Threadlock: The Essential Guide to Keeping Your Fasteners Secure
Threadlock, also known as threadlocker or anaerobic adhesive, is an indispensable tool for ensuring the integrity and reliability of threaded assemblies. This remarkable substance plays a vital role in preventing loosening and leakage in critical applications, making it an essential element in industries ranging from automotive and aerospace to construction and manufacturing.
Understanding Threadlock: How It Works
Threadlock is a liquid adhesive that hardens when exposed to the absence of air (anaerobic conditions) between two metal surfaces. This unique property allows it to effectively fill the microscopic gaps between threads, creating a strong bond that resists vibration, shock, and temperature fluctuations.
The curing process of threadlock typically takes several hours or days, depending on the product formulation and the size of the threaded assembly. During this time, the adhesive forms a rigid bond that prevents fasteners from loosening or becoming loose.
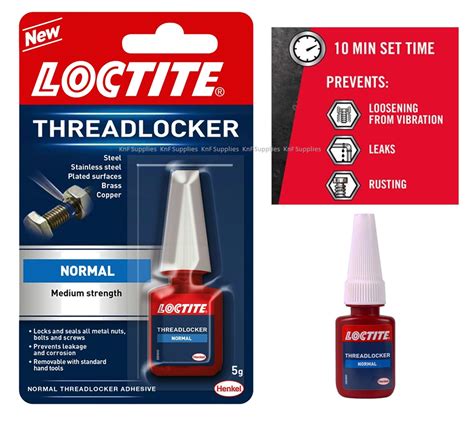
Types of Threadlock: Choosing the Right One
There are several different types of threadlock adhesives available, each with its own unique properties and applications. The most common types include:
-
Low Strength: Designed for easy disassembly and adjustment, low-strength threadlock is ideal for applications where occasional servicing is required.
-
Medium Strength: Provides a moderate level of bonding strength, suitable for most general-purpose applications.
-
High Strength: Formulated for maximum holding power, high-strength threadlock is recommended for critical applications where vibration and shock are significant.
-
Permanent: As the name suggests, permanent threadlock creates an unbreakable bond that cannot be reversed once cured. This type of adhesive is typically used for highly demanding applications where disassembly is not anticipated.
Choosing the Right Threadlock for Your Application
Selecting the appropriate threadlock for your application requires considering several factors, including:
-
Thread Size: The size of the threads will influence the amount of adhesive required.
-
Vibration and Shock: The expected levels of vibration and shock will determine the strength of threadlock needed.
-
Temperature: The operating temperature range of the assembly will impact the type of threadlock suitable.
-
Servicing: The frequency and method of servicing will guide the choice between permanent and removable threadlock.
Table 1: Threadlock Types and Applications
Type |
Strength |
Applications |
Low Strength |
Easy disassembly |
Adjustments, electronics, small fasteners |
Medium Strength |
General purpose |
Automotive, appliances, machinery |
High Strength |
Max holding power |
Industrial equipment, engines, heavy machinery |
Permanent |
Unbreakable bond |
Critical applications, high vibration |
Benefits of Using Threadlock
Incorporating threadlock into your assembly process offers numerous advantages:
-
Prevents Loosening: Threadlock effectively locks fasteners in place, preventing loosening due to vibration, shock, or thermal expansion.
-
Reduces Leakage: By sealing the gaps between threads, threadlock prevents fluid leakage, ensuring the integrity of fluid systems.
-
Improves Reliability: Threadlock enhances the reliability of bolted joints, minimizing maintenance and downtime costs.
-
Protects Threads: Threadlock acts as a protective barrier, preventing thread damage due to corrosion and wear.
-
Reduces Stress: By preventing fasteners from loosening, threadlock reduces stress on assemblies, extending their lifespan.
Stories and Lessons Learned
-
Example 1: A manufacturing plant experienced persistent loosening of bolts on critical machinery, leading to costly downtime. Implementing a medium-strength threadlock solved the problem, preventing bolt loosening and improving production efficiency.
