Laser Welding: Revolutionizing Manufacturing and Beyond
In today's fast-paced industrial landscape, efficiency, precision, and innovation are paramount. Enter the realm of laser welding, a cutting-edge technology that has emerged as a game-changer in various manufacturing sectors. With its unparalleled advantages, laser welding has become an indispensable tool for businesses seeking to optimize their processes and produce high-quality products.
Transition: Stepping into the World of Laser Welding
Laser welding, the process of joining materials using a focused laser beam, offers a multitude of benefits that set it apart from traditional welding methods. Unlike arc welding or MIG welding, laser welding does not rely on filler materials, which eliminates the need for post-weld cleanup and reduces material waste. Moreover, laser welding boasts exceptional precision, allowing for intricate and delicate welds that would be impossible to achieve with other welding techniques.
How Laser Welding Impacts Industries
The impact of laser welding extends far beyond the manufacturing sector. In the automotive industry, for instance, laser welding has become the preferred method for joining vehicle body panels, ensuring structural integrity and enhancing safety. The aerospace industry, too, relies heavily on laser welding for the construction of aircraft components, where precision and reliability are paramount.
Transition: Exploring the Advantages of Laser Welding
While the benefits of laser welding are far-reaching, let's delve into some of its key advantages that have made it the preferred choice for manufacturers worldwide:


-
Exceptional Precision: Laser welding beams are highly focused, enabling precise control over the welding process. This unparalleled precision makes laser welding ideal for applications where accuracy is crucial.
-
High Welding Speeds: Laser welding operates at lightning-fast speeds, significantly reducing production time and increasing efficiency.
-
Minimal Heat-Affected Zone: Unlike other welding methods, laser welding generates a concentrated and narrow heat-affected zone, resulting in minimal distortion and preserving the integrity of the material.
-
Versatility: Laser welding is compatible with a wide range of materials, including metals, plastics, and even dissimilar materials, providing manufacturers with a versatile solution for various applications.
-
High Weld Strength: Laser welds are known for their exceptional strength and durability, ensuring the longevity and reliability of manufactured products.
Transition: Unveiling the Benefits of Laser Welding
The benefits of laser welding extend beyond its technical capabilities to impact businesses and industries in myriad ways:
-
Cost Reduction: The automation and high welding speeds offered by laser welding significantly reduce labor costs and improve productivity.
-
Increased Production Efficiency: Laser welding streamlines manufacturing processes, reducing lead times and increasing overall output.
-
Enhanced Product Quality: The precision and minimal heat-affected zone associated with laser welding result in superior weld quality, improving product performance and reducing defects.
-
Innovation: Laser welding opens up new possibilities for product design and manufacturing, fostering innovation and competitiveness.
-
Sustainability: Laser welding minimizes material waste and energy consumption compared to traditional welding methods, contributing to environmental sustainability.
Transition: Discovering Effective Strategies for Successful Laser Welding
To fully harness the potential of laser welding, manufacturers must adopt effective strategies that optimize the process and yield exceptional results:
-
Material Selection: Choosing the right material for laser welding is crucial to ensure weldability and achieve desired properties.
-
Laser Power: Selecting the optimal laser power for the specific materials and application is essential for achieving the desired weld depth and penetration.
-
Beam Focus: Proper adjustment of the laser beam's focus ensures precise and consistent weld quality.
-
Shielding Gas: Utilizing an appropriate shielding gas protects the weld area from oxidation and contamination, enhancing weld quality and durability.
-
Process Monitoring: Employing advanced process monitoring systems provides real-time feedback and control over the welding process, ensuring optimal performance.
Transition: Tips and Tricks for Flawless Laser Welding
Beyond effective strategies, manufacturers can enhance their laser welding operations by implementing practical tips and tricks:

-
Clean the Weld Area: Preparing the weld area by removing any dirt, oil, or contaminants ensures proper laser absorption and weld quality.
-
Use Proper Safety Gear: Adhering to safety regulations and wearing appropriate protective gear is essential to prevent injuries from laser radiation and molten metal spatter.
