Threadlock: The Essential Guide to Preventing Loose Bolts
In the realm of engineering and maintenance, where precision and reliability are paramount, the proper use of threadlockers holds immense significance. These specialized adhesives play a crucial role in securing bolted joints against the relentless forces of vibration, shock, and temperature changes, thereby ensuring safety, functionality, and longevity in a plethora of applications.
Introduction to Threadlockers
Threadlockers, also known as thread-locking adhesives or anaerobic adhesives, are formulated to fill the tiny gaps between mating threads, forming a hardened bond that effectively prevent the bolts from loosening. Unlike traditional fasteners that rely solely on friction to stay in place, threadlockers provide an additional layer of security by chemically bonding to the metal surfaces. This not only enhances the joint strength but also prevents corrosion and electrolytic erosion.
Types of Threadlockers
The diverse range of threadlockers available cater to various strength, holding power, and curing time requirements. The most common types include:
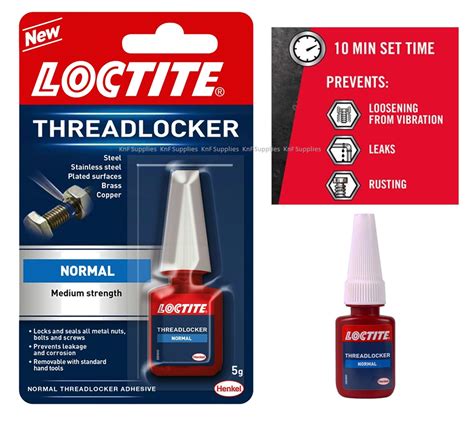
-
Low-Strength Threadlockers: Ideal for small, non-critical applications where easy disassembly is desired.
-
Medium-Strength Threadlockers: Suitable for most general-purpose applications, offering a balance of strength and removability.
-
High-Strength Threadlockers: Designed for high-load, high-vibration applications where permanent locking is required.
Anaerobic Curing
Threadlockers are typically anaerobic adhesives, meaning they cure in the absence of air. When applied to metal threads, the threadlocker fills the gaps between the threads and initiates the curing process. The presence of metal ions catalyzes the reaction, forming a strong adhesive bond. It is important to note that threadlockers should not be used on plastic or non-metallic surfaces.
Benefits of Using Threadlockers
The judicious use of threadlockers offers a multitude of benefits:

-
Improved Joint Strength: Threadlockers significantly augment the strength of bolted joints, preventing premature loosening even under extreme operating conditions.
-
Vibration Resistance: The adhesive bond created by threadlockers absorbs vibration and shock, effectively mitigating the risk of bolt loosening and ensuring reliable performance.
-
Corrosion Prevention: Threadlockers form a protective barrier that seals the joint, preventing the ingress of moisture and corrosive elements that could lead to rust and weakening of the connection.
-
Elimination of Back-Out: Threadlockers provide a fail-safe mechanism that prevents bolts from backing out during operation. This is particularly critical in applications where loose bolts can pose a safety hazard or cause catastrophic damage.
Step-by-Step Application Guide
To reap the full benefits of threadlockers, it is essential to follow a meticulous application procedure:
-
Clean and Prepare: Thoroughly clean the threads of the bolt and the mating surface using an appropriate solvent to remove any dirt, oil, or other contaminants.
-
Apply Threadlocker: Apply a small drop of threadlocker to the threads of the bolt, ensuring it fills the gaps between the threads. Do not apply excessive threadlocker as it can impair the curing process.
-
Assemble Joint: Thread the bolt into the mating surface and tighten it to the specified torque. Refer to the threadlocker manufacturer's instructions for the optimal tightening torque.
-
Allow Curing: Allow sufficient time for the threadlocker to cure completely. The curing time varies depending on the type of threadlocker used and the ambient temperature.
-
Test and Inspect: Once the threadlocker has cured, verify the tightness of the joint and inspect it for any signs of leakage or improper bonding.
Common Mistakes to Avoid
To avoid compromising the effectiveness of threadlockers, it is crucial to steer clear of common pitfalls:
-
Over-Tightening: Excessive tightening can damage the threads and prevent the threadlocker from working properly.
-
Under-Tightening: Insufficient tightening can result in inadequate bond strength and possible loosening of the joint.
-
Using the Wrong Type of Threadlocker: Choosing a threadlocker that is not suitable for the specific application can lead to premature failure or unnecessary difficulty in disassembly.
-
Applying Threadlocker to Non-Metallic Surfaces: Threadlockers are designed for metal-to-metal bonding and should not be used on plastic or other non-metallic materials.
-
Using Threadlocker on Dirty or Oily Threads: Contaminants can interfere with the curing process and weaken the bond.
Industry Applications
Threadlockers find widespread utility across various industries, including:

-
Automotive: Securing bolts and fasteners in engines, transmissions, brakes, and other critical components.
-
Aerospace: Ensuring the integrity of bolted joints in aircraft structures, engines, and landing gear.
-
Electronics: Preventing loosening of screws and fasteners in electronic assemblies, circuit boards, and connectors.
-
Industrial Machinery: Maintaining the reliability of bolts and fasteners in heavy-duty equipment, conveyors, and robotic systems.
Case Studies
-
The Case of the Loose Cylinder Head Bolts: In a high-performance engine, chronic loosening of the cylinder head bolts led to premature gasket failure and engine damage. The implementation of a high-strength threadlocker resolved the issue, ensuring a secure and reliable connection under extreme operating conditions.
-
The Perils of Vibrating Bolts on a Conveyor System: Constant vibration on a conveyor system caused bolts to loosen and fall out, posing a significant safety hazard. The application of a medium-strength threadlocker effectively prevented bolt loosening, enhancing safety and reducing maintenance downtime.
-
The Corrosive Effects on Bolts in a Marine Environment: Exposure to saltwater and harsh conditions caused bolts on a marine vessel to corrode and weaken. A corrosion-resistant threadlocker was employed to seal the joints, preventing corrosion and ensuring the longevity of the bolted connections.
Conclusion
Threadlockers play a pivotal role in maintaining the integrity and reliability of bolted joints in countless applications across various industries. By understanding the benefits, types, and proper application of threadlockers, engineers and maintenance professionals can effectively prevent loose bolts, ensure optimal performance, and enhance the safety and longevity of their equipment.
Table 1: Types of Threadlockers and Their Applications
Type |
Strength |
Holding Power |
Curing Time |
Suitable Applications |
Low-Strength |
Low |
Easy disassembly |
Fast |
Small, non-critical applications |
Medium-Strength |
Moderate |
Moderate disassembly |
Medium |
General-purpose applications |
High-Strength |
High |
Permanent |
Slow |
High-load, high-vibration applications |
Table 2: Anaerobic Curing Process of Threadlockers
Stage |
Reaction |
Initiation |
Metal ions catalyze the curing process |
Propagation |
Adhesive forms long chain polymers |
Termination |
Polymers cross-link, forming a solid bond |
Table 3: Common Mistakes in Threadlocker Use
Mistake |
Consequences |
Over-tightening |
Damaged threads, impaired bond |
Under-tightening |
Insufficient bond strength, loose joint |
Wrong threadlocker type |
Premature failure, difficulty in disassembly |
Non-metallic surfaces |
Adhesive bond failure |
Dirty or oily threads |
Weak bond, potential failure |