The Crimping Tool: An Essential Guide for Electrical Professionals and DIYers
In the realm of electrical engineering and DIY projects, the crimping tool reigns supreme. It's a versatile handheld equipment that enables secure and efficient connections between wires and electrical components.
Understanding the Basics of Crimping Tools
Crimping, in essence, involves joining two or more conductors together by compressing a metal sleeve or connector around them. This permanent connection ensures a reliable and low-resistance path for electrical current.
Crimping tools come in various shapes and sizes, each designed for specific types of connectors and wires.
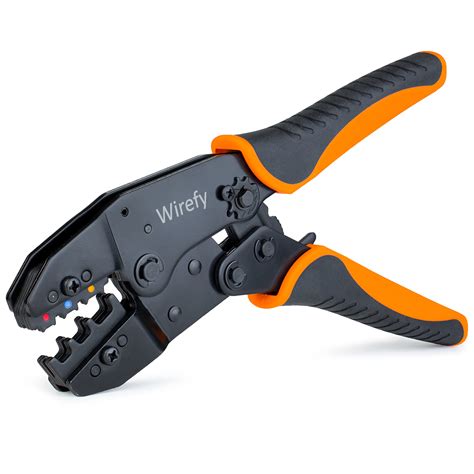
Types of Crimping Tools
-
Handheld crimping pliers: Manual tools operated by squeezing handles together to crimp connectors.
-
Hydraulic crimping tools: Powered by a hydraulic pump to generate greater force for crimping larger connectors.
-
Ratchet crimping tools: Utilize a ratcheting mechanism to ensure consistent crimping force.
-
Stripping and crimping tools: Multifunctional tools that both strip and crimp wires in one operation.
Choosing the Right Crimping Tool
Selecting the appropriate crimping tool depends on several factors:
-
Wire type: Different wire gauges and insulation types require specific crimping dies.
-
Connector type: The shape and size of the connector determine the required die profile.
-
Crimping force: The tool's force rating should match the specifications of the connector.
-
Ergonomics: Consider the comfort and ease of use of the tool, especially if prolonged use is anticipated.
How to Use a Crimping Tool
Using a crimping tool effectively requires proper technique:
-
Prepare the wires: Strip the wires to expose the bare conductors.
-
Position the connector: Insert the wires into the connector and align them correctly.
-
Insert into the crimping tool: Place the connector with the wires into the appropriate die.
-
Crimp the connector: Squeeze or activate the tool to crimp the metal sleeve onto the wires.
-
Inspect the crimp: Verify the crimp is secure and meets the electrical code specifications.
Troubleshooting Crimping Problems
Despite careful execution, occasional crimping problems can arise:

-
Loose crimp: Inspect the crimp for incomplete or misaligned connections.
-
Damaged wire insulation: Ensure the crimping tool is not causing damage to the wire insulation.
-
Incorrect connector: Verify that the connector and die are compatible with the wire type and size.
-
Insufficient force: Use a crimping tool with a higher force rating or adjust the setting.
Safety Precautions for Crimping
When working with crimping tools, safety should be paramount:
-
Wear safety glasses: Flying metal fragments can occur during crimping.
-
Insulate exposed wires: Handle live wires with caution and ensure they are properly insulated.
-
Inspect tools regularly: Check for damaged handles, dies, or wires before each use.
-
Follow manufacturer's instructions: Refer to the tool's user manual for specific operating instructions and safety precautions.
Types of Crimp Connectors
A wide range of crimp connectors exist, each designed for specific applications:


-
Insulated crimp terminals: Used for connecting wires to terminals or other electrical components, such as relays or switches.
-
Butt connectors: Join two wires together end-to-end.
-
Ring terminals: Crimped onto wires and installed under the head of screws or bolts.
-
Fork terminals: Similar to ring terminals but with a forked shape for easier installation on terminal blocks.
-
Splice connectors: Join multiple wires together in a watertight connection.
Applications of Crimping Tools
Crimping tools are indispensable in various electrical applications:
-
Electrical wiring: Connecting wires in electrical panels, switches, and outlets.
-
Automotive electrical: Crimping connectors for wires in car audio systems, lighting, and engine components.
-
Telecommunications: Creating secure connections in cabling for phone lines and data networks.
-
Appliance repair: Replacing damaged connectors in appliances such as refrigerators, microwaves, and dishwashers.
-
Robotics and automation: Crimping connectors for wires in industrial control systems and automated machinery.
Crimping Tool Market Landscape
According to market research firm Grand View Research, the global crimping tool market was valued at USD 2.88 billion in 2021 and is projected to reach USD 4.52 billion by 2030, exhibiting a CAGR of 5.3% during the forecast period.
The growth is attributed to surging demand from the electrical and electronics industry, particularly in automotive, telecommunications, and consumer electronics.
Top Crimping Tool Manufacturers
Several reputable manufacturers produce high-quality crimping tools:
-
Klein Tools: Renowned for its durable and reliable hand tools.
-
Fluke: Known for precision instruments and test equipment, including crimping tools.
-
Panduit: Specializes in network infrastructure solutions, including crimping tools for data cabling.
-
Thomas & Betts: A leading manufacturer of electrical components and crimping tools.
-
Molex: Global supplier of electronic connectors and crimping tools.
Stories and Lessons Learned
Story 1:
Electrician Misdiagnoses Crimp Problem:
An electrician was troubleshooting a faulty light fixture and suspected a loose crimp connection. However, after inspecting the crimp, he realized that the problem was actually a damaged wire inside the fixture. This highlights the importance of thorough troubleshooting to avoid misdiagnosis.
Lesson Learned:
Always investigate all potential causes of electrical problems before assuming a faulty crimp connection.
Story 2:
Improper Crimp Causes Electrical Fire:
A homeowner attempted to repair a faulty outlet using an undersized crimping tool. The crimps were not secure, resulting in overheating and an electrical fire. This incident underscores the importance of using the correct tools for the job.
Lesson Learned:
Ensure the crimping tool you use matches the specifications of the electrical components you are working with.
Story 3:
Loose Crimp Leads to Equipment Failure:
In a manufacturing plant, a loose crimp connection caused an industrial motor to malfunction, halting production. The company lost valuable time and revenue due to the faulty crimp. This example emphasizes the critical role of secure crimps in preventing equipment failures.
Lesson Learned:
Regular maintenance and inspection of crimps are crucial to avoid costly equipment downtime.
Effective Strategies for Crimping
-
Use high-quality crimp connectors: Choose connectors that meet industry standards and are compatible with the wires and crimping tool.
-
Prepare wires properly: Ensure wires are stripped to the correct length and free of insulation damage.
-
Inspect crimping tools regularly: Check for damaged dies, loose handles, or frayed wires.
-
Calibrate crimping tools: Follow manufacturer's instructions to calibrate the tool to the correct force setting.
-
Use a sturdy crimping surface: Provide a stable base to support the crimping tool and prevent uneven crimps.
Tips and Tricks for Crimping
-
Use a visual inspector: A visual inspector can help verify the quality of crimps and detect any potential issues.
-
Practice on scrap wire: Practice crimping on scrap wire before working on live electrical components.
-
Inspect both sides of the crimp: Check the crimp from both sides to ensure it is secure and complete.
-
Don't overcrimp: Excessive crimping can damage the connector or wire insulation.
-
Replace damaged dies: Worn or damaged dies will result in poor-quality crimps. Replace them promptly.
Call to Action
To ensure reliable and safe electrical connections, invest in a high-quality crimping tool and master the techniques discussed in this guide. By following these practices, you can minimize the risk of electrical problems, prevent equipment failures, and create secure and lasting electrical connections.