-
Test and Calibrate Equipment: Regularly testing and calibrating laser welding equipment ensures optimal performance and consistent weld quality.
-
Consider Laser Beam Shaping: Utilizing advanced laser beam shaping techniques allows for customized weld profiles, enhancing precision and efficiency.
-
Train Operators: Providing adequate training to operators ensures they are proficient in laser welding techniques and can troubleshoot any issues promptly.
Transition: Stories of Success and Valuable Lessons
The transformative power of laser welding is evident in real-world applications across various industries:
-
Automotive Industry: Laser welding has revolutionized the production of automobiles, enabling the joining of lightweight materials and complex geometries with exceptional strength and precision.
-
Aerospace Industry: In the aerospace sector, laser welding plays a crucial role in manufacturing aircraft components, ensuring structural integrity and reliability under demanding operating conditions.
-
Medical Device Industry: Laser welding has transformed the production of medical devices, allowing for the joining of delicate components with high precision and minimal heat-affected zones, maintaining the sterility and functionality of medical devices.
Transition: Why Laser Welding Matters and How It Benefits Us
Laser welding has emerged as an indispensable tool in modern manufacturing due to its numerous advantages:
-
Reduced Manufacturing Time: The high welding speeds of laser welding significantly decrease production times, improving efficiency and output.
-
Enhanced Product Reliability: Laser welds are renowned for their exceptional strength and durability, contributing to the reliability and longevity of manufactured products.
-
Lower Production Costs: The automation and efficiency of laser welding reduce labor costs and minimize material waste, resulting in lower overall production costs.
-
Improved Safety: Laser welding eliminates the need for hazardous gases or fumes, creating a safer working environment for operators.
-
Increased Innovation Potential: The precision and versatility of laser welding stimulate innovation, enabling the development of new products and manufacturing processes.
Transition: Call to Action
If you are seeking ways to optimize your manufacturing processes, improve product quality, and gain a competitive edge, it is time to embrace the power of laser welding. Invest in the latest laser welding equipment, train your team on best practices, and reap the numerous benefits this revolutionary technology has to offer. Laser welding is not just a trend; it is the future of manufacturing and beyond. By embracing its potential, you can transform your operations and position your business for success in the years to come.
Tables
Table 1: Industries and Applications of Laser Welding
Industry |
Application |
Automotive |
Joining body panels, welding exhaust systems |
Aerospace |
Manufacturing aircraft components, welding engine parts |
Medical Device |
Producing pacemakers, surgical instruments |
Electronics |
Assembling circuit boards, welding heat sinks |
Jewelry |
Creating intricate jewelry designs, welding delicate components |
Table 2: Advantages of Laser Welding
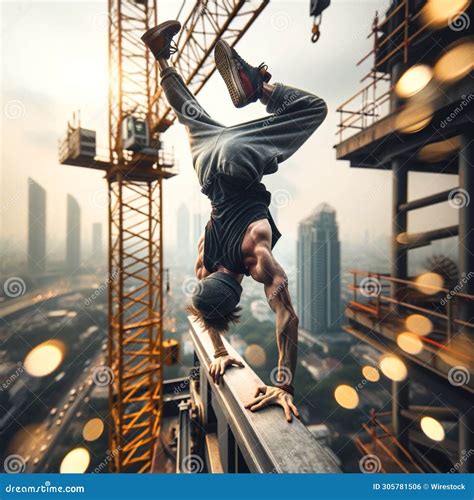
Advantage |
Benefit |
Precision |
Intricate welds, minimal distortion |
Speed |
High welding speeds, reduced production time |
Heat-Affected Zone |
Narrow heat-affected zone, preserves material integrity |
Versatility |
Welds various materials, dissimilar materials |
Strength |
Exceptional weld strength and durability |
Table 3: Benefits of Laser Welding for Businesses and Industries
Benefit |
Impact |
Cost Reduction |
Lower labor costs, reduced material waste |
Increased Efficiency |
Streamlined processes, shorter lead times |
Enhanced Quality |
Superior weld quality, improved product performance |
Innovation |
New product designs, enhanced competitiveness |
Sustainability |
Minimized waste, reduced energy consumption |