A Comprehensive Guide to Die Grinding Slots: Techniques, Benefits, and Best Practices
Die grinding is an essential process in the manufacturing industry, used to create slots and other geometric features on metal dies. The accuracy and efficiency of die grinding slots are crucial for the quality and performance of the final product. This detailed guide will provide an extensive overview of die grinding slots, including the different techniques, equipment, and best practices involved.
Understanding Die Grinding Slots
Die grinding slots are narrow cuts or grooves machined into metal dies using specialized grinding tools. They are commonly used for:
-
Molding: Creating slots for plastic or metal parts, such as injection molding tools
-
Stamping: Producing slots in sheet metal for various components
-
Machining: Removing excess material or creating specific geometries in dies
-
Deburring: Removing sharp edges and burrs left behind from other machining processes
Techniques for Die Grinding Slots
There are several techniques employed for die grinding slots, each with its own advantages and applications:
1. Conventional Die Grinding
- Uses a rotating grinding wheel to remove material by abrasion
- Requires highly skilled operators to achieve precise dimensions
- Suitable for small-scale or low-volume production
2. EDM Die Grinding
- Electrodes & diluted water are used to cut slots through a process called sparking
- No direct contact between electrode and workpiece, preventing distortion
- Provides high precision and complex geometry capability
- Expensive and time-consuming process
3. Laser Die Grinding
- Uses a focused laser beam to melt and vaporize material
- Non-contact machining eliminates tool wear and distortion
- Fast and accurate, but can be more expensive for smaller slots
Equipment for Die Grinding Slots
The appropriate equipment for die grinding slots depends on the technique and material being machined:

Technique |
Equipment |
Key Features |
Conventional Die Grinding |
CNC grinding machine, grinding wheel |
Precision control, wide range of grinding wheel options |
EDM Die Grinding |
EDM machine, electrodes |
Non-contact machining, high precision |
Laser Die Grinding |
Laser machine, optics |
Fast, accurate, suitable for complex geometries |
Benefits of Die Grinding Slots
Die grinding slots offer several advantages in the manufacturing process:
-
Improved Part Quality: Precise slots ensure proper fit, function, and durability of molded or stamped parts.
-
Enhanced Performance: Smooth and burr-free slots minimize friction and wear, increasing the efficiency of the die.
-
Cost Savings: Accurate slots reduce scrap and rework, resulting in lower production costs.
-
Increased Productivity: Automated grinding and laser machining techniques allow for faster production times.
-
Design Flexibility: Die grinding allows for customization and modification of slots to meet specific requirements.
Best Practices for Die Grinding Slots
To achieve optimal results, it is essential to follow best practices for die grinding slots:


-
Choose the Right Technique: Select the appropriate grinding technique based on the size, complexity, and material of the slot.
-
Use High-Quality Equipment: Invest in well-maintained grinding machines and tools to ensure precision and accuracy.
-
Proper Workholding: Secure the die firmly to prevent movement and maintain dimensional accuracy.
-
Optimize Grinding Parameters: Determine the ideal grinding wheel speed, feed rate, and depth of cut for efficient material removal.
-
Regular Tool Maintenance: Inspect and sharpen grinding tools regularly to maintain performance and extend their lifespan.
Common Mistakes to Avoid
Avoiding common mistakes can significantly improve the efficiency and quality of die grinding slots:
-
Incorrect Slot Design: Inadequate slot dimensions or poor corner radii can lead to part failure.
-
Excessive Material Removal: Grinding too deep can weaken the die and compromise its structural integrity.
-
Poor Surface Finish: Rough or uneven surfaces can increase friction and wear on the die and molded parts.
-
Lack of Proper Cooling: Insufficient cooling during grinding can generate excessive heat, leading to distortion or burning of the die.
-
Improper Tool Selection: Using the wrong grinding wheel or tool material can result in poor machining performance or damage to the die.
