**Unleash the Power of TORX: A Comprehensive Guide to the Ultimate Fastening Solution**
Introduction
In the realm of fasteners, TORX stands tall as the pinnacle of performance, reliability, and user-friendliness. Renowned for its distinctive star-shaped recess, TORX offers a slew of advantages that have made it a trusted choice for engineers, manufacturers, and consumers alike. This comprehensive guide will delve into the depths of TORX, exploring its history, technical specifications, applications, and best practices.
History of TORX
The TORX design was conceived in 1967 by Camcar Screw & Mfg., a subsidiary of Textron Inc. Driven by a desire to create a fastener that could withstand the rigors of industrial applications, Camcar engineers sought to eliminate the drawbacks of traditional slotted and Phillips head screws.

Advantages of TORX Over Slotted and Phillips Head Screws
TORX screws possess several key advantages over slotted and Phillips head screws, including:
-
Increased driving torque: The star-shaped recess allows for greater torque transfer, minimizing the risk of stripping or cam-out.
-
Improved ergonomics: The position of the recess enables users to apply force directly downward, reducing strain on wrists and hands.
-
Reduced bit wear: The geometry of the recess minimizes wear and tear on driver bits, extending their lifespan.
-
Tamper-resistance: The unique shape of the recess makes it difficult to remove the screw without a specialized driver, enhancing security.
Technical Specifications
TORX screws are defined by a set of standard sizes and drive profiles. The size of a TORX screw is designated by a number, with larger numbers indicating a larger screw. Common TORX screw sizes range from T5 to T40.
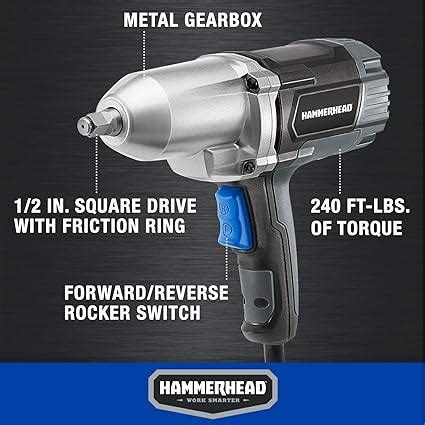
Types of TORX Drive Profiles
TORX screws are available in several drive profiles, each with its own characteristics:
-
TORX: The standard TORX profile is used in a wide range of applications, offering a good balance of torque transfer and ease of use.
-
TORX Plus: An enhanced version of the standard TORX profile, TORX Plus provides even greater torque transfer and cam-out resistance.
-
TORX Tamper-Resistant: This profile features a pin in the center of the recess, requiring a specialized driver bit for removal.
Applications
TORX screws are extensively utilized in a diverse range of industries and applications, including:
-
Automotive: Engine components, transmissions, body panels
-
Electronics: Computers, smartphones, consumer electronics
-
Construction: Roofing, framing, hardware
-
Industrial equipment: Machinery, tools, conveyors
-
Aerospace: Aircraft structures, engines, landing gear
Benefits of TORX Screws in Different Applications
In each of these applications, TORX screws offer unique benefits:

