SFR3: The Ultimate Guide to Subfloor Radio Frequency Identification (RFID) Technology in Warehousing and Logistics
Introduction
Subfloor Radio Frequency Identification (RFID), or SFR3, is a cutting-edge technology that revolutionizes warehouse and logistics operations by providing real-time visibility and tracking of inventory and assets. This article serves as a comprehensive guide to SFR3, empowering readers with an in-depth understanding of its benefits, implementation, and best practices.
Defining SFR3
SFR3 is an RFID-based technology that utilizes radio waves to identify and track items. It employs a network of antennas installed beneath the floor of a warehouse or logistics center. These antennas transmit and receive signals, allowing the system to detect and locate tagged items anywhere within the facility.
SFR3 offers several key advantages:
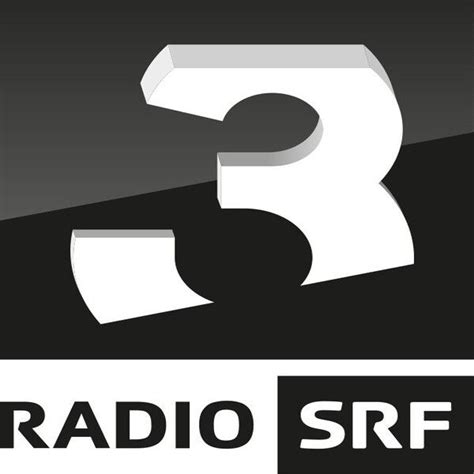
-
Real-time visibility: Provides constant monitoring of inventory levels, location, and movement.
-
Accurate tracking: Ensures precise identification and tracking of individual items, eliminating errors.
-
Improved efficiency: Streamlines processes by eliminating manual counting and tracking, saving time and labor.
-
Increased accuracy: Reduces errors caused by human input, providing highly accurate data.
-
Enhanced security: Tracks items throughout the facility, preventing theft and unauthorized access.
Benefits of SFR3
The implementation of SFR3 in warehouses and logistics centers brings numerous benefits, including:
-
Increased Inventory Accuracy: SFR3 provides real-time inventory updates, eliminating discrepancies and ensuring accurate stock levels.
-
Enhanced Productivity: Automates inventory tracking processes, freeing up staff for more value-added tasks.
-
Reduced Labor Costs: Eliminates the need for manual counting and scanning, reducing labor expenses significantly.
-
Optimized Space Utilization: Provides precise inventory location data, allowing for efficient space planning and optimization.
-
Improved Customer Service: Enables faster processing of orders and real-time updates on order status, enhancing customer satisfaction.
Applications of SFR3
SFR3 has a wide range of applications in various industries, including:
-
Warehousing: Real-time inventory tracking, cycle counting, and efficient putaway processes.
-
Logistics: Tracking of pallets, containers, and other assets throughout the supply chain.
-
Manufacturing: Inventory management, work-in-progress tracking, and finished goods tracking.
-
Healthcare: Accurate tracking of medical supplies, equipment, and patient records.
-
Retail: Inventory management, shrinkage control, and efficient checkout processes.
How SFR3 Works
SFR3 operates on a combination of hardware and software components:
%20Technology%20in%20Warehousing%20and%20Logistics)

Hardware:
-
Antennas: Installed beneath the floor to transmit and receive RFID signals.
-
Tags: Attached to items to be tracked, containing unique identifiers.
-
Readers: Interrogate tags and transmit data to the software system.
Software:
%20Technology%20in%20Warehousing%20and%20Logistics)
-
Management Software: Manages the RFID system, processes data, and provides visibility and tracking capabilities.
-
Database: Stores and organizes collected data for analysis and reporting.
Tagging Strategies
SFR3 requires the tagging of items to be tracked. Different tagging strategies are available:
-
Item-level tagging: Each individual item is assigned a unique tag.
-
Batch-level tagging: Items are tagged in groups or batches.
-
Pallet-level tagging: Tags are attached to pallets containing multiple items.
Implementing SFR3
The implementation of SFR3 involves several key steps:
-
Planning: Define the scope, objectives, and requirements of the SFR3 system.
-
Infrastructure Design: Determine the optimal antenna layout and tag strategy for the facility.
-
Hardware Selection: Choose appropriate antennas, readers, and tags based on the specific requirements.
