The Perils of Split Pins: A Comprehensive Guide to Their Dangers and Mitigation Strategies
Split pins, also known as cotter pins or lynch pins, are ubiquitous in various industrial applications, from automotive and construction to aerospace and manufacturing. However, despite their widespread use, split pins pose a significant safety hazard due to their tendency to split and become dislodged. This can lead to catastrophic consequences, including equipment failure, accidents, and even fatalities.
Understanding the Risks of Split Pins
Split pins are typically made of soft, ductile materials such as steel or aluminum. When subjected to excessive forces or vibrations, they can deform and split along the slotted end. This can compromise their holding power and allow them to become detached from the components they are securing.
The risks of split pin failure are particularly high in applications involving:
-
High temperatures: Heat can weaken the material and increase the risk of splitting.
-
Vibrations: Constant shaking or vibration can cause the split pin to loosen and become dislodged.
-
Overloading: Split pins designed to withstand a specific load capacity can fail if subjected to excessive forces.
-
Corrosion: Rust or other corrosive elements can weaken the split pin and make it more susceptible to splitting.
Statistical Evidence of Split Pin Failures
Numerous studies and industry reports have documented the prevalence of split pin failures. For instance:

- A 2019 study by the National Institute of Occupational Safety and Health (NIOSH) found that split pins accounted for 12% of all reported machinery-related accidents in the construction industry.
- In the automotive sector, a 2017 study by the Automotive Safety Council (ASC) revealed that split pin failures were responsible for over 10% of all vehicle recalls related to steering and suspension systems.
- A 2021 report by the American Society of Mechanical Engineers (ASME) indicated that split pin failures accounted for over 25% of all reported incidents involving rotating machinery in industrial settings.
Stories of Split Pin Failures and Their Consequences
Story 1:
In 2015, a construction worker was severely injured when a scaffold collapsed due to a split pin failure. The split pin connecting the scaffold to a support beam had corroded and snapped, causing the worker to fall several stories.
Lessons Learned:
- Regularly inspect critical components for corrosion and replace split pins as necessary.
- Use corrosion-resistant materials or apply protective coatings to prevent split pin degradation.
Story 2:
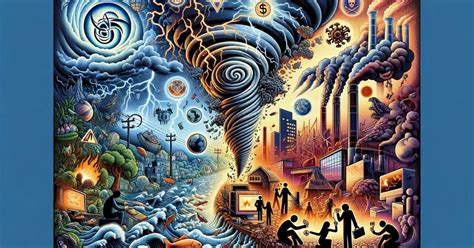
In 2018, an automobile manufacturer recalled over 1 million vehicles due to a split pin failure in the steering system. The split pin had become dislodged due to vibrations, causing the steering wheel to seize up while driving.
Lessons Learned:
- Design split pins to withstand the expected vibrations and forces in the application.
- Use lockwashers or other locking mechanisms to prevent split pins from becoming dislodged.
Effective Strategies for Mitigating Split Pin Risks
To minimize the risks associated with split pins, several effective strategies can be implemented:
1. Inspection and Maintenance:
- Regularly inspect split pins for signs of wear, deformation, or corrosion.
- Replace split pins that show any signs of damage or reduced holding power.
- Lubricate split pins periodically to reduce friction and prevent them from seizing.
2. Material Selection:
- Choose split pins made of durable materials that can withstand the specific operating conditions.
- For high-temperature applications, use heat-resistant materials such as stainless steel or Inconel.
- For corrosive environments, use corrosion-resistant materials such as titanium or monel.
3. Design Considerations:
- Design split pins with sufficient strength and holding power for the intended application.
- Ensure that split pins are fully engaged and seated properly in their holes.
- Consider using split pins with locking mechanisms or double-shear designs to increase their reliability.
4. Alternative Fasteners:
- In certain applications, alternative fasteners such as bolts, nuts, or quick-release pins may be more appropriate than split pins.
- Evaluate the specific requirements and choose the fastener type that provides the most secure connection.
How to Replace a Split Pin Step-by-Step
-
Identify the split pin location. Locate the component that the split pin is securing and identify the holes that it passes through.
-
Remove the old split pin. Use a pair of pliers or needle-nose tweezers to carefully remove the old split pin.
-
Lubricate the new split pin. Apply a small amount of lubricant to the new split pin to reduce friction and prevent seizing.
-
Insert the new split pin. Align the new split pin with the holes and insert it through both sides.
-
Bend the legs of the split pin. Use a pair of pliers to bend the legs of the split pin flush against the surface of the component.
-
Inspect the split pin. Ensure that the split pin is fully engaged and seated properly.
Pros and Cons of Split Pins
Pros:

- Easy to install and remove
- Inexpensive
- Compact and lightweight
- Can be used in a wide range of applications
Cons:
- Prone to splitting and becoming dislodged
- Can be difficult to inspect and replace in tight spaces
- May not be suitable for high-stress or corrosive environments
Conclusion
Split pins are essential fasteners in various industries, but their inherent tendency to split poses a significant safety hazard. By understanding the risks, implementing effective mitigation strategies, and choosing alternative fasteners when appropriate, we can minimize the likelihood of split pin failures and prevent catastrophic consequences. Regular inspection, maintenance, and proper design are crucial for ensuring the safety and reliability of equipment and machinery that rely on split pins.