Linear Bearings: The Ultimate Guide for Precision Motion
Introduction
Linear bearings are indispensable components in a wide range of industrial and commercial applications, including precision machinery, automation equipment, medical devices, and semiconductor manufacturing. They enable smooth, low-friction linear motion along a predefined axis, ensuring high accuracy and repeatability. In this comprehensive guide, we will delve into the world of linear bearings, exploring their types, applications, advantages, and best practices for their effective use.
Types of Linear Bearings
Linear bearings are classified into two main categories based on their design and operating principle:
1. Ball Linear Bearings
- Utilize ball bearings as the rolling elements, providing low friction and high load capacity.
- Suitable for applications requiring high precision and smoothness of motion.
- Available in various configurations, including round rails, square rails, and profile rails.
2. Roller Linear Bearings
- Employ rollers as the rolling elements, offering higher load capacity than ball bearings.
- Ideal for heavy-duty applications and environments with high vibration and shock loads.
- Available in different types, such as cylindrical rollers, needle rollers, and crossed rollers.
Applications of Linear Bearings
The versatility of linear bearings makes them widely applicable in numerous industries and sectors:
-
Precision Machinery: Machine tools, coordinate measuring machines, inspection equipment
-
Automation Equipment: Robots, gantry systems, conveyor systems
-
Medical Devices: Surgical robots, imaging systems, patient positioning tables
-
Semiconductor Manufacturing: Wafer handling and processing equipment, lithography systems
-
Other Applications: Automotive parts, food processing equipment, packaging machinery
Advantages of Linear Bearings
Linear bearings offer several advantages over traditional sliding bearings:

-
Low Friction: Precision-engineered rolling elements minimize friction, resulting in smoother motion and reduced power consumption.
-
High Accuracy: Precision machining and manufacturing techniques ensure high accuracy and repeatability of linear movement.
-
High Load Capacity: Designed to withstand substantial loads, linear bearings enable reliable operation in demanding applications.
-
Long Service Life: With proper maintenance, linear bearings can achieve extended service life, reducing downtime and maintenance costs.
-
Compact Design: Their compact design allows for space-efficient implementations, particularly in constrained environments.
Common Mistakes to Avoid
To ensure optimal performance and longevity of linear bearings, it is crucial to avoid certain common mistakes:
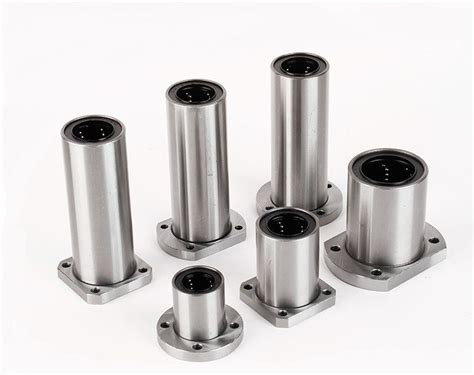
-
Overloading: Exceeding the specified load capacity can lead to premature bearing failure and damage.
-
Improper Lubrication: Regular lubrication is essential for minimizing friction and wear. Using incompatible or insufficient lubrication can result in premature bearing degradation.
-
Contamination: Contaminants, such as dirt, dust, and moisture, can interfere with bearing operation and shorten service life.
-
Misalignment: Incorrect shaft alignment or mounting errors can impose unnecessary stress on bearings, reducing their performance and durability.
-
Excessive Tightening: Overtightening fasteners can cause binding and premature bearing failure.
How to Select Linear Bearings
Selecting the appropriate linear bearings for an application requires careful consideration of the following factors:
-
Load Capacity: Determine the maximum static and dynamic loads the bearings will encounter.
-
Speed: Specify the operating speed of the linear motion system.
-
Accuracy: Establish the required precision and repeatability of movement.
-
Environment: Consider operating conditions, such as temperature, vibration, and potential contamination.
-
Space Constraints: Determine the available space for bearing installation and operation.
Step-by-Step Approach for Effective Use
To maximize the benefits and longevity of linear bearings, follow these steps:

-
Proper Selection: Conduct a thorough evaluation of application requirements and select the appropriate bearing type and specifications.
-
Careful Installation: Ensure proper alignment and mounting of bearings, following manufacturer's guidelines precisely.
-
Regular Lubrication: Establish a lubrication schedule using the specified lubricant type and frequency.
-
Frequent Inspection: Regularly inspect bearings for wear, damage, or contamination, and take corrective actions as needed.
-
Preventive Maintenance: Schedule periodic maintenance, including cleaning, lubrication, and replacement of worn components.
Why Linear Bearings Matter
Linear bearings play a crucial role in advancing precision motion and automation in various industries and sectors. Their unique properties and advantages make them essential components for:
-
Enhanced Productivity: Reduced friction and high accuracy enable faster cycle times and improved production efficiency.
-
Improved Quality: Precision motion ensures consistent and repeatable movements, resulting in higher product quality.
-
Reduced Downtime: Long service life and low maintenance requirements minimize downtime, increasing equipment availability.
-
Energy Savings: Low friction reduces power consumption, leading to energy savings and reduced operating costs.
-
Innovation: Linear bearings contribute to the development of innovative products and technologies, driving advancement and progress.
Success Stories in Practice
Case Study 1: A leading medical device manufacturer replaced traditional sliding bearings with linear bearings in their surgical robot. The result was a significant improvement in accuracy and repeatability, enabling more precise surgical procedures and reduced patient downtime.
Case Study 2: An automation equipment provider integrated linear bearings into their gantry system for a semiconductor manufacturing facility. The high load capacity and precision of the bearings ensured reliable and accurate wafer handling, reducing production defects and improving yield.
Case Study 3: A food processing plant upgraded their conveyor system with linear bearings. The low friction and corrosion resistance of the bearings led to smoother product movement, increased productivity, and reduced maintenance costs.
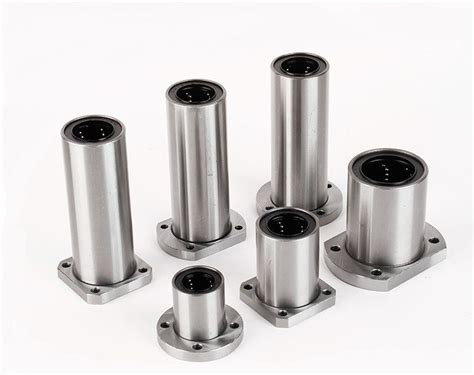
Conclusion
Linear bearings are indispensable for precision motion and automation, playing a vital role in advancing various industries and sectors. Their low friction, high accuracy, high load capacity, and long service life make them ideal for applications where precise linear movement and durability are paramount. By carefully selecting, installing, and maintaining linear bearings, engineers and technicians can optimize performance, extend equipment life, and contribute to improved productivity, quality, and innovation.