Comprehensive Guide to Advanced Process Control and Monitoring Systems (APCMS): Empowering Process Optimization
Introduction
In today's highly competitive manufacturing landscape, optimizing processes is crucial to achieving operational excellence and maximizing profitability. Advanced Process Control and Monitoring Systems (APCMS) play a transformative role in this pursuit, providing real-time data, insights, and control capabilities that enable businesses to enhance product quality, reduce costs, and improve overall efficiency. This comprehensive guide will delve into the essential aspects of APCMS, covering:
- Key benefits and advantages
- Different types of APCMS
- Implementation strategies
- Common mistakes to avoid
- Step-by-step approach to successful deployment
Key Benefits of APCMS
APCMS offer a wide range of benefits, including:
-
Improved product quality: Real-time monitoring and control ensure consistent adherence to specifications, reducing defects and enhancing customer satisfaction.
-
Increased operational efficiency: Automated data collection and analysis identify inefficiencies and bottlenecks, allowing for targeted improvements.
-
Reduced costs: Optimized processes reduce waste, energy consumption, and downtime, resulting in significant cost savings.
-
Improved asset utilization: Predictive maintenance capabilities extend equipment life and minimize unplanned outages.
-
Enhanced safety: Real-time monitoring identifies potential risks and triggers alarms to ensure a safe operating environment.
Types of APCMS
There are various types of APCMS available, each tailored to specific industries and applications. Common types include:
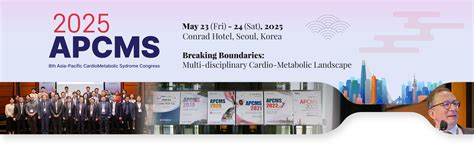
-
Statistical Process Control (SPC): Uses statistical methods to monitor and control processes, identifying and eliminating sources of variability.
-
Model Predictive Control (MPC): Employs mathematical models to predict future process behavior, enabling proactive adjustment of control parameters.
-
Fault Detection and Diagnosis (FDD): Monitors processes for abnormal behavior and triggers alarms when potential faults are detected.
-
Supervisory Control and Data Acquisition (SCADA): Provides a centralized platform for monitoring, controlling, and collecting data from multiple processes.
Implementation Strategies
Successful APCMS implementation requires careful planning and a well-defined strategy. Effective strategies include:
-
Phased approach: Implement APCMS in stages to minimize disruption and ensure a smooth transition.
-
Pilot projects: Test and validate APCMS in a controlled environment before full-scale deployment.
-
Stakeholder involvement: Engage personnel from all levels of the organization to ensure buy-in and support.
-
Training and development: Provide comprehensive training to ensure operators and engineers are proficient in using APCMS.
-
Continuous improvement: Regularly review and update APCMS to optimize performance and address evolving needs.
Common Mistakes to Avoid
Common mistakes to avoid during APCMS implementation include:
-
Insufficient stakeholder involvement: Failing to engage key stakeholders can lead to resistance and implementation challenges.
-
Lack of data analysis: Ignoring data analysis and insights can limit the potential benefits of APCMS.
-
Inadequate training: Inadequate training can result in operational errors and reduced system effectiveness.
-
Overreliance on technology: APCMS should complement existing processes and not replace human expertise.
-
Neglecting maintenance: Proper maintenance is essential to ensure the accuracy and reliability of APCMS.
Step-by-Step Approach to Deployment
A step-by-step approach to successful APCMS deployment involves:
-
Define project scope: Determine the processes to be monitored and the desired outcomes.
-
Select and implement APCMS: Choose an APCMS that aligns with specific needs and capabilities.
-
Configure and calibrate APCMS: Ensure proper configuration and calibration to accurately monitor and control processes.
-
Train personnel: Provide comprehensive training to operators and engineers.
-
Monitor and evaluate performance: Regularly review performance indicators and make necessary adjustments.
-
Continuously improve: Regularly update and enhance APCMS to optimize performance and address evolving needs.
