Silicone Lubricants: A Comprehensive Guide for Enhanced Performance
As technology advances at an unprecedented pace, silicone has become an indispensable component in various industries due to its exceptional properties. Its versatility extends from automotive parts to medical devices, making it a material of choice for diverse applications. However, to ensure the optimal performance and longevity of silicone components, the use of specialized lubricants is paramount.
This comprehensive guide will delve into the world of silicone lubricants, exploring their significance, benefits, and applications. We will provide a detailed overview of different types of lubricants, their properties, and their impact on silicone surfaces. Additionally, we will offer practical tips and tricks for selecting and using lubricants to maximize the performance and durability of your silicone components.
Understanding Silicone Lubricants
Silicone lubricants are specially formulated to provide lubrication between silicone surfaces, reducing friction and wear. They are typically composed of a base oil, such as polydimethylsiloxane (PDMS), and additives that enhance their performance characteristics.
Compared to conventional lubricants, silicone lubricants offer several significant advantages:

-
Excellent Thermal Stability: Silicone lubricants exhibit exceptional resistance to extreme temperatures, maintaining their properties over a wide range of operating conditions.
-
Chemical Inertness: They are highly resistant to chemical degradation, making them ideal for use in corrosive environments.
-
Non-Toxic and Biocompatible: Silicone lubricants are typically non-toxic and biocompatible, making them suitable for applications involving human contact.
-
Low Coefficient of Friction: They significantly reduce friction between silicone surfaces, minimizing wear and prolonging component life.
-
Water Repellency: Silicone lubricants are hydrophobic, repelling water and protecting silicone components from moisture-related damage.
Types of Silicone Lubricants
There are various types of silicone lubricants available, each tailored to specific applications and performance requirements. Common types include:
Type |
Properties |
Applications |
PDMS-Based Lubricants: General-purpose lubricants with good thermal stability, low friction, and chemical inertness. Ideal for O-rings, seals, and gaskets. |
|
|
Fluorinated Silicone Lubricants: Enhanced thermal and chemical resistance, suitable for extreme conditions. Used in high-temperature applications, bearings, and aerospace components. |
|
|
Greases: High-viscosity lubricants that provide long-term lubrication. Suitable for gears, bearings, and other moving parts. |
|
|
Sprays: Convenient and easy-to-apply lubricants for quick lubrication of surfaces. Ideal for maintenance and repair work. |
|
|
Dry Film Lubricants: Thin, solid films that reduce friction and wear without leaving a residue. Used in cleanroom environments and applications where contamination is a concern. |
|
|
Benefits of Using Silicone Lubricants
Incorporating silicone lubricants into your silicone maintenance routine offers numerous benefits that can enhance the performance and longevity of your components:
-
Reduced Friction and Wear: Silicone lubricants effectively reduce friction between silicone surfaces, preventing premature wear and extending component life.
-
Improved Performance: Lubricated silicone components operate more smoothly, reducing energy consumption and improving efficiency.
-
Corrosion Protection: Silicone lubricants act as a barrier, protecting silicone surfaces from corrosion and degradation caused by environmental factors.
-
Reduced Maintenance: Regular lubrication helps minimize friction and wear, reducing the frequency and cost of maintenance.
-
Extended Component Life: By protecting silicone components from friction, wear, and corrosion, silicone lubricants can significantly extend their lifespan.
Applications of Silicone Lubricants
Silicone lubricants have a wide range of applications across various industries and sectors:
-
Automotive: O-rings, seals, gaskets, bearings, and other components in engines, transmissions, and brake systems.
-
Medical: Surgical instruments, catheters, implants, and other medical devices that require biocompatibility.
-
Aerospace: Bearings, seals, and other components in aircraft and spacecraft that endure extreme operating conditions.
-
Electronics: Connectors, switches, and other electrical components to reduce friction and improve reliability.
-
Industrial: O-rings, seals, bearings, and other components in machinery, pumps, and valves.
-
Consumer Products: Lubrication of household appliances, toys, and sporting goods for increased performance and durability.
