A Comprehensive Guide to Industrial Bearings: Unlocking Efficiency and Reliability in Industrial Applications
Introduction
Industrial bearings are the unsung heroes of modern industry, playing a pivotal role in the smooth and efficient operation of countless machines and systems. These precision-engineered components stand at the heart of rotary motion, enabling the transfer of loads while minimizing friction and wear. In this article, we delve into the multifaceted world of industrial bearings, exploring their types, applications, selection criteria, and maintenance strategies. Armed with this knowledge, industries can optimize their operations, enhance equipment lifespan, and maximize their productivity.
Global Market Size and Outlook
The global industrial bearing market is a testament to the significance of these components in the industrial landscape. According to a report by Grand View Research, the market was valued at USD 152.4 billion in 2021 and is projected to reach USD 233.6 billion by 2030, exhibiting a CAGR of 5.0% from 2022 to 2030. This growth is attributed to the rising demand for industrial bearings in various end-use industries, including automotive, aerospace, and manufacturing.
Types of Industrial Bearings
The vast array of industrial bearings available caters to specific application requirements. Each type possesses unique characteristics that make it suitable for different load capacities, speeds, and operating environments. The most common types of industrial bearings include:

-
Rolling Element Bearings: These bearings utilize rolling elements, such as balls or rollers, to minimize friction between rotating surfaces. They come in various forms, including ball bearings, roller bearings, and needle bearings.
-
Plain Bearings: Also known as journal bearings or sleeve bearings, these bearings consist of a rotating shaft that slides against a stationary bearing surface. They are typically used in low-speed applications where high loads and misalignment are present.
-
Hydrodynamic Bearings: These bearings rely on a thin film of fluid to separate the rotating and stationary surfaces, eliminating metal-to-metal contact. They are ideal for high-speed, high-load applications where precision and low friction are critical.
-
Magnetic Bearings: These bearings utilize magnetic forces to levitate the rotating shaft, creating a frictionless environment. They are often employed in applications that require extremely high speeds and precision, such as turbomachinery and medical devices.
Applications of Industrial Bearings
Industrial bearings find applications across a wide spectrum of industries, including:
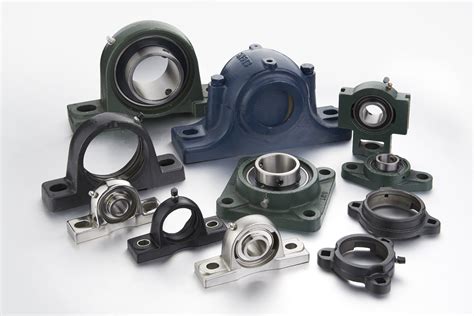
-
Automotive: Bearings support the rotation of various components in vehicles, such as engines, transmissions, and wheels.
-
Aerospace: Bearings are crucial in aircraft engines, landing gear, and flight control systems.
-
Manufacturing: Bearings enable smooth operation of machinery used in metalworking, plastics processing, and food processing.
-
Power Generation: Bearings play a vital role in turbines, generators, and pumps used in power plants.
-
Mining and Construction: Bearings are essential in heavy machinery used in mining and construction operations.
Selection Criteria for Industrial Bearings
Selecting the right industrial bearing for an application involves careful consideration of several factors:
-
Load Capacity: The bearing must be able to withstand the expected loads in the application.
-
Speed: The bearing should be rated for the operating speed of the machinery.
-
Precision: The bearing should meet the required precision levels to ensure proper operation and accuracy.
-
Lubrication: The bearing type and application determine the appropriate lubrication method.
-
Environmental Conditions: The bearing must be suitable for the operating environment, including temperature, humidity, and contamination levels.
Maintenance Strategies for Industrial Bearings
Proper maintenance is crucial to maximize the lifespan and reliability of industrial bearings. Effective strategies include:
-
Regular Inspections: Regularly inspect bearings for signs of wear, contamination, or damage.
-
Proper Lubrication: Lubricate bearings according to the manufacturer's recommendations using the appropriate lubricant.
-
Condition Monitoring: Use condition monitoring technologies to monitor bearing performance and detect potential problems early on.
-
Predictive Maintenance: Implement predictive maintenance strategies to identify and address potential bearing issues before they cause downtime.
-
Training: Provide training to maintenance personnel to ensure proper bearing handling, installation, and troubleshooting.
Common Mistakes to Avoid When Using Industrial Bearings
To ensure optimal performance and longevity of industrial bearings, avoid these common mistakes:

-
Overloading: Applying excessive loads on bearings can lead to premature failure.
-
Improper Lubrication: Using the wrong lubricant or neglecting lubrication can result in increased friction and wear.
-
Misalignment: Incorrect alignment of bearings can cause abnormal wear and premature failure.
-
Contamination: Avoid contamination of bearings with dirt, water, or other foreign particles.
-
Improper Installation: Improper installation techniques can lead to bearing damage and reduced performance.
How to Step-by-Step Approach to Bearing Maintenance
Follow these steps for effective bearing maintenance:

- Identify the bearing type and application.
- Refer to the manufacturer's recommendations for maintenance intervals and procedures.
- Inspect the bearing for signs of wear, contamination, or damage.
- Clean the bearing and surrounding area thoroughly.
- Apply the appropriate lubricant according to the manufacturer's specifications.
- Reinstall the bearing and ensure proper alignment.
- Monitor bearing performance using condition monitoring technologies.
- Take corrective actions if any deviations from normal operating parameters are detected.
Pros and Cons of Different Industrial Bearing Types
Rolling Element Bearings:
Pros:
- Low friction
- High load capacity
- Long lifespan
Cons:
- Sensitive to misalignment
- Can generate noise
Plain Bearings:
Pros:
- Can accommodate misalignment
- Low noise levels
- Suitable for low-speed, high-load applications
Cons:
- Higher friction
- Shorter lifespan
Hydrodynamic Bearings:
Pros:
- Extremely low friction
- High precision
- Long lifespan
Cons:
- Complex design
- Require high oil flow rates
Magnetic Bearings:
Pros:
- Frictionless operation
- High precision
- Long lifespan
Cons:
- Expensive
- Require specialized expertise
Conclusion
Industrial bearings are the backbone of countless industrial applications, enabling efficient and reliable operation of machinery and systems. Understanding the different types, applications, and maintenance strategies of industrial bearings is crucial for industries to maximize equipment lifespan, reduce downtime, and optimize productivity. By implementing effective bearing selection, maintenance, and troubleshooting practices, industries can unlock the full potential of these precision-engineered components and drive long-term success.