Effective Strategies for Process Optimization
Effective APCMS-based strategies for process optimization include:
-
Data analysis and visualization: Use real-time data to identify patterns, trends, and areas for improvement.
-
Predictive analytics: Leverage machine learning algorithms to forecast future process behavior and anticipate potential issues.
-
Multivariate optimization: Optimize multiple process variables simultaneously to achieve optimal performance.
-
Automatic tuning: Utilize APCMS capabilities to automatically adjust control parameters based on changing process conditions.
-
Advanced control algorithms: Employ advanced control algorithms, such as MPC, to enhance process stability and performance.
Key Performance Indicators (KPIs) for APCMS
Measuring performance is crucial to assess the effectiveness of APCMS. Relevant KPIs include:
-
Overall Equipment Effectiveness (OEE): A comprehensive metric that measures equipment availability, performance, and quality.
-
Mean Time Between Failures (MTBF): The average time between equipment failures.
-
Mean Time to Repair (MTTR): The average time to repair failed equipment.
-
Energy consumption: The amount of energy consumed by processes.
-
Waste reduction: The percentage of waste eliminated through process optimization.
Examples of Successful APCMS Implementation
Numerous organizations have successfully implemented APCMS to enhance their operations. Example case studies include:
:%20Empowering%20Process%20Optimization)
-
Chemical plant: Implementation of APCMS resulted in a 20% increase in product yield and a 15% reduction in energy consumption.
-
Automotive manufacturer: Use of APCMS led to a 30% reduction in defects and a 10% increase in production output.
-
Oil and gas company: APCMS helped optimize drilling operations, resulting in a 25% reduction in drilling time and a 15% increase in well productivity.
Conclusion
APCMS are powerful tools that empower manufacturers to optimize processes, enhance product quality, reduce costs, and improve overall efficiency. By leveraging data, analytics, and control capabilities, businesses can achieve operational excellence and gain a competitive edge. A well-planned and executed APCMS implementation involves careful planning, stakeholder involvement, training, and continuous improvement. By embracing effective strategies and avoiding common pitfalls, organizations can unlock the full potential of APCMS and transform their operations.
)
Tables
Table 1: Benefits of APCMS
Benefit |
Description |
Improved product quality |
Real-time monitoring and control ensure consistent adherence to specifications, reducing defects and enhancing customer satisfaction. |
Increased operational efficiency |
Automated data collection and analysis identify inefficiencies and bottlenecks, allowing for targeted improvements. |
Reduced costs |
Optimized processes reduce waste, energy consumption, and downtime, resulting in significant cost savings. |
Improved asset utilization |
Predictive maintenance capabilities extend equipment life and minimize unplanned outages. |
Enhanced safety |
Real-time monitoring identifies potential risks and triggers alarms to ensure a safe operating environment. |
Table 2: Types of APCMS
Type |
Description |
Statistical Process Control (SPC) |
Uses statistical methods to monitor and control processes, identifying and eliminating sources of variability. |
Model Predictive Control (MPC) |
Employs mathematical models to predict future process behavior, enabling proactive adjustment of control parameters. |
Fault Detection and Diagnosis (FDD) |
Monitors processes for abnormal behavior and triggers alarms when potential faults are detected. |
Supervisory Control and Data Acquisition (SCADA) |
Provides a centralized platform for monitoring, controlling, and collecting data from multiple processes. |
Table 3: Effective APCMS-Based Strategies for Process Optimization
Strategy |
Description |
Data analysis and visualization |
Use real-time data to identify patterns, trends, and areas for improvement. |
Predictive analytics |
Leverage machine learning algorithms to forecast future process behavior and anticipate potential issues. |
Multivariate optimization |
Optimize multiple process variables simultaneously to achieve optimal performance. |
Automatic tuning |
Utilize APCMS capabilities to automatically adjust control parameters based on changing process conditions. |
Advanced control algorithms |
Employ advanced control algorithms, such as MPC, to enhance process stability and performance. |