The Comprehensive Guide to Spherical Bushings: A Vital Component for Precision Motion Control
Introduction
Spherical bushings, also known as self-aligning bearings, are indispensable mechanical components that play a pivotal role in facilitating smooth and precise motion control in various industrial and engineering applications. Their unique design and exceptional performance characteristics make them an essential element in achieving optimal efficiency and reliability in demanding operational environments.
Understanding the Design and Function of a Spherical Bushing
A typical spherical bushing comprises two primary components:
-
Inner Ring: This is the spherical inner part that accommodates the shaft. It possesses a precision-ground spherical surface that ensures precise alignment and rotation with the shaft.
-
Outer Ring: The outer ring is the housing that encloses the inner ring and the shaft. It features a spherical concave surface that matches the spherical surface of the inner ring, allowing for self-alignment and angular misalignment.
The spherical geometry of the bushing allows for axial displacement and angular misalignment between the shaft and the housing. This unique feature accommodates shaft imperfections, misalignment due to mounting tolerances, and thermal expansion or contraction, ensuring smooth and uninterrupted motion.
Key Performance Characteristics of Spherical Bushings
Spherical bushings offer a range of exceptional performance attributes that make them suitable for diverse applications:

-
Self-Alignment: The spherical design enables self-alignment, compensating for misalignment and ensuring proper load distribution and extended bearing life.
-
Low Friction: The sliding contact between the spherical surfaces minimizes friction, reducing power consumption and maximizing efficiency.
-
High Load Capacity: Spherical bushings can withstand significant radial, axial, and moment loads, making them suitable for applications with demanding load requirements.
-
Long Service Life: The durable construction of spherical bushings and the minimal wear associated with their sliding contact contribute to their extended service life.
-
Corrosion Resistance: Stainless steel or corrosion-resistant materials are often used in the construction of spherical bushings, enhancing their resistance to environmental factors and prolonging their lifespan.
Types of Spherical Bushings
Spherical bushings are categorized into different types based on their design and functional characteristics:
-
Standard Spherical Bushings: These are the most common type and offer a wide range of load capacities and mounting options.
-
Flanged Spherical Bushings: Flanged bushings feature an additional flange that allows for secure mounting and prevents axial displacement.
-
Rod End Spherical Bushings: These bushings have a threaded stud instead of a housing, providing versatility and ease of installation.
-
Self-Lubricating Spherical Bushings: These bushings incorporate a built-in lubricant to minimize maintenance requirements and extend their service life.
Applications of Spherical Bushings
Spherical bushings find extensive use in a multitude of industrial and engineering applications, including:
-
Industrial Machinery: They are employed in conveyors, gearboxes, and printing presses to facilitate precise motion control and accommodate misalignment.
-
Aerospace and Defense: Spherical bushings play a critical role in aircraft control systems, instrument panels, and defense equipment.
-
Robotics and Automation: They enable smooth and accurate motion in robots, automated assembly lines, and medical equipment.
-
Medical Equipment: Surgical instruments, prosthetics, and MRI scanners utilize spherical bushings for precise positioning and alignment.
-
Transportation: Spherical bushings are used in automotive suspensions, steering systems, and aircraft landing gear to accommodate misalignment and reduce friction.
Benefits of Using Spherical Bushings
The incorporation of spherical bushings in various applications offers numerous benefits:
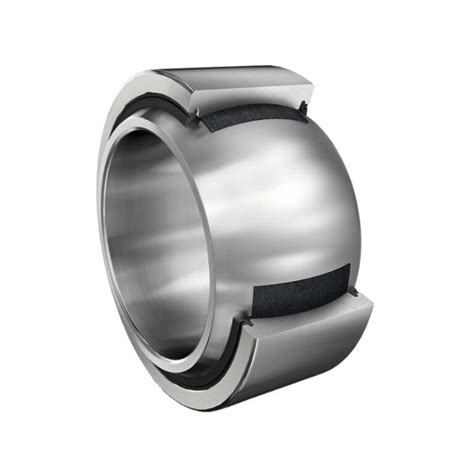
-
Improved Precision: The self-aligning capability of spherical bushings eliminates misalignment and ensures precise motion control, reducing vibrations and improving overall performance.
-
Reduced Maintenance: The low friction and wear associated with spherical bushings significantly reduce maintenance requirements, saving both time and resources.
-
Extended Service Life: The durable construction and minimal wear of spherical bushings contribute to their extended lifespan, reducing downtime and replacement costs.
-
Enhanced Reliability: The precise alignment and reduced friction result in increased reliability, minimizing the risk of equipment failure and costly repairs.
Effective Strategies for Selecting Spherical Bushings
Choosing the appropriate spherical bushing for your application involves careful consideration of the following factors:
-
Load Capacity: Determine the maximum radial, axial, and moment loads that the bushing will be subjected to during operation.
-
Size and Space Constraints: Ensure that the size of the bushing aligns with the available space and mounting configuration.
-
Operating Temperature: Consider the temperature range in which the bushing will be used to ensure compatibility with its material properties.
-
Corrosion Resistance: Select bushings made of materials that are resistant to the environmental conditions encountered in your application.
-
Maintenance Requirements: Choose bushings with built-in lubrication or consider ease of maintenance for regular lubrication.
Tips and Tricks for Using Spherical Bushings
To maximize the performance and lifespan of spherical bushings, follow these tips:
-
Proper Installation: Ensure precise mounting and alignment of the bushing and shaft to minimize misalignment and premature wear.
-
Regular Lubrication: Lubricate bushings regularly according to the manufacturer's recommendations to reduce friction and extend their service life.
-
Inspect Regularly: Conduct periodic inspections to check for any signs of wear, damage, or misalignment that may require attention.
-
Handle with Care: Handle spherical bushings with care to avoid damage to their precision surfaces or seals.
-
Store Properly: Store bushings in a clean and dry environment to prevent corrosion or contamination.
Pros and Cons of Spherical Bushings
Pros:
- Self-aligning to compensate for misalignment
- Low friction for increased efficiency
- High load capacity to withstand demanding loads
- Long service life due to minimal wear
- Corrosion-resistant materials for durability
Cons:

- Higher cost compared to traditional bearings
- Limited speed capabilities in certain applications
- May require regular lubrication to maintain optimal performance
- Can be susceptible to brinelling damage if subjected to excessive impact loads
Call to Action
If you seek precision motion control and long-lasting performance in your industrial or engineering applications, spherical bushings are an excellent choice. Consider the factors and strategies outlined in this comprehensive guide to select the most suitable bushings for your specific requirements. By implementing the tips and tricks provided, you can maximize the benefits and ensure optimal operation of your equipment. For expert guidance and support in choosing and using spherical bushings, consult with a reputable manufacturer or distributor.