mm) |
Dynamic Load Rating (kN) |
20 |
47 |
14 |
16.5 |
30 |
72 |
19 |
34.5 |
40 |
95 |
22 |
62.4 |
50 |
120 |
26 |
97.5 |
60 |
142 |
30 |
141.3 |
Table 2: Typical Dimensions and Ratings of Double-Row Tapered Roller Bearings
Bore Diameter (mm) |
Outside Diameter (mm) |
Width (mm) |
Dynamic Load Rating (kN) |
20 |
62 |
20 |
36.4 |
30 |
94 |
26 |
77.2 |
40 |
124 |
32 |
128.7 |
50 |
154 |
38 |
193.9 |
60 |
182 |
42 |
274.5 |
Table 3: Lubrication Recommendations for Tapered Roller Bearings
Operating Temperature (°C) |
Lubricant Type |
Below -30 |
Synthetic Oil |
-30 to 120 |
Mineral Oil |
Above 120 |
High-Temperature Grease |
Call to Action
Tapered roller bearings play a crucial role in various industrial applications, offering exceptional performance and durability under demanding conditions. By understanding the principles of their design, selecting the appropriate type, and implementing proper maintenance practices, you can optimize the performance and longevity of these critical components.