The Ultimate Guide to Pin Bearings: A Comprehensive Resource
Introduction
Pin bearings are essential components in various industrial applications, providing rotational support and reducing friction. They are widely used in machinery, automotive systems, and aerospace equipment. This comprehensive guide will delve into the world of pin bearings, exploring their types, applications, advantages, and best practices. Whether you're a design engineer, maintenance technician, or anyone seeking to enhance your understanding of these critical bearings, this article has everything you need to know.
Types of Pin Bearings
Pin bearings come in various types, each with its unique characteristics and applications:
Cylindrical Pin Bearings:
Cylindrical pin bearings consist of a cylindrical pin rotating within a cylindrical housing. They offer high load capacity and are commonly used in low-speed applications where accuracy is not a primary concern.
Conical Pin Bearings:
Conical pin bearings have a conical pin rotating within a conical housing. They provide higher accuracy and load capacity compared to cylindrical bearings and are suitable for medium-speed applications.

Tapered Roller Pin Bearings:
Tapered roller pin bearings utilize tapered rollers that roll between a tapered inner and outer race. They offer excellent load capacity and accuracy, making them ideal for high-speed and heavy-duty applications.
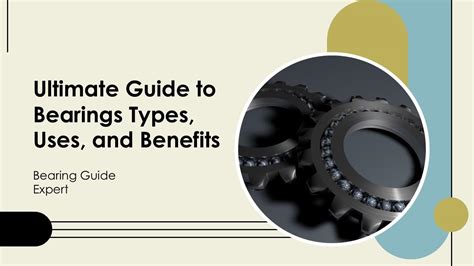
Needle Roller Pin Bearings:
Needle roller pin bearings have a cylindrical pin with a small diameter. They provide high load capacity in a compact design and are commonly used in confined spaces.
Spherical Pin Bearings:
Spherical pin bearings have a spherical pin rotating within a spherical housing. They offer high load capacity and are suitable for applications requiring self-aligning capabilities.

Applications of Pin Bearings
Pin bearings are extensively used across various industries, including:
-
Automotive: Crankshafts, transmissions, and steering systems
-
Machinery: Conveyor belts, pumps, and gearboxes
-
Aerospace: Landing gear, actuators, and control systems
-
Medical Equipment: Surgical instruments, MRI machines, and robotic surgery
-
Industrial Machinery: Printing presses, textile machinery, and food processing equipment
Advantages of Pin Bearings
Pin bearings offer numerous advantages over other bearing types:
-
High Load Capacity: Pin bearings can withstand significant loads due to their robust construction and design.
-
Low Friction: The rolling action between the pin and housing reduces friction, resulting in increased efficiency and reduced wear.
-
Accuracy and Precision: Pin bearings provide high levels of accuracy and precision due to their precise manufacturing tolerances.
-
Long Service Life: Pin bearings are designed to last longer than other bearing types, offering reliable performance over extended periods.
-
Compact Design: Pin bearings are relatively compact, making them suitable for applications with space constraints.
Best Practices for Pin Bearing Usage
To ensure optimal performance and longevity of pin bearings, the following best practices should be considered:
-
Proper Lubrication: Regular lubrication is crucial to reduce friction and prevent premature wear. Use high-quality lubricants recommended for pin bearing applications.
-
Proper Mounting: Pin bearings should be correctly mounted and aligned to avoid excessive stress and premature failure.
-
Load Considerations: Pin bearings should be selected according to the anticipated load requirements. Overloading can lead to damage and reduced bearing life.
-
Temperature Management: Pin bearings should be protected from excessive temperatures, which can affect their performance and reduce their life.
-
Regular Maintenance: Regular inspections and maintenance, including cleaning, lubrication, and monitoring, are essential to ensure optimal bearing performance.
Effective Strategies for Pin Bearing Applications
-
Use the Right Bearing for the Job: Select the appropriate pin bearing type based on the application requirements, considering load capacity, accuracy, and speed.
-
Optimize Lubrication: Implement a suitable lubrication strategy based on the bearing type, operating conditions, and manufacturer's recommendations.
-
Monitor Bearing Condition: Implement condition monitoring techniques such as vibration analysis or temperature monitoring to detect potential issues early.
-
Avoid Misalignment: Ensure proper alignment of the bearing components to prevent excessive loads and premature failure.
-
Protect from Contamination: Keep pin bearings clean and protected from contaminants such as dirt, moisture, and abrasives.
Tips and Tricks for Pin Bearing Maintenance
-
Inspect Regularly: Conduct periodic visual inspections to check for any signs of damage, wear, or contamination.
-
Lubricate Regularly: Follow the recommended lubrication schedule and use the proper lubricants to minimize friction and extend bearing life.
-
Prevent Contamination: Keep bearing surfaces clean and protected from external contaminants.
-
Monitor Vibration and Temperature: Monitor vibration and temperature levels to detect potential issues or changes in bearing condition.
-
Store Properly: Store pin bearings in a clean, dry, and controlled environment to prevent corrosion and damage.
Common Mistakes to Avoid
-
Overloading: Exceeding the rated load capacity of a pin bearing can lead to premature failure.
-
Incorrect Mounting: Improper mounting, misalignment, or insufficient tightening can cause excessive stress and reduced bearing performance.
-
Inadequate Lubrication: Insufficient or incorrect lubrication can lead to increased friction and accelerated wear.
-
Contamination: Allowing contaminants to enter the bearing can cause damage to the bearing surfaces and reduce its life.
-
Ignoring Maintenance: Neglecting regular inspections and maintenance can lead to undetected issues and potential bearing failure.
Step-by-Step Approach for Pin Bearing Replacement
- Safety First: Ensure proper safety precautions are taken before beginning the replacement process.
- Disassembly: Carefully disassemble the components surrounding the pin bearing, following proper procedures and using the appropriate tools.
- Bearing Removal: Remove the old pin bearing by carefully tapping it out of its housing or using a suitable bearing puller.
- Cleaning and Inspection: Clean the bearing housing and surrounding components to remove any contaminants. Inspect the housing for any damage or wear.
- New Bearing Installation: Press the new pin bearing into the housing using a suitable bearing press or hand tools.
- Lubrication: Apply the appropriate lubricant to the bearing surfaces and surrounding components.
- Assembly: Reassemble the components around the pin bearing, ensuring proper alignment and tightening.
- Final Checks: Perform a final check to ensure the pin bearing is securely installed and all components are properly assembled.
Pros and Cons of Pin Bearings
Pros:
- High load capacity
- Low friction
- Accuracy and precision
- Long service life
- Compact design
Cons:
- Can be more expensive than other bearing types
- May require specialized installation and maintenance procedures
Conclusion
Pin bearings are essential components that play a critical role in various industrial applications. By understanding the different types, applications, advantages, and best practices, you can effectively implement pin bearings to enhance the performance, efficiency, and longevity of your machinery and systems. Proper maintenance, lubrication, and condition monitoring are crucial to ensure optimal bearing performance and prevent premature failure.