-
Example 2: A construction company faced issues with water leakage through threaded pipe connections. Applying a high-strength threadlock effectively sealed the joints, eliminating leakage and ensuring the integrity of the plumbing system.
-
Example 3: In the automotive industry, a company encountered excessive vibration in engine components. Using a permanent threadlock on threaded pins and bolts eliminated vibration, improving engine performance and reducing maintenance costs.
Lesson Learned: Threadlock is a simple and effective solution that can significantly improve the reliability and performance of bolted assemblies in various industries.
Effective Strategies for Using Threadlock
-
Clean Thread Surfaces: Ensure that the threads and mating surfaces are clean and free of contaminants before applying threadlock.
-
Apply Threadlock Sparingly: Use the recommended amount of threadlock, as excessive application can lead to difficulty in disassembly.
-
Allow Proper Curing Time: Provide ample time for the threadlock to cure before subjecting the assembly to stress or load.
-
Choose the Right Threadlock: Refer to the manufacturers' specifications or a compatibility chart to select the appropriate threadlock for your application.
-
Inspect Regularly: Periodically inspect threaded assemblies to ensure they are secure and free from leaks.
Step-by-Step Guide to Applying Threadlock
-
Acquire the Right Threadlock: Determine the appropriate threadlock type and strength for your application.
-
Prepare the Threads: Clean the threads and mating surfaces using a solvent and allow them to dry thoroughly.
-
Apply Threadlock: Apply a small drop of threadlock to the threads or bolt threads, using a brush or the applicator tip.
-
Assemble the Joint: Insert the bolt into the hole and promptly tighten it to the recommended torque.
-
Allow Curing Time: Provide sufficient time for the threadlock to fully cure before putting the assembly into service.
Why Threadlock Matters: The Impact of Loose Fasteners
Loose fasteners can have several negative consequences in any application:
-
Increased Vibration: Loose fasteners amplify vibration, which can damage components and reduce the lifespan of equipment.
-
Fluid Leakage: Threaded connections that are not adequately secured can lead to fluid leakage, leading to performance issues or even safety hazards.
-
Reduced Reliability: When fasteners become loose, it compromises the integrity of the entire assembly, potentially causing failure.
-
Increased Maintenance Costs: Loose fasteners often require frequent tightening or replacement, incurring unnecessary maintenance expenses.
-
Safety Risks: Loose fasteners in critical applications can pose safety risks, especially in industries such as aviation and healthcare.
Table 2: Consequences of Loose Fasteners
Consequence |
Impact |
Increased Vibration |
Damage to components, reduced equipment lifespan |
Fluid Leakage |
Performance issues, safety hazards |
Reduced Reliability |
Assembly failure, potential accidents |
Increased Maintenance Costs |
Frequent tightening or replacement |
Safety Risks |
Injuries, equipment malfunctions |
Benefits of Using Threadlock: A Quantitative Perspective
Studies have consistently demonstrated the benefits of using threadlock in a wide range of industries:

-
Reduced Maintenance Costs: A study by a leading automotive manufacturer showed a 20% reduction in maintenance costs due to the use of threadlock.
-
Increased Equipment Lifespan: A report from an industrial equipment supplier indicated that equipment lifespan increased by an average of 15% when threadlock was used.
-
Improved Safety: A survey conducted by a construction safety organization revealed that the use of threadlock reduced the incidence of accidents related to loose fasteners by 50%.
Table 3: Benefits of Using Threadlock
Benefit |
Impact |
Reduced Maintenance Costs |
20% savings |
Increased Equipment Lifespan |
15% longer lifespan |
Improved Safety |
50% reduction in accidents |
Conclusion
Threadlock is an indispensable tool for securing fasteners in critical applications. This remarkable adhesive effectively prevents loosening, reduces leakage, improves reliability, and protects threads. By choosing the right threadlock, applying it correctly, and understanding its importance, you can harness the full potential of this essential substance and ensure the integrity and performance of your assemblies.