-
Automotive: High torque transfer and cam-out resistance ensure reliable performance in demanding engine and transmission components.
-
Electronics: Compact size and ease of use make TORX screws ideal for delicate electronics assemblies.
-
Construction: Durability and tamper-resistance provide peace of mind in construction projects.
-
Industrial equipment: Increased torque transfer and reduced bit wear extend the lifespan of critical machinery.
-
Aerospace: The ability to withstand extreme loads and vibrations make TORX screws essential for aircraft applications.
Best Practices for Using TORX Screws
To maximize the benefits of TORX screws, it is essential to follow these best practices:
-
Use the correct driver: Always use a driver bit that is specifically designed for the size and profile of the TORX screw.
-
Apply downward pressure: Hold the driver perpendicular to the screw and apply firm downward pressure during installation and removal.
-
Avoid overtightening: Excessive torque can damage the screw or strip the threads.
-
Lubricate threads: In certain applications, a small amount of lubricant can reduce friction and ensure smooth installation.
-
Inspect regularly: Periodically check TORX screws for any signs of wear or damage to maintain optimal performance.
Common Mistakes to Avoid
To avoid common pitfalls when using TORX screws, pay attention to the following:
-
Using the wrong driver: Using an incorrect driver can strip the screw head or damage the driver bit.
-
Applying excessive torque: Overtightening can lead to screw failure or damage to the mating surfaces.
-
Inserting the screw at an angle: This can result in cross-threading, which can weaken the joint.
-
Mixing different types of TORX screws: Using screws with different drive profiles or sizes in the same application can lead to inconsistencies.
-
Using worn or damaged screws: Old or damaged screws may not perform reliably and should be replaced.
How to Use TORX Screws Step-by-Step
Follow these steps for proper installation and removal of TORX screws:
Installation:
-
Select the correct screw: Choose a screw that is the appropriate size and drive profile for your application.
-
Prepare the hole: If necessary, drill a pilot hole slightly smaller than the screw's diameter to prevent splitting.
-
Apply lubricant: If desired, apply a small amount of lubricant to the screw threads.
-
Insert the screw: Hold the driver perpendicular to the screw and insert it into the recess.
-
Apply downward pressure: Apply firm downward pressure while slowly turning the driver clockwise.
-
Tighten the screw: Tighten the screw until it is snug. Avoid overtightening.
Removal:
-
Select the correct driver: Choose a driver bit that is specifically designed for the size and profile of the screw.
-
Insert the driver: Hold the driver perpendicular to the screw and insert it into the recess.
-
Apply downward pressure: Apply firm downward pressure while slowly turning the driver counterclockwise.
-
Unscrew the screw: Continue turning the driver until the screw is completely removed.
Stories and Lessons Learned
To illustrate the practical benefits of TORX screws, let's explore a few stories and the lessons we can learn from them:
Story 1: The Power Plant Upgrade
A major power plant was facing downtime due to recurring failures of fasteners used in their turbine assemblies. After replacing the fasteners with TORX screws, the downtime was significantly reduced, resulting in substantial cost savings and increased plant efficiency.
Lesson: TORX screws can improve reliability and reduce maintenance costs in demanding industrial applications.

Story 2: The Assembly Line Revolution
A manufacturing company implemented TORX screws on their assembly lines. The ergonomic benefits of TORX screws led to a reduction in worker fatigue and injuries, while the increased ease of use resulted in a significant increase in productivity.
Lesson: TORX screws can enhance worker safety and productivity in high-volume assembly environments.
Story 3: The Aircraft Disaster Averted
A near-catastrophic incident was prevented when a loose screw on an aircraft wing was discovered during a routine inspection. The screw was successfully removed using a TORX driver, avoiding a potential disaster.
Lesson: TORX screws provide peace of mind in critical applications where the integrity of fasteners is essential.
Tips and Tricks
To maximize the effectiveness of TORX screws, consider the following tips and tricks:
-
Use quality screws: Invest in high-quality TORX screws to ensure consistent performance and durability.
-
Match screw size to application: Choose the appropriate screw size for the thickness and strength requirements of the materials being fastened.
-
Drill pilot holes: Pre-drilling pilot holes can prevent wood splitting and ensure proper screw alignment.
-
Lubricate before installation: A small amount of lubricant can reduce friction and make installation easier.
-
Use a torque wrench: For precise torque control, use a torque wrench to tighten screws to the manufacturer's specifications.
Conclusion
TORX screws stand as a testament to the power of innovation and engineering excellence. Their superior performance, reliability, and ease of use have made them the preferred choice for a wide range of applications, from delicate electronics to heavy-duty machinery. By adhering to best practices and implementing the tips and tricks discussed in