How to Select and Use Silicone Lubricants
Choosing the right silicone lubricant for your application is crucial to maximizing its benefits. Consider the following factors when selecting a lubricant:
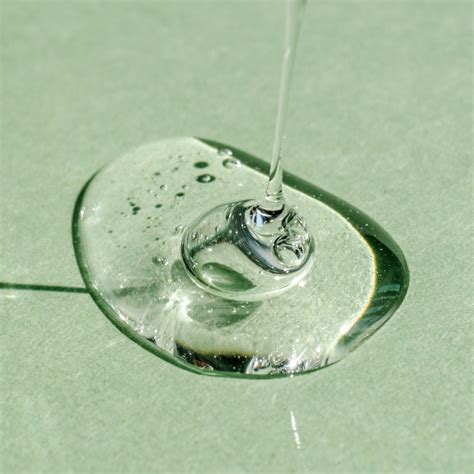
-
Application Environment: Temperature range, exposure to chemicals, moisture, and other environmental factors.
-
Component Type: O-ring, seal, gasket, bearing, or other component being lubricated.
-
Desired Properties: High thermal stability, chemical resistance, low friction, or other specific performance characteristics.
-
Application Method: Spray, grease, or thin film for ease of application and desired coverage.
To ensure optimal performance, follow these tips:
-
Clean Surfaces: Remove any dirt or contaminants from silicone surfaces before applying lubricant.
-
Apply Evenly: Apply lubricant thoroughly to all surfaces that require lubrication.
-
Avoid Over-Lubrication: Excess lubricant can attract dirt and reduce performance.
-
Reapply Regularly: Lubricants may evaporate or wash away over time. Check and reapply lubricant as needed.
Tips and Tricks for Maximizing Lubricant Effectiveness
In addition to proper selection and application, there are a few tricks to help you get the most out of your silicone lubricants:
-
Use a High-Quality Lubricant: Invest in a reputable brand that provides high-quality lubricants known for their performance and reliability.
-
Consider the Service Life: Choose a lubricant with a service life that matches the operating conditions of your components.
-
Store Lubricants Properly: Store lubricants in a cool, dry place to prevent degradation and extend their shelf life.
-
Avoid Mixing Lubricants: Using lubricants from different manufacturers or types may compromise their performance.
-
Follow Manufacturer's Instructions: Always refer to the manufacturer's instructions for specific application and handling guidelines.
Step-by-Step Approach to Lubricating Silicone Components
To ensure proper lubrication, follow these steps:
-
Clean the Surfaces: Remove any dirt or contaminants from the silicone surfaces using a mild detergent and water.
-
Apply Lubricant: Apply a thin, even layer of lubricant to all mating surfaces.
-
Work into Surfaces: Gently rub the lubricant into the surfaces using a clean cloth or brush.
-
Allow to Set: Allow the lubricant to fully penetrate the silicone surfaces before using the component.
Why Silicone Lubricants Matter
Silicone lubricants play a vital role in maintaining the performance and longevity of silicone components. By reducing friction, preventing wear, and protecting against corrosion, they help ensure the smooth and efficient operation of various devices and machinery.

How Silicone Lubricants Benefit You
Incorporating silicone lubricants into your maintenance routine offers numerous benefits:
-
Enhanced Performance: Reduced friction and improved efficiency lead to increased performance and productivity.
-
Reduced Maintenance Costs: Regular lubrication extends component life, reducing the frequency and cost of repairs.
-
Extended Component Life: Silicone lubricants help protect components from wear and corrosion, significantly extending their lifespan.
-
Improved Reliability: Lubricated components are less prone to failure, improving reliability and reducing downtime.
-
Increased Safety: By preventing friction and wear, silicone lubricants help ensure the safe operation of equipment.
Pros and Cons of Silicone Lubricants
Pros:
- Excellent thermal stability
- Chemical inertness
- Non-toxic and biocompatible
- Low coefficient of friction
- Water repellency
Cons:
- Can be expensive compared to other lubricants
- Some formulations may not be suitable for high-load applications
Conclusion
Silicone lubricants are essential tools for maintaining the optimal performance and longevity of silicone components. By understanding their properties, applications, and benefits, you can select and use the right lubricant for your specific needs. Follow the tips and tricks provided in this guide to maximize the effectiveness of your lubricants and reap the benefits of friction reduction, wear prevention, and extended component life.