The Indispensable Guide to Pins and Cotters: Ensuring Safety and Efficiency
Introduction
Pins and cotters are essential mechanical components used to secure and align various parts in machinery, vehicles, and structures. Their ability to prevent unintended movement and maintain the integrity of mechanical assemblies makes them indispensable in a wide range of industries. This comprehensive guide will delve into the world of pins and cotters, exploring their types, applications, and best practices for their effective use.
Types of Pins and Cotters
The vast array of pins and cotters available offers solutions for diverse engineering challenges. Here are some common types:
Pins
-
Cylindrical Pins: These pins are cylindrical in shape and can be solid, hollow, or slotted. They are often used to align and position parts, such as shafts and gears.
-
Tapered Pins: As the name suggests, these pins have a tapered shape that allows for a secure fit in tapered holes. They are commonly used to secure gears and pulleys.
-
Dowel Pins: Dowel pins have a cylindrical shape with a knurled or serrated surface. They are used to align and prevent rotation of two parts.
-
Spring Pins: Spring pins are cylindrical and made of spring steel. They are designed to provide a spring force when inserted into a hole, securing the parts without the need for additional fasteners.
Cotters
-
Split Cotters: These cotters are split along their length and are inserted through a hole in a bolt or screw. The ends are spread apart, providing a mechanical lock against the nut or head of the fastener.
-
Tapered Cotters: Similar to tapered pins, tapered cotters have a wedge-shaped design. They are driven into a tapered hole to secure shafts and prevent movement.
-
Flat Cotters: Flat cotters, also known as gibs or keys, are rectangular in shape and are used to prevent axial movement or rotation of shafts or gears.
Applications of Pins and Cotters
Pins and cotters find application in countless industries, including:

-
Automotive: Securing suspension components, steering systems, and engine parts
-
Aerospace: Ensuring the reliability of aircraft structures and engines
-
Construction: Securing bolts and fasteners in bridges, buildings, and other structures
-
Manufacturing: Aligning and positioning parts in machinery, tools, and equipment
-
Agriculture: Securing blades, shafts, and other components in farm machinery
Benefits of Using Pins and Cotters
The use of pins and cotters offers numerous benefits, such as:
-
Security: Pins and cotters provide a secure connection, preventing unintended movement and maintaining the integrity of assemblies.
-
Alignment: They ensure proper alignment of components, reducing wear and tear.
-
Cost-effectiveness: Pins and cotters are relatively inexpensive compared to other fastening methods.
-
Simplicity: They are easy to install and remove, making maintenance and repairs less time-consuming.
-
Versatility: The wide range of available types and sizes makes them suitable for a vast array of applications.
Best Practices for Use
To ensure the optimal performance and longevity of pins and cotters, it is essential to follow these best practices:
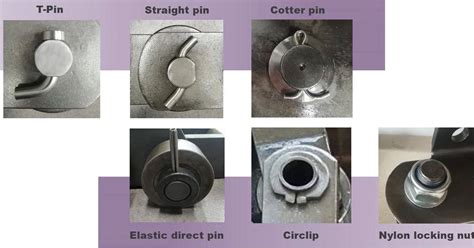
-
Correct Size: Always use the correct size pin or cotter for the specific application.
-
Proper Installation: Ensure that the pin or cotter is fully inserted and securely locked into place.
-
Lubrication: Lubricate pins and cotters to minimize friction and wear.
- ** регулярная проверка:** Regularly inspect pins and cotters for signs of damage or wear.
-
Replacement: Replace pins and cotters immediately if they show signs of fatigue or failure.
Common Mistakes to Avoid
Avoiding common mistakes is crucial for the safe and effective use of pins and cotters:
-
Overtightening: Excessive torque can damage the pin or cotter, leading to failure.
-
Using the Wrong Type: Selecting the wrong type of pin or cotter for the application can compromise the integrity of the assembly.
-
Improper Installation: Incomplete insertion or insecure locking can result in movement or failure.
-
Ignoring Maintenance: Neglecting regular inspections and lubrication can lead to premature wear and failure.
-
Reusing Old Pins and Cotters: Reusing damaged or worn pins and cotters is a safety hazard and should be avoided.
Step-by-Step Approach to Using Pins and Cotters
Follow these steps for the proper installation of pins and cotters:

-
Select the Correct Size: Determine the appropriate size pin or cotter based on the hole diameter and the thickness of the parts to be secured.
-
Prepare the Hole: Clean and deburr the hole where the pin or cotter will be inserted.
-
Lubricate: Apply a thin layer of lubricant to the pin or cotter to reduce friction.
-
Insert the Pin or Cotter: Carefully insert the pin or cotter into the hole, ensuring it is fully seated and aligned.
-
Secure the Pin or Cotter: For split cotters, spread the ends apart using a cotter pin spread