A Step-by-Step Approach to Die Grinding Slots
Follow these steps to ensure a successful die grinding process:
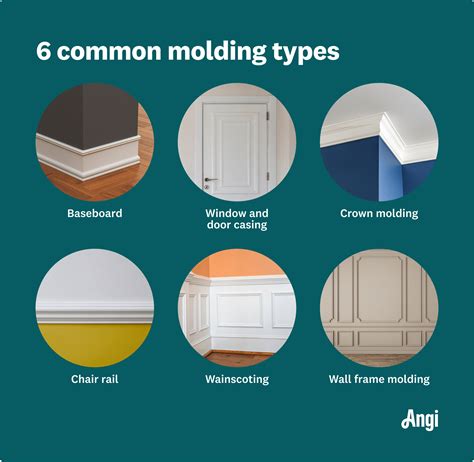
-
Plan and Design: Determine slot specifications, material properties, and grinding techniques.
-
Material Preparation: Prepare the die surface by cleaning and ensuring proper workholding.
-
Tool Selection: Choose the appropriate grinding tool based on the desired slot size and shape.
-
Parameter Optimization: Set the optimal grinding parameters (speed, feed, depth) for efficient material removal.
-
Grinding Process: Execute the grinding operation, monitoring the process carefully.
-
Quality Inspection: Verify the slot dimensions, surface finish, and overall quality to meet specifications.
-
Post-Processing: Perform any necessary post-processing, such as deburring or surface treatment.
Stories and Lessons Learned
Case Study 1:
A metal stamping manufacturer faced challenges with burred and uneven slots, leading to faulty parts and increased scrap. By implementing a laser die grinding technique, they significantly improved slot quality, reduced scrap by 25%, and increased production efficiency.
Lesson Learned: Laser die grinding can provide high-precision, burr-free slots, resulting in reduced scrap and improved part quality.
Case Study 2:
A plastic injection molding company struggled to maintain consistent slot dimensions due to variations in conventional die grinding. By switching to EDM die grinding, they achieved micron-level precision and reduced rejects by 40%.
Lesson Learned: EDM die grinding offers exceptional precision for critical slot dimensions, ensuring consistency and reducing part failures.
Case Study 3:
A die manufacturer experienced excessive tool wear during conventional die grinding, resulting in increased downtime and maintenance costs. By optimizing grinding parameters and implementing proper tool maintenance, they extended tool life by 30% and reduced downtime.
Lesson Learned: Proper parameter optimization and regular tool maintenance are crucial for reducing tool wear, lowering maintenance costs, and increasing productivity.
Effective Strategies for Die Grinding Slots
Optimization Techniques:
- Use computer-aided design (CAD) software for precise slot design and simulation.
- Implement grinding parameter optimization tools to determine the most efficient settings.
- Employ adaptive control systems to adjust grinding parameters based on workpiece conditions.
- Utilize multi-axis grinding for complex geometries and improved accuracy.
Advanced Tooling Solutions:
- Invest in high-performance grinding wheels and cutting tools for enhanced efficiency and durability.
- Use specialized tooling for specific materials or slot configurations.
- Explore the latest abrasive technologies, such as superabrasives and diamond wheels, for improved performance.
Process Automation and Control:
- Automate the grinding process using CNC or robotic systems to reduce errors and increase consistency.
- Implement closed-loop control systems to monitor and adjust grinding parameters in real-time.
- Use vision inspection or laser scanning systems to ensure slot quality and dimensional accuracy.
Conclusion
Die grinding slots is a critical process in the manufacturing industry, requiring precision, accuracy, and efficiency. By understanding the different techniques, equipment, and best practices involved, manufacturers can optimize their die grinding processes to achieve high-quality slots and enhance the performance of their products. Implementing effective strategies, such as optimization techniques, advanced tooling solutions, and process automation, can further improve productivity, reduce costs, and ensure the highest levels of quality and precision.