-
Software Configuration: Install and configure the management software to meet the business needs.
-
Testing and Validation: Thoroughly test the system to ensure accuracy and reliability.
-
Training and Deployment: Train staff on the use and maintenance of the SFR3 system.
Best Practices for SFR3 Deployment
-
Proper Antenna Placement: Optimize antenna layout to ensure complete coverage and minimize interference.
-
Accurate Tagging: Ensure proper attachment and orientation of tags to maximize readability.
-
Data Management: Establish clear guidelines for data collection, storage, and analysis.
-
Continuous System Monitoring: Track system performance and address any issues promptly.
-
Regular Maintenance: Perform regular maintenance and calibration of the hardware components.
Case Studies
Case Study 1:
A large warehouse implemented SFR3 to improve inventory accuracy. The system reduced inventory discrepancies by 85%.
Case Study 2:
A logistics company deployed SFR3 to track pallets throughout the supply chain. This resulted in a 20% increase in asset utilization.
Case Study 3:
A manufacturing facility used SFR3 to monitor work-in-progress. This led to a 15% reduction in cycle times.
Lessons Learned
These case studies highlight the significant benefits of SFR3 implementation:
-
Improved data accuracy: Reduces errors and provides a more accurate representation of inventory levels.
-
Increased efficiency: Automates processes, reduces manual labor, and streamlines operations.
-
Enhanced visibility: Provides real-time tracking and visibility of inventory and assets.
Common Mistakes to Avoid
-
Poor Antenna Placement: Insufficient or inadequate antenna coverage can lead to inaccurate tracking.
-
Inconsistent Tagging: Variations in tag placement or orientation can affect readability and tracking accuracy.
-
Insufficient Training: Untrained staff may not fully utilize the capabilities of the SFR3 system.
-
Lack of Continuous Monitoring: Failing to monitor system performance can lead to undetected issues and data inaccuracies.
-
Neglecting Maintenance: Proper maintenance is crucial for system reliability and accuracy.
Step-by-Step Approach to Deploying SFR3
-
Assessment: Conduct a thorough assessment of current inventory management processes and challenges.
-
Planning: Define the scope, objectives, and requirements of the SFR3 system.
-
Design: Determine the optimal antenna layout, tag strategy, and software configuration.
-
Implementation: Install hardware, configure software, and train staff.
-
Testing: Test and validate the system to ensure accuracy and reliability.
-
Deployment: Roll out the system across the facility and monitor performance.
-
Continuous Improvement: Regularly review and optimize the system to enhance its effectiveness.
Call to Action
Deploying SFR3 in warehouses and logistics centers offers numerous benefits, including increased inventory accuracy, enhanced efficiency, reduced costs, and improved customer service. Organizations seeking to optimize their operations and gain a competitive advantage should consider the implementation of this transformative technology.
Additional Tables and Resources
Table 1: Benefits of SFR3 in Different Industries
Industry |
Key Benefits |
Warehousing |
Real-time inventory tracking, improved space utilization, reduced inventory discrepancies |
Logistics |
Enhanced asset tracking, increased supply chain visibility, optimized transportation efficiency |
Manufacturing |
Accurate work-in-progress tracking, reduced cycle times, improved quality control |
Healthcare |
Efficient medical supply management, patient record tracking, enhanced patient safety |
Retail |
Optimized inventory management, reduced shrinkage, improved checkout processes |
Table 2: Best Practices for SFR3 Implementation
Practice |
Description |
Proper Antenna Placement |
Optimize antenna layout to ensure complete coverage and minimize interference |
Accurate Tagging |
Ensure proper attachment and orientation of tags to maximize readability |
Data Management |
Establish clear guidelines for data collection, storage, and analysis |
Continuous System Monitoring |
Track system performance and address any issues promptly |
Regular Maintenance |
Perform regular maintenance and calibration of the hardware components |
Table 3: Common Mistakes to Avoid in SFR3 Deployment
Mistake |
Impact |
Poor Antenna Placement |
Inaccurate tracking and reduced system effectiveness |
Inconsistent Tagging |
Difficulties in tag readability and tracking accuracy |
Insufficient Training |
Limited understanding and utilization of the SFR3 system |
Lack of Continuous Monitoring |
Undetected issues and data inaccuracies |